Maintaining a Melt Flow Indexer for Accurate Results
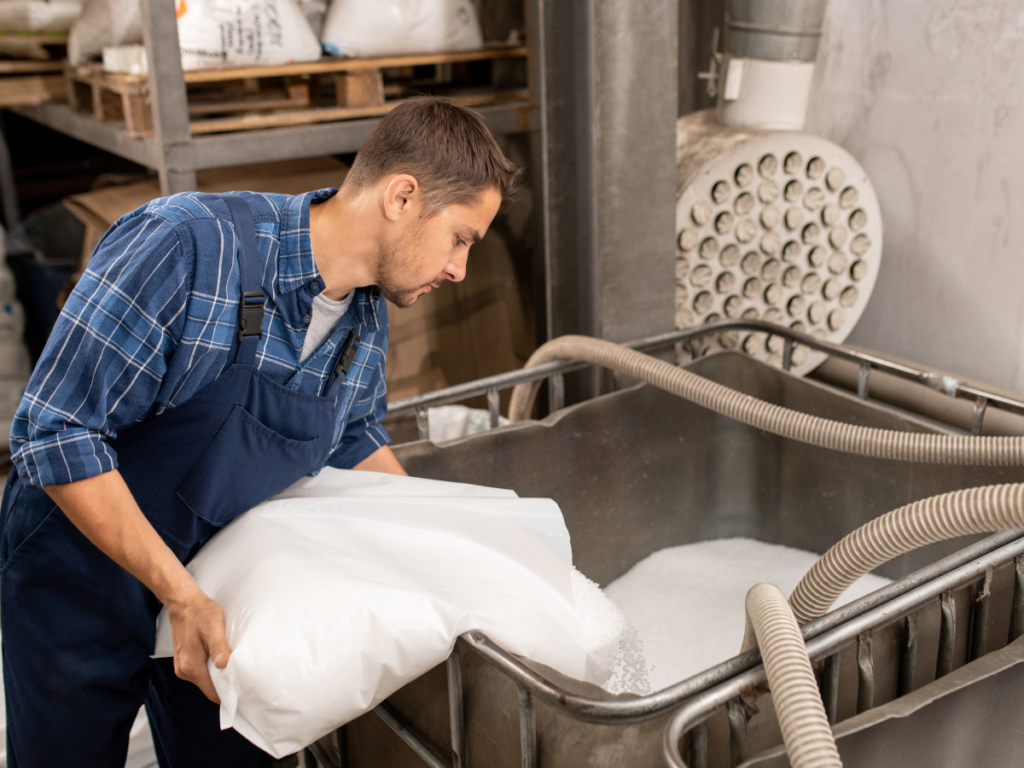
Melt Flow Index testers, also known as extrusion plastometers or Melt Flow Indexers, are used by plastic processors to determine the melt mass flow rate (MFR) and melt volume flow rate (MVR) of a plastic melted mass. The test measures the melt flow properties of virgin, compounded and post-process thermoplastics at a particular shear stress. Measurements of the flow behavior of melted materials are used to compare different grades of the same polymer, resin or material to provide quality control, for material selection and/or for the set up of processing machines by plastics producers.
Melt Flow Indexers are especially important in injection molding applications where it is essential to use the right polymer grade with an appropriate melt density and suitable temperature and pressure characteristics for a given application. Plastic extrusion applications also employ melt flow index testers to ensure that the materials to be extruded demonstrate the necessary molecular weights and viscosities during the molten stage for better control during the extrusion process.
Melt Flow Indexer Components
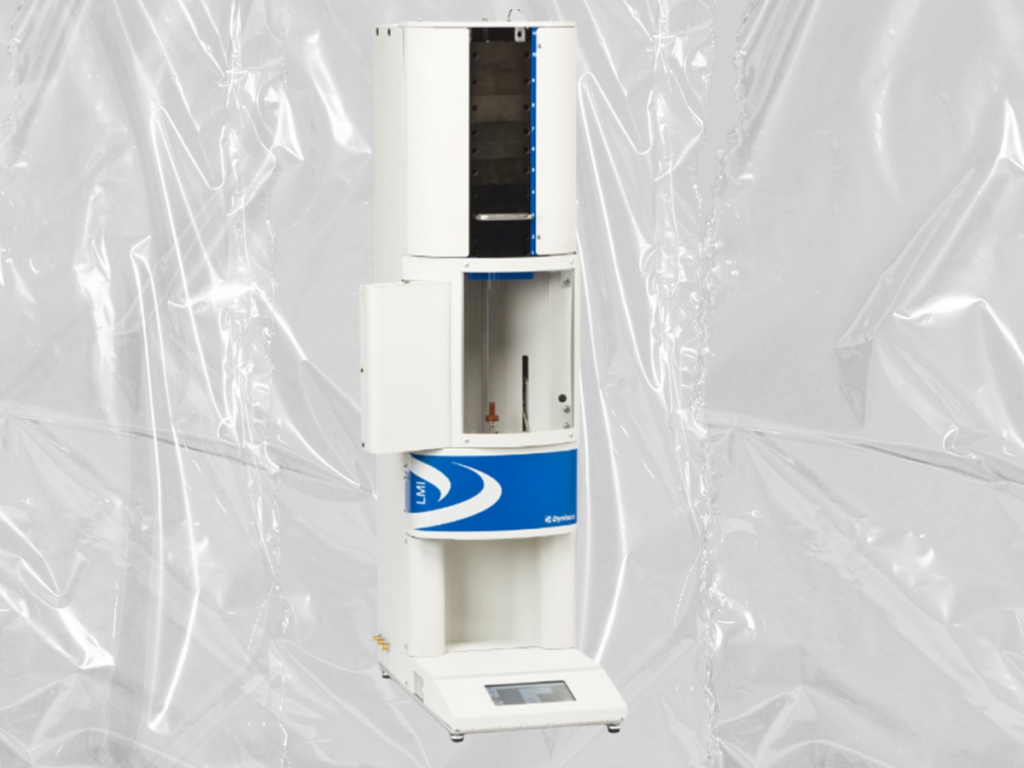
While Melt Flow Indexers can vary somewhat in design, most consist of several components, including:
- A barrel or cylinder, which is the melting chamber where the polymer being tested is heated.
- A heater, which provides the heat to the melting chamber.
- A temperature controller, which precisely controls the temperature in the barrel and can be set to varying temperatures.
- A timer, which is used for timing the test.
- A die from where the polymer under test is extruded from the barrel. It may also be called the jet or orifice.
- A die plate, which holds the extrusion die in place.
- A piston, which supplies the weight to simulate the standard conditions of the load to the sample under test.
Factors Affecting Melt Flow Test Results
It is not uncommon to have varying test results as the accuracy of a test can be affected by many factors such as how well the testing device is calibrated, the technique used by the technicians, how closely the test procedures are followed and how well the cleanliness of the testing device is maintained.
In order to ensure the best test accuracy, it’s important that the testing machine is in good working order. This means that in addition to regular calibration and validation, a visual inspection of all parts of the Melt Flow Indexer should be conducted before each test to ensure that the barrel of the instrument is level and free from rust, scratches and imperfections. The indexer should also be located in an area that is not subject to vibration or air currents as any of these things could alter test results. It is also essential that the test machine and its components are properly cleaned between each test because residue from prior tests may alter the results of the current test.
Proper Cleaning of a Melt Flow Indexer
Because cleanliness of the equipment is crucial to accurate test results, the importance of properly cleaning the machine cannot be stressed enough. The Melt Flow Indexer should be cleaned immediately following each test, which means it is likely to be extremely hot, so be mindful of this and remember that it may contain the residue of unsafe materials. For this reason protective gloves and eyewear should always be worn during cleaning and maintenance.
From there, follow these steps:
Step 1 | Any remaining test material should be purged from the machine prior to cleaning. |
Step 2 | Carefully remove the weight from the piston and set it aside. |
Step 3 | While still warm, remove the piston from the barrel and completely remove any residual material using a clean cotton rag or pad. The piston should be cleaned down to bare metal. |
Step 4 | Next, the die should be removed and cleaned using cotton pads and/or a brass brush while still warm to remove any residual plastic from the surface as well as from the center orifice. It is recommended that a special orifice cleaning tool is used for the task. Solvents or abrasives are not recommended. |
Step 5 | The barrel must also be thoroughly cleaned by repeatedly swabbing with a cotton cleaning tool. If the test material is difficult to remove, a brash brush may be used |
Step 6 | After cleaning these components, the die should be replaced in the barrel. The piston should be returned to the barrel, as well, so that it remains at the same temperature as the barrel to help ensure accuracy of the next test. |
Some manufacturers of Melt Flow Indexers provide cleaning kits with the equipment, as well as optional tools that may be purchased separately. One such manufacturer, Dynisco, also offers an informative tutorial demonstrating the cleaning process for their Melt Flow Indexer, found here.
For more information, please contact Sensors Incorporated.