Improve Efficiency with a Variable Speed Compressor
As manufacturers grapple with maximizing productivity while also cutting costs, increasing energy efficiency to reduce the electric bill is a growing trend. For industrial applications that have a fluctuating demand for compressed air, upgrading to a variable speed air compressor may be an effective way to improve air compressor efficiency and reduce the facility’s power consumption. This blog will explain the technology behind the energy-efficient design of variable speed compressors, as well as when it makes sense to upgrade.
What is a Variable Speed Air Compressor?
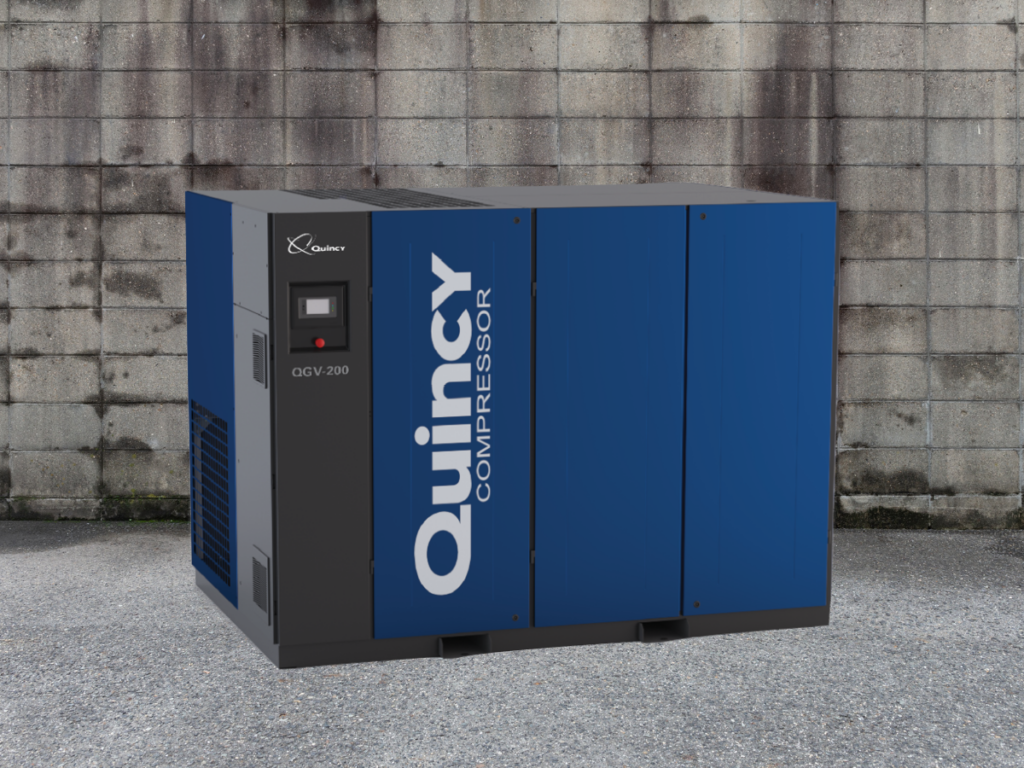
Variable speed compressors continuously adjust the motor speed to match the demand for compressed air. This means when the air requirement is low, the motor will run at a reduced speed and draw less energy for operation, and when compressed air demand is high, the compressor will automatically increase the speed of the motor to meet the air output needs, increasing compressor efficiency.
For comparison, most fixed speed compressors adjust the air inlet valve to meet air demand rather than adapting the motor speed to match the required output. This means that even when compressed air demand is low, the motor will still operate at the same speed. While this enables a compressor to continuously achieve the highest CFM for which it is rated, it may be wasting energy if peak demand is not needed, reducing the efficiency of a compressor.
The Advantages of Variable Speed Compressors
Due to the variable speed drive operation, industrial applications with compressed air needs that vary over the course of a day, shift or season are likely to benefit from upgrading to a variable speed air compressor.
As a matter of fact, there are multiple advantages associated with variable speed compressor technology, including:
- Reduced energy consumption: The greatest advantage of switching to a variable speed compressor in industrial applications where demand varies is that this type of compressor consumes less energy when operating below peak capacity demand. Some estimates suggest that the provided compressor efficiency may reduce energy costs associated with compressed air by 30 to 70%, depending on the amount of variability.
- Soft start/stop functionality: Because motors controlled by variable speed drives feature lower starting currents, the large spikes in demand that occur when fixed-speed motors start are eliminated. Rather, the soft start/stop offered by variable speed compressors automatically controls acceleration and deceleration, reducing amperage peaks and the associated stress on the electrical components of the unit.
- Reduced downtime: The soft start/stop feature and optimized performance of variable speed drives puts less stress on the electrical and mechanical components, so they experience less wear and tear, minimizing maintenance, reducing downtime and ultimately extending the life of the compressor.
- Constant pressure: Variable speed compressors provide constant pressure (as programmed) so when an industrial application demands air pressure at an exact volume and rate, the unit delivers it without delay.
- Optimized performance: These efficient compressors feature more advanced controls so they operate on tighter tolerances than fixed speed compressors. This enables variable speed air compressors to run at lower delivery pressures while still maintaining the minimum working pressure, optimizing performance and air compressor efficiency.
When Variable Speed Compressors Make Sense
Despite the advantages and enhanced compressor efficiency, upgrading to a variable speed compressor isn’t always the right move.
Variable speed air compressors make the most sense in industrial applications with a fluctuating demand for treated air. This is because the technology automatically adapts the motor speed to match air demand, so it will boost air compressor efficiency and significantly cut electricity costs in these operating environments. So, manufacturers that rely on multiple shifts with different air demands, facilities where demand fluctuates over the course of a shift or those with seasonal variability will typically see the biggest impact in the efficiency of a compressor when upgrading from a fixed speed unit to a variable speed compressor.
However, fixed speed compressor technologies are more efficient in industrial applications when base loaded or where variations in air demand are minimal so the compressor must always operate at or near its maximum output flow. For example, facilities with automated equipment and robots that operate 24/7 with a little to no variation in demand are likely to find fixed speed units offer better air compressor efficiency. Additionally, facilities with inconsistent power supply or extremely dirty or wet conditions are not good candidates for variable speed air compressors as the electronic components are sensitive to power fluctuations, dirt and moisture.
Need help deciding whether a fixed speed or variable speed air compressor will provide the best compressor efficiency and minimize the cost of electricity in your industrial application? The compressed air experts at JHFOSTER, a Tavoron company, can help you make an informed decision. Contact us today!