Reducing Frictional Resistance in Linear Guides
Linear guides are specified in applications, such as robotics, medical equipment, imaging devices, 3D printers and CNC machines, where it is essential that the device provides straight, linear motion that is as smooth and precise as possible. To achieve the necessary level of fluent motion, the selected linear guide should feature low-friction materials and designs that are optimized for smooth motion and easy lubrication. This blog will discuss how properly designed linear guides minimize frictional resistance, as well as maintenance best practices that will enhance performance in critical applications.
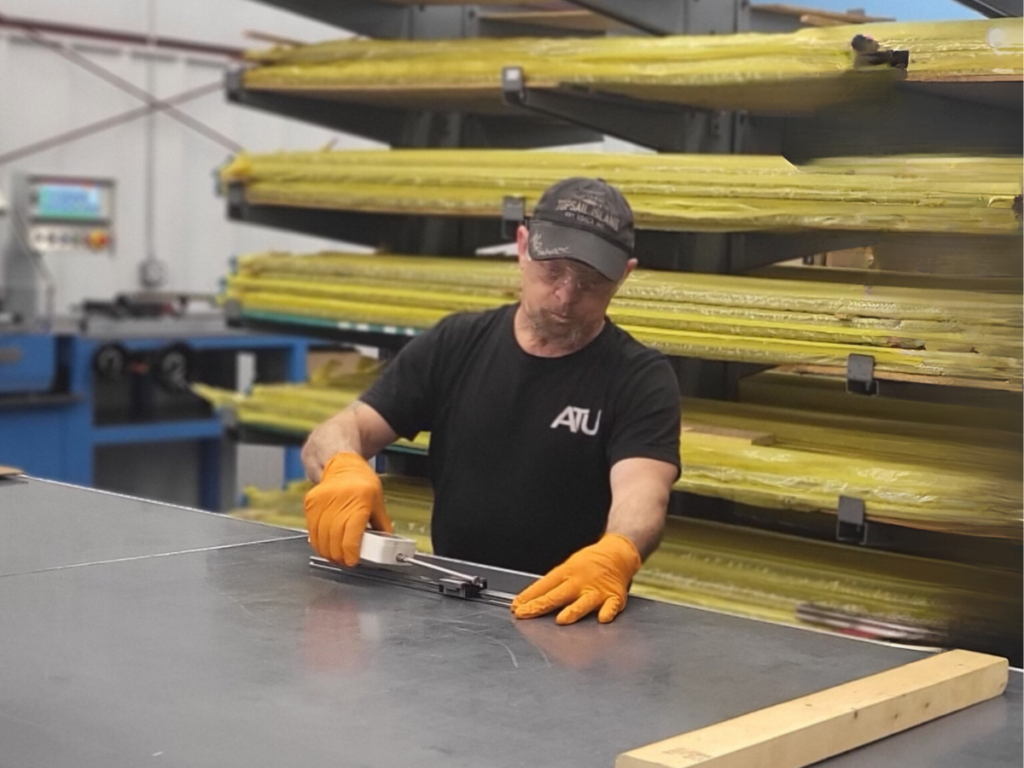
What is a Linear Guide?
Linear guides are mechanical systems that support, carry and contain a load along a single axis to provide smooth, low-friction motion in applications that require highly precise, straight-line movement where deviation from the assigned path is not permissible.
To support the necessary frictional resistance, the design of linear guides differs from that of other linear motion devices such as linear actuators. Typically, linear guides, also called linear guide rails, include a linear base, a slider and ball or roller bearings. The slider is attached to the moving component and the linear base is mounted to a stationary surface.
It is the addition of the ball or roller bearings that reduce frictional resistance between the slider and the linear bearings, as well as the high levels of precision and accuracy to micrometers afforded by linear guides.
To enable use in a variety of applications, there are several linear guide designs available, including:
- Recirculating ball linear guides: This type of linear guide contains linear ball bearings, carriages and guideways capable of supporting long distances between support points, as well as smooth, unlimited travel.
- Ball chain linear guides: In this design, the ball track and ball chain systems ensure that the balls do not come in contact with each other to reduce friction and noise while still permitting precise, fast straight-line motion
- Roller Linear Guides: It consists of a rail and a carriage assembly, where rollers (cylindrical) are used instead of traditional ball bearings to guide the movement of the carriage along the rail. These rollers typically have a larger contact area with the rail, allowing for higher load capacities and better resistance to lateral forces compared to ball-type linear guides.
Innovations in Linear Guide Designs
Because there is a growing demand for automated equipment, such as robots, medical devices, 3D printers and imaging machines, that achieves accurate, repeatable and smooth linear motion, there have been several developments in the materials, coatings and designs used in linear guides.
Often in the design of linear guides, the linear guide rails are constructed of low-friction materials that facilitate rolling, such as high-strength steel that is shaped and profiled to the necessary specifications. Steel is used because it resists corrosion and cracking, so it remains strong and stable throughout its lifetime and continues to provide low-friction movement. Linear rails can be treated with additional coatings to further resist corrosion and provide frictional resistance.
The choice of low-friction materials for the ball or roller components is also an important design factor. Bearings and rollers made from steel have a higher load capacity, as well the ability to provide precise motion, while enabling frictional resistance. However, it should be noted that regular lubrication is still needed to keep the rolling elements moving as smoothly as possible.
Linear guide carriage designs can also be enhanced to provide greater frictional resistance. For example, anti-friction mechanisms and low-friction materials can be incorporated into the design to further reduce friction. The carriages can be designed with self-lubricating properties to provide longer-term frictional resistance.
Lubrication systems are another important consideration as they are essential to keeping linear guides moving smoothly and precisely. Many linear guides are designed with an easily accessible grease nipple for quick re-lubrication, enabling the linear guide rail system to maintain its low frictional resistance and high level of accuracy.
All of these material and design considerations come together to create a linear guide rail system that provides precise and smooth motion. For example, Accu Tech’s linear guides are designed with a low-friction coefficient that enables smooth motion under strenuous loads. The frictional resistance of these linear guides is only 1/20th to 1/40th of that in a slide guide. In addition, specialized anti-friction bearings allow for high repeatability and positioning to sub-micron accuracies. The low-frictional resistance and optimized design withstand loading in all four directions. AccuTech’s linear guides include a grease nipple for easily accessible lubrication.
Maintenance Best Practices for Linear Guides
Although an optimized design contributes to the frictional resistance of the linear guide, maintenance, especially lubrication, is essential to keeping the linear guide moving as smoothly and accurately as possible in delicate applications.
Recommended lubrication techniques and schedules are available through the manufacturer or supplier of the linear guide, but a well-designed lubrication system, such as an easily accessible grease nipple, will not only make this task easier to accomplish, but it will prevent contamination of the other components as well. While each linear guide will have a different lubrication requirement, it is important to learn and adhere to the lubrication schedule to keep the liner guide in good working order.
In addition to lubrication, linear guides should be inspected and cleaned on a regular schedule. Inspections will reveal any necessary preventive maintenance activities (in addition to lubrication), as well as any issues that may cause failure, so speak with your manufacturer or supplier to determine what components should be inspected and how often.
Cleaning tasks are essential, but will also depend upon the environment in which the linear guide is installed. In extreme industrial environments where contamination is an issue, more frequent cleanings and inspections will be necessary. It may be also possible to seal the linear guide system to prolong time between cleanings in these instances.
For assistance in selecting a linear guide that provides frictional resistance, accuracy and precision for your motion control application or to learn about maintenance best practices, including lubrication, inspection and cleaning, please contact Accu Tech USA, A Tavoron company, today.