Should I Purchase OEM or Aftermarket Air Compressor Parts?
While most industrial air compressor users understand the importance of purchasing original equipment manufacturer (OEM) compressor parts for major air compressor repairs and replacements, they are often tempted by the lower price of aftermarket parts when purchasing consumables, such as filters and oils, that are used during preventive maintenance activities. This blog will discuss how to choose between OEM and aftermarket consumable air compressor parts so you can make informed purchasing decisions.
Why OEM Compressor Parts are Best for Major Repairs
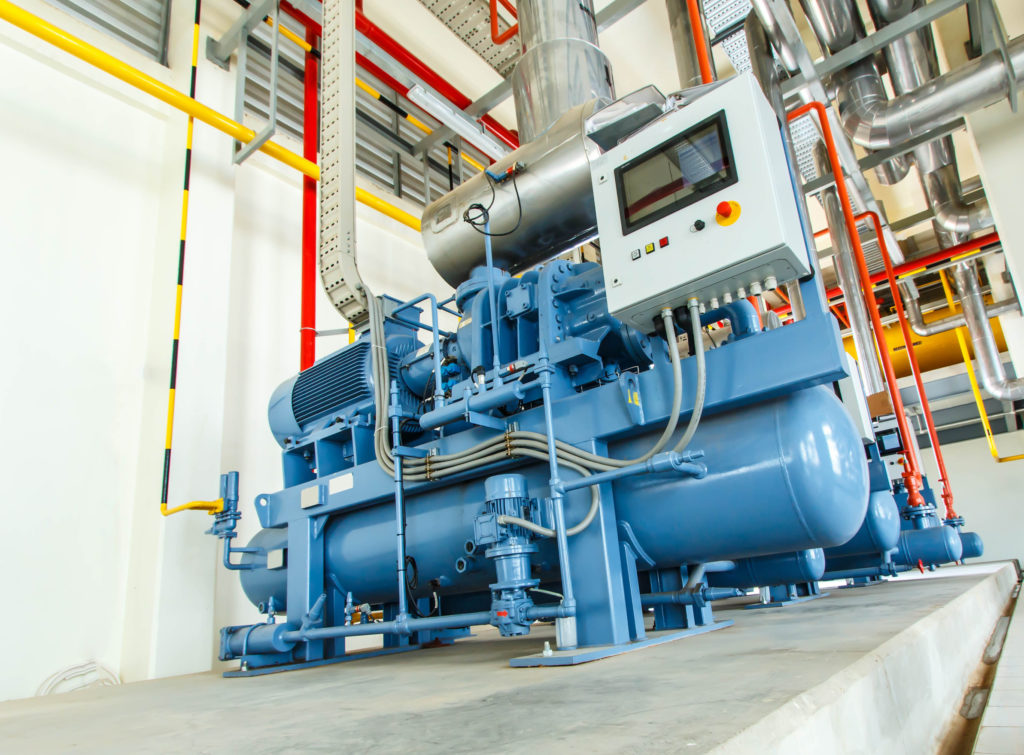
However, before discussing consumable air compressor parts used for preventive maintenance, we’ll provide a brief review of the importance of purchasing genuine OEM compressor parts, such as motors and coolers for major repairs.
When it comes to major repairs, OEM air compressor parts are always the smarter choice for several reasons, including:
- Improved durability: OEM compressor parts are made with higher-quality materials, engineered to exact specifications and rigorously quality tested to ensure performance, so are likely to be more durable in operation than generic aftermarket replacement parts.
- Increased efficiency: Genuine OEM compressor parts are designed and tested for optimal performance so will provide higher levels of operating and energy efficiency than aftermarket air compressor parts that are not specifically engineered for the industrial air compressor in which they are placed.
- Optimized operation: Because OEM air compressor parts are manufactured under tight tolerances and are tested to guarantee quality and function, they provide optimized operation, higher levels of reliability and greater levels of manufacturing efficiency.
- Maintain the Warranty: It is often the case that the use of third-party aftermarket parts will void the original warranty of an industrial air compressor, so it is recommended to purchase and install OEM compressor parts for major repairs.
What About Consumable Air Compressor Parts for Preventive Maintenance?
Preventive maintenance plays an essential role in the performance, efficiency and lifespan of an industrial air compressor. And, as part of a solid preventive maintenance program, filter changes and lubrication should be performed on a regular basis as specified by the air compressor manufacturer.
However, the frequent purchase of OEM air filters and air compressor oil can really add up, so many industrial air compressor users want to know how to choose between consumable OEM compressor parts and their aftermarket competitors. We will take a look here.
OEM Air Filters vs. Aftermarket Air Filters
Air compressor air filters are intended to remove contaminants from the air compressor system so they do not cause damage to components or reduce the efficiency of the system, making them a critical air compressor part, and changing them on a regular basis is an essential part of preventive maintenance. For this reason, any air compressor filter used in the system should be of the highest quality and performance level to protect your equipment investment and to ensure the greatest levels of performance and efficiency.
OEM air filters are guaranteed to provide the same fit and performance level as original air compressor air filters. Aftermarket air filters may offer the same size, will be designed to fit in the same filter enclosure and will, undoubtedly, have a reduced upfront cost.
However, there are likely to be differences between OEM air filters and aftermarket air filters. The best way to compare the performance of OEM vs. aftermarket air compressor filters is to find comparable products from suppliers that provide data sheets and take the time to closely examine the specifications.
Compare the air quality ratings to ensure that both products use the same standard and then examine the performance level that the filter is expected to provide. If air quality is essential to your operation, selecting an OEM air filter is the better choice since the air quality testing is likely to be more rigorous, accurate and accountable.
Another important comparison is the pressure drop rating as it directly impacts the efficiency of the air compression system, which in turn influences energy consumption. (Keep in mind that electricity is one of the highest operational costs of air compressor ownership.) Often, even aftermarket air filters that provide the same fit will have a higher pressure drop rating than OEM air filters. If this is the case, saving a few dollars on an aftermarket air filter can end up costing thousands of dollars per year in electricity bills.
The rate of saturation, which is how quickly the filter fills with contamination, is another important consideration as it will affect pressure drop and air quality. Often aftermarket air filters that offer an equivalent pressure drop rating may become soiled more quickly and need to be changed more often because they don’t offer the correct surface area. In these cases, what seems like a bargain can end up costing more due to more frequent filter changes.
It is also important to compare the filter membrane size, as the wrong membrane size may permit the passage of larger particles, which could damage system components or the quality of the produced air.
And, finally, the use of aftermarket air filters may void the warranty of the air compressor, it may impact the warranty of the air dryer or other system components, so it is essential to check all warranties before deciding to purchase an aftermarket air filter instead of an OEM air filter.
Is OEM Air Compressor Oil Really Better than Aftermarket?
Air compressor oil is a crucial part of the performance of the overall system. However, the use of poorly performing lubricants can result in damaging wear and friction, limited operational range, reduced cooling capacity, corrosion, higher energy consumption, clogged filters and other unwanted issues. So, it’s important to purchase the best air compressor oil available.
That said, many replacement lubricants are engineered to provide equivalent performance to OEM lubricants and use the same high-quality base stock and additives as OEM air compressor oil, which means purchasing them at a lower cost has the potential to save users some money without sacrificing performance.
However, OEM air compressor oils are optimized for the system for which they are intended, so they may provide several benefits when compared to aftermarket lubricants, such as the ability to withstand higher pressures and temperatures, higher levels of performance and efficiency and less frequent replacement, which will decrease long-term maintenance costs. OEM air compressor oil is usually required for manufacturers extended warranties also.
With that in mind, when choosing replacement oils, it is crucial that the selected lubricant is fully compatible with the system. Important characteristics include flashpoint, viscosity index, oxidative stability and pour point. If you opt for a generic air compressor oil, ensure that these specifications meet the manufacturer’s specifications and that the base stocks and additives are the same as the OEM air compressor oil.
When in doubt about a replacement air compressor part, air compressor air filter or air compressor oil’s compatibility with your system, please reach out to JHFOSTER, a Tavoron company, for selection guidance. We are here to help.