Industry 4.0 Promotes Optimized Manufacturing Operations
Industry 4.0, Connected Factory and Smart Manufacturing are all terms that get thrown around a lot in the manufacturing industry lately, but how can manufacturers begin to employ today’s smarter and more connected technologies and, more importantly, why should they?
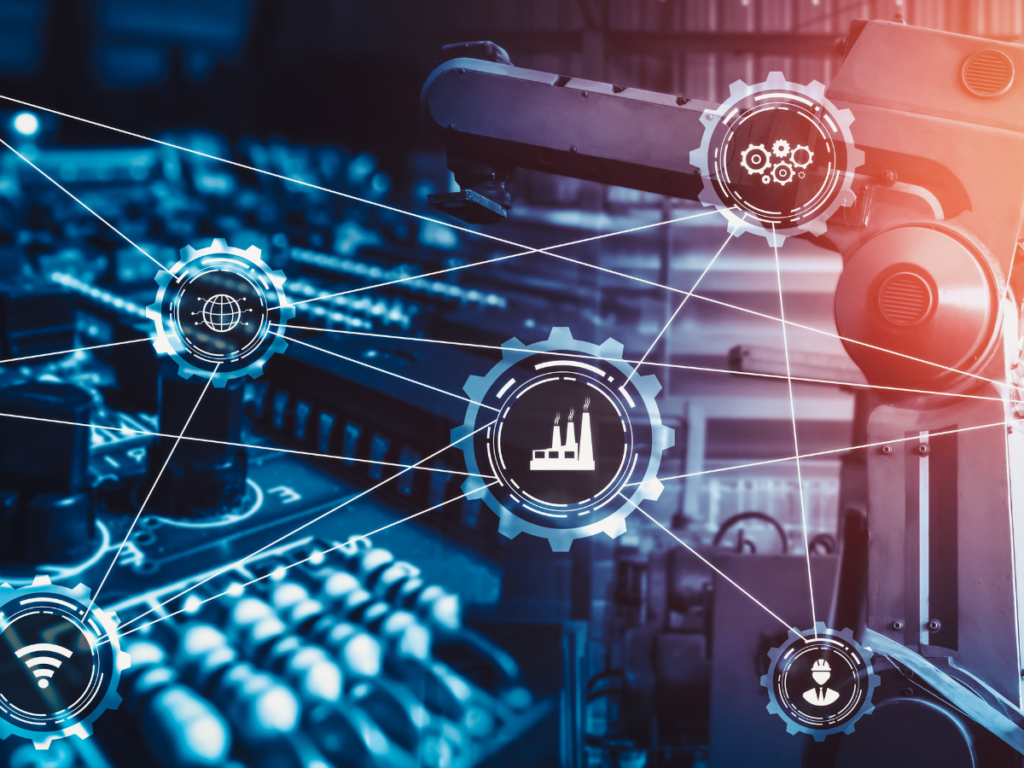
Industry 4.0, also known as the 4th Industrial Revolution, is changing the way companies manufacture product, operate and maintain machinery in an effort to optimize energy use, safety and productivity. The technology-driven movement involves the integration of Industrial Internet of Things (IIoT)-enabled equipment, such as smart sensors, automation, machine vision and connected controls, into production lines, processes and facilities.
Utilizing smart devices and advanced sensors to collect data, which is then analyzed by software, allows for real-time visualization into operations and more informed decision making regarding how the process or production line is operated, managed and controlled, and the way in which equipment is maintained. The intentional use of smart technologies and data analytics supports higher levels of efficiency in manufacturing, while also promoting uptime and throughput by utilizing informed and proactive process and maintenance strategies. At a time when industry is under extreme pressure to reduce costs and increase throughput and productivity, engaging in Industry 4.0 practices can provide the solution, enabling manufacturers to remain cost effective and competitive.
The Benefits of Industry 4.0
The connectivity and visibility of production, process and equipment data offers several benefits for manufacturers looking for a competitive edge, including:
- Operational Effectiveness: Leveraging and studying analyzed data collected from smart sensors, machine vision systems and connected automation equipment can help plant operators discover bottlenecks or other areas of inefficiency and take corrective actions. In addition, connected sensors can send alerts regarding events, process or production upsets or when critical measurements such as temperature or pressure are out of specification so that operators can use controls to quickly, in real time, return the process to its optimum running conditions, increasing throughput and reducing waste by eliminating the production of out-of-spec product. The use of connected sensors, machine vision, automation and controls, increases visibility and allows faster more informed decisions to be made. While the ability to closely monitor and control equipment leads to increased operational efficiency, uptime, throughput and product quality.
- Proactive Maintenance: While the manufacturing industry has long been guilty of running to failure, IIoT-enabled technologies such as smart sensors, machine vision, automation and controls enhanced with self-diagnostics support the transition from reactive maintenance to proactive maintenance. Smart connected equipment can also send alerts to operators and/or maintenance techs when equipment or components may require unscheduled maintenance soon, limiting potential damage to the equipment. This visibility into machines also allows maintenance teams to order parts and schedule repairs at a convenient time that is well ahead of failure. While the big savings here are obvious – the reduction of unplanned downtime and the loss of throughput and capacity during the repair, there are also smaller savings. For instance, thanks to connected devices and the data they supply, trips to the field to take readings and perform routine inspections may be reduced, saving labor hours and freeing up maintenance techs to tackle value-added repairs. In addition, self diagnostics and trending of data collected from machinery will likely reduce time spent troubleshooting faulty equipment. Further, facilities that traditionally practiced preventive maintenance, which is done according to a schedule versus on an as needed basis, may be able to reduce costs associated with unnecessary maintenance. Often, when repairs are done proactively, according to actual machine data rather than a set schedule, plant operators find that some of the routine maintenance can be postponed, slashing costs related to labor hours, parts and unnecessary downtime.
- Optimized Energy Use: By connecting smart sensors and intelligent control panel components and analyzing that data, it is also possible to monitor the consumption of electricity, steam and compressed air. By tracking usage via collected data, plant operators can determine where there is wasted energy and make data-driven changes to reduce unnecessary usage. In addition, monitoring can point out any blips or events with these services so they can be addressed to ensure stable and reliable power delivery, preventing inefficiencies, waste and potential power surges that could damage equipment or create hazards.
- Enhanced Product Quality: Not only can smart sensors and tighter control be used to quickly halt production processes that have gone astray to keep products within quality specifications, but smart machine vision systems can be used to inspect product and packages with more speed and accuracy than manually performing inspections, preventing damaged, defective or faulty products and packages from reaching consumers. By enhancing product quality, engaging Industry 4.0 technologies prevents wasted product and protects the manufacturer’s reputation.
New Industry 4.0 Equipment
Realizing the benefits of Industry 4.0 connectivity and the operational enhancements it achieves requires the use of modern IIoT-enabled equipment. Some key technologies include:
Smart Sensors | Smart, connected sensors are available to measure everything from equipment vibration to process temperatures and pressures to electricity usage. Because they are used to collect and transmit data to analytic software, they are essential to Industry 4.0. Modern automated equipment often includes smart sensors and data analytics software, but older equipment can usually be retrofitted with smart wireless sensors. Access to provided data can provide insight into production equipment, the process, and the surrounding environment. |
Modern Control Panels | With the introduction of Industry 4.0 technologies, control panels will be where new, smarter automation components are located. Modern control panels offer components such as Human Machine Interfaces that help operators better and more easily control the equipment or process and intelligent self diagnostics, smart lights and other components that will alert operators that changes may need to be made to the production line, equipment or power supply. |
Machine and Computer Vision Systems | These smart systems, which often include embedded analytics software, can be used in Industry 4.0 scenarios to detect issues with product quality so that production lines can be halted and managed if things are out of spec. In addition, real-time data collected from vision systems can be used to detect when machines and equipment are running out of spec or if there are bottlenecks on the line so that they can be addressed. |
Intelligent Automation, Robots, and Cobots | Modern automation equipment is often equipped with sensors, machine vision systems and controls that help boost operational efficiency, while also collecting data about product quality and/or asset health, helping to ensure throughput, enhance quality control efforts and prevent equipment failure. |
Together these and other IIoT-enabled technologies along with data analytics software help to connect the components of a manufacturing facility in a way that brings real-time insight into equipment and facility operations so that informed decisions can be made to help enhance production efficiency, productivity and uptime, while also improving energy efficiency and product quality. Manufacturers who embrace the technological changes of Industry 4.0 will find themselves in a better position as industry continues to operate on tighter budgets and with greater levels of competitiveness. Reputable partners like JHFOSTER can guide you through this Industrial Revolution and toward optimized operations.