IoT Predictive Maintenance Mitigates Risks Associated with Equipment Failure
While most manufacturers appreciate the positive impact IoT predictive maintenance and advanced sensor technologies can have on reducing unscheduled downtime and the associated costs, they may not recognize that the same predictive maintenance tools can be used to mitigate potential risks and hazardous operating conditions that can result when equipment fails.
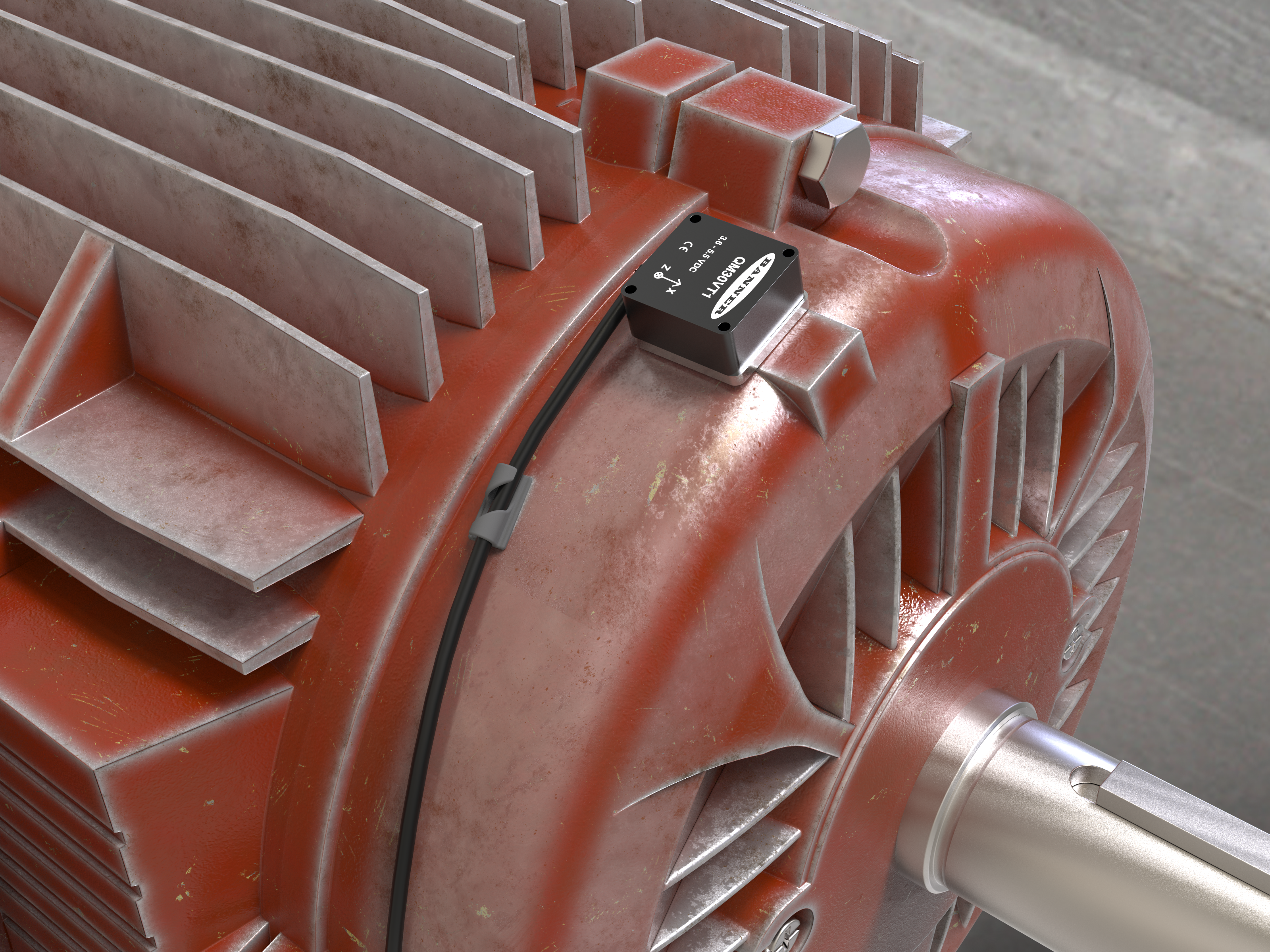
What is IoT Predictive Maintenance?
Before exploring the ways in which predictive maintenance tools can be used to identify hazardous operating conditions and mitigate the associated risks, it’s important to understand the technology and benefits associated with IoT predictive maintenance.
Today’s predictive maintenance practices involve the use of smart sensor technologies and Internet of Things (IoT) devices to monitor, in real time, the health and performance of critical equipment. Smart sensors continuously measure parameters such as vibration, temperature and other important equipment variables and, if deviations from the norm are detected, send out alerts, permitting operators and maintenance technicians to make informed decisions based on the provided data so they may take immediate corrective actions where necessary or schedule maintenance activities for a time that is more convenient and does not impact production.
Additionally, many IoT predictive maintenance solutions also involve the use of data analytics programs that assess the risk of potential equipment failures and classify them based on severity and immediacy so that users can determine which pieces of equipment are most likely to fail first and schedule accordingly. This not only ensures that the most critical machines or equipment that is most likely to fail is serviced as soon as possible, but it also ensures that labor and resources are allocated properly and that production schedules are adjusted as needed.
By using real-time data to detect and predict potential maintenance issues before catastrophic failure, these predictive maintenance tools help manufacturers minimize unscheduled downtime and significantly reduce the costs associated with lost production, labor and catastrophic equipment failure and replacement.
Using Internet of Things Monitoring to Avoid Hazardous Operating Conditions
What many manufacturers don’t realize is that these same predictive maintenance tools can be used to identify and address anomalies in machinery, such as overheating or pressure fluctuations, that can result in hazardous operating conditions that can negatively affect both equipment lifespan and safety.
For example, if a critical piece of equipment has an undetected increase in pressure, it may eventually result in an explosion, but if the sensors and Internet of Things monitoring solutions are used to detect an increase in pressure at the earliest stages, the malfunction can be identified and addressed well before hazardous operating conditions occur.
In this way, sensors and IoT technologies, make it possible to detect subtle changes in temperature, pressure, vibrations and other variables that could point to potential issues so that preventive maintenance can be scheduled before small anomalies escalate and become hazardous situations that can impact both the equipment lifespan and facility safety.
And because IoT technologies offer real-time alerts, maintenance teams are able to quickly identify any potential issues, make informed and actionable decisions and implement immediate corrective actions to avoid hazardous equipment failures and mitigate the associated risks as swiftly as possible.
Further, Internet of Things monitoring and predictive maintenance tools also allow manufacturers to prioritize maintenance activities based on hazardous equipment conditions. In other words, data can be analyzed so that high-risk or critical pieces of equipment can be monitored closely for concerning anomalies to prevent the occurrence of equipment failures that may results in hazardous operating conditions, helping to prevent accidents, create a safer manufacturing environment and extend the life of critical equipment.
In recent years manufacturers have learned that proactive maintenance is more favorable than reactive maintenance when it comes to preventing catastrophic failure, minimizing downtime and eliminating unnecessary costs. Thankfully, the same predictive maintenance tools and proactive techniques can be used to implement data-driven solutions, in which smart sensor technologies and manufacturing monitoring solutions can be used to detect, in real time, equipment performance issues and anomalies that may also result in equipment-related hazardous operating conditions and prioritize the necessary corrective actions, rather than reacting to unsafe conditions after they occur.
Because avoiding equipment failures and hazardous operating conditions are high priorities in manufacturing facilities, contact Sensor Incorporated today to learn more about how sensor technologies and manufacturing monitoring solutions can help mitigate both downtime and equipment hazards, helping to extend the operating life of critical equipment and make your facility safer, as well as more proactive, productive and profitable.