Detecting and Minimizing Air Pressure Drop in Compressed Air Systems
Air pressure drop is a common – and costly – problem with many compressed air systems. Not only will drops in pressure create problems with the functionality of the pneumatic tools and equipment the compressed air system serves, but pressure drop in pipelines can also run up the facility’s electric bill. So, detecting and minimizing excessive air pressure drops should be a priority as it will improve the performance of connected equipment and can save thousands in energy costs each year. Here, we provide practical advice on identifying pressure drop issues and implementing effective solutions.
What is Pressure Drop?
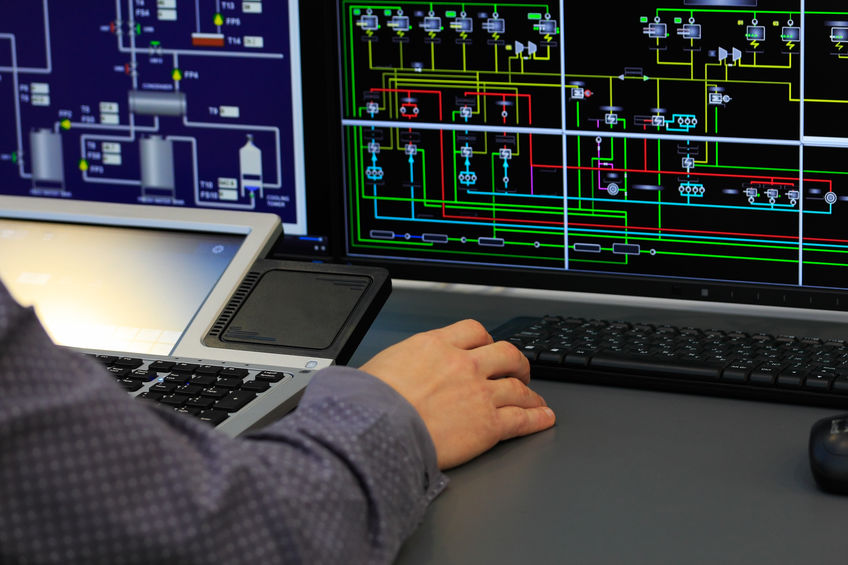
Pressure drop in a compressed air system occurs when there is a reduction of air pressure at any point between the compressor discharge and the delivery point. Air pressure drop may occur due to air flow obstructions, friction or resistance in the delivery system or air leaks within the compressed air system.
While some air pressure loss is typical of any system, a well-designed and efficient compressed air system should have no more than 10% pressure drop between the compressor discharge and the point of use.
Any drop in pressure above the acceptable 10% is problematic. If you are losing too much pressure, pneumatic tools and equipment will not receive enough air to operate effectively and efficiently. To compensate for this loss in performance, it may become necessary to increase the overall pressure of the compressed air system. However, over-pressurizing the system will cause it to work harder, significantly increasing the energy consumption of the air compressor, which will result in steep electric bills.
The Pressure Drop Equation
If you notice that pneumatic tools and equipment are underperforming or that the electric bill is suddenly rising, it’s a good idea to measure for any drops in pressure, so that the cause can be identified and mitigated.
Measurements should be taken in several areas of the compressed air system including:
- At the compressed air discharge or receiver tank,
- Before and after the air dryer,
- Before inline filters and ancillary equipment, such as after coolers,
- At various points in the distribution system, such as joints and connections.
Doing so will help identify the areas that have the most significant drops in pressure and will indicate where adjustments are likely needed.
5 Common Causes for Air Pressure Drops and How to Fix Them
Once you’ve determined the extent of the pressure drop and where the problem might be within the system, the next step is to identify the cause so that it may be remedied.
Five common causes for air pressure drops and their remedies include:
Undersized piping | When piping is too small for the required airflow of the system, pressure drop in pipelines will occur due to friction as the air tries to pass through the undersized piping, creating drag that results in pressure drop. Undersized piping should be replaced with piping that is suitably sized for the required CFM of the system. This will reduce pressure drops and ensure optimal efficiency of the system. |
Complex distribution system | If the air distribution system is complex and contains many twists and turns or long runs of piping, the air will encounter friction as it flows, resulting in pressure drop in pipelines that will adversely affect the performance of the system. If possible, the distribution system should be redesigned to be more efficient. This means ensuring that the pipes are properly sized for the required CFM of the system. The number of tees and elbows should also be reduced and sharp turns should be eliminated. While this is a significant undertaking, an well-designed system will save money on energy bills. |
Leaks in the distribution system | Any loss of air will result in air pressure drops, creating a situation in which the compressor must work harder to generate enough pressure to effectively serve the equipment. Leaks are common in couplings, hoses, fittings and joints and are one of the most common causes of pressure drop. Finding and fixing any leaks will reduce pressure drop and increase the overall performance and efficiency of the system. |
Clogged filters | Filters that are clogged with contaminants, dirt, oil, water or moisture obstruct the flow of air and will result in drops in pressure that reduce the effectiveness of connected tools and equipment and force the compressor to work harder, increasing the energy consumption of the system. Regular filter replacement is a simple solution to this problem and will maximize the efficiency of the system while also preventing wear and tear on the compressor and excessive energy consumption. |
Moisture and/or corrosion | If there is moisture in the system, there is likely corrosion. Flaking corrosion will attach to the interior of the pipes causing friction and/or obstructions that make it difficult for the air to flow, which will result in pressure drop through the pipes. Corroded pipes should be replaced to avoid damaging the system. The addition of an air dryer (or upgrading the current unit) will prevent the moisture build up that is responsible for corrosion, while also improving the quality of the generated air from the system. |
If you need assistance in measuring, identifying or implementing solutions for pressure drop, please contact JHFOSTER, a Tavoron company. As experts in compressed air systems, our representatives are available to help detect and solve air pressure drop problems so your tools and equipment operate effectively and energy costs can be reduced.