Pick and Place Automation Revolutionizes High-Speed Manufacturing
Picking up parts, precisely positioning them and setting them down is one of the most common actions in the manufacturing industry. When done manually, the process can be time consuming, mundane and inaccurate. However, pick and place automation technology performs this tedious task with high speeds and great levels of accuracy, while freeing up manual laborers to accomplish more complex and value-added tasks around the plant.
Because robotic pick and place has the ability to boost efficiency in high-speed manufacturing settings, these robots are used across an array of manufacturing sectors, including electronics, pharmaceuticals and food processing. This blog will explore the various advantages of pick and place robots and the applications in which their high speeds and precision significantly boost efficiency.
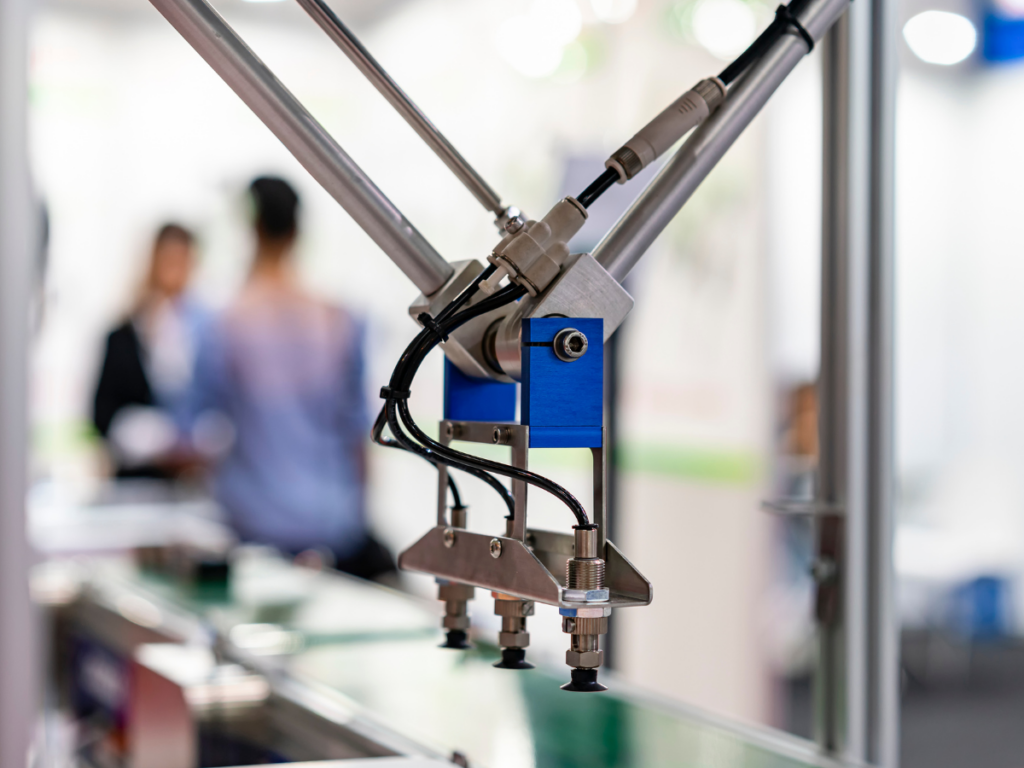
How has Robotics Changed Manufacturing?
Robotics, in general, have revolutionized the manufacturing industry by boosting efficiency, speed, safety and quality of products, and pick and place robots, one of the most applied technologies, bring to the table these same advantages.
Some of the most noteworthy benefits of swapping manual pick and pick place tasks with pick and place automation include:
Increased product quality | Pick and place robots are capable of extreme and consistent precision and accuracy when locating, manipulating and setting down workpieces. In addition, they can handle fragile and hazardous materials safely and with dexterity. These traits minimize errors, reduce waste and significantly increase finished product quality, as well as safety. |
Greater productivity | Automating repetitive pick and place activities increases the speed at which products are handled, greatly enhancing productivity and throughput. The available high speeds and precision increase quality and production rates while reducing cycle times and bottlenecks. Furthering productivity is the fact that robots can operate continuously without breaks or becoming fatigued. |
Versatility | Because many types of pick and place robots are designed to be easily reprogrammed, adaptable to different applications and can be fitted with a variety of end-of-arm tooling, they can handle different objects and accommodate changing product lines and production requirements, making them flexible and agile. |
Enhanced safety | By reducing the need for manual performance of repetitive and/or physically demanding pick and place activities, pick and place machines can help improve the safety record of a facility as the risk of injury from manually bending, lifting and twisting or working around fast-moving machinery to accomplish pick and place tasks is reduced. In addition, they can safely handle sharp or hazardous materials, reducing risks to human employees. |
Reduced costs | Installing pick and place automation helps to cut costs in a number of ways. Manual laborers can be reassigned to more complex tasks around the facility, which reduces labor costs and minimizes the costs associated with on-the-job injuries. In addition, pick and place technology helps eliminate fatigue-induced errors and inconsistencies between workers, which improves quality and reduces the cost of waste. |
Types of Pick and Place Robots
Depending on the type and speed of the pick and place application selected, these robots are capable of more than 60 cycles per minute. The ppm (parts per minute) depends on the robot’s maximum speed, move distance, dwell time and more. Thanks to technological advances, pick and place robots can be equipped with specialized end-of-arm tooling that allows them to gently grip and place even the most delicate items and the addition of vision systems allows for inspection, as well as discerning various sizes, shapes and colors.
While several types of industrial robots can be adapted for pick and place tasks, the following types are most often selected for these activities:
Cartesian
Because they can operate on multiple planes, they offer the positional accuracy needed for precision when picking and placing objects.
Depending on the number of axes, robotic arms for manufacturing can be used for simple pick and place tasks that require moving workpieces along a single path to more complex installations that involve twisting or manipulating objects before placing them down.
Delta
The parallel arms of delta robots allow for high speeds, precision and repeatability.
SCARA
Selective Compliance Assembly Robot Arm (SCARA) robots offer a compact design and can perform both linear and rotational movements, allowing them to manipulate complex shapes.
Collaborative robots
Because collaborative robots, or cobots, are specially designed to safely work alongside humans and are compact, easy to reprogram and capable of handling objects with higher speeds and greater precision than manual laborers, they make excellent pick and place robots in shared work cells or in facilities that require frequent product changes.
High-Speed Manufacturing Applications for Pick and Place Robots
Pick and place automation provides precision and boosts efficiency, so they are widely used throughout the manufacturing industry to boost efficiency, increase accuracy and reduce costs.
Some examples where pick and place machines play a role in increasing efficiency, productivity and quality include:
- General Manufacturing: The speed, agility and precision provided by pick and place robots makes them indispensable when placing parts on conveyors, handling fragile or hazardous products and reducing bottlenecks on high-speed production linens.
- Food and Beverage Manufacturing: Pick and place technology is essential in the food sector where delicate items, such as fruit and vegetables and baked goods, must be transferred from one place to another or packaged with care, as well as efficiency. They may also be used for tasks such as delicately placing chocolates into molded boxes and precisely decorating cakes. As a bonus, robots reduce the risk of contamination in food and beverage applications.
- Pharmaceutical Production: Because it offers a more hygienic option than human workers, pick and place automation is widely used in pharmaceutical production, which has strict sanitary guidelines. They offer precise placement of pills into trays and vials, packing pills in blister packs, filling or transferring syringes and other applications where sensitive materials must be accurately and consistently processed under sanitary conditions.
- Electronics Assembly: The precision granted by pick and place robots is crucial in the electronics manufacturing industry where tiny components must be accurately placed during assembly. They excel at placing glass on smartphones, delicate electrical parts in computers, circuit boards and other devices and other applications that demand precision for quality purposes. Here, too, they reduce the risk of introducing contaminants to sensitive electronic devices during production.
Robotic pick and place technologies are revolutionizing the manufacturing industry with their high speeds, accuracy and ability to handle sensitive components and products without damage. Contact JHFOSTER to discuss how a pick and place robot can be used in your application to help increase throughput, quality and safety, while reducing costs.