Designing the Ideal Environment for Your Air Compressor Room
While selecting the right industrial air compressor is critical for efficient and effective performance, it is only part of the equation. The compressor room environment, air compressor system design and compressor installation also play a crucial role in the operation of the compressed air system. Important considerations for air compressor room design, system design and air compressor installation will be provided in this blog.
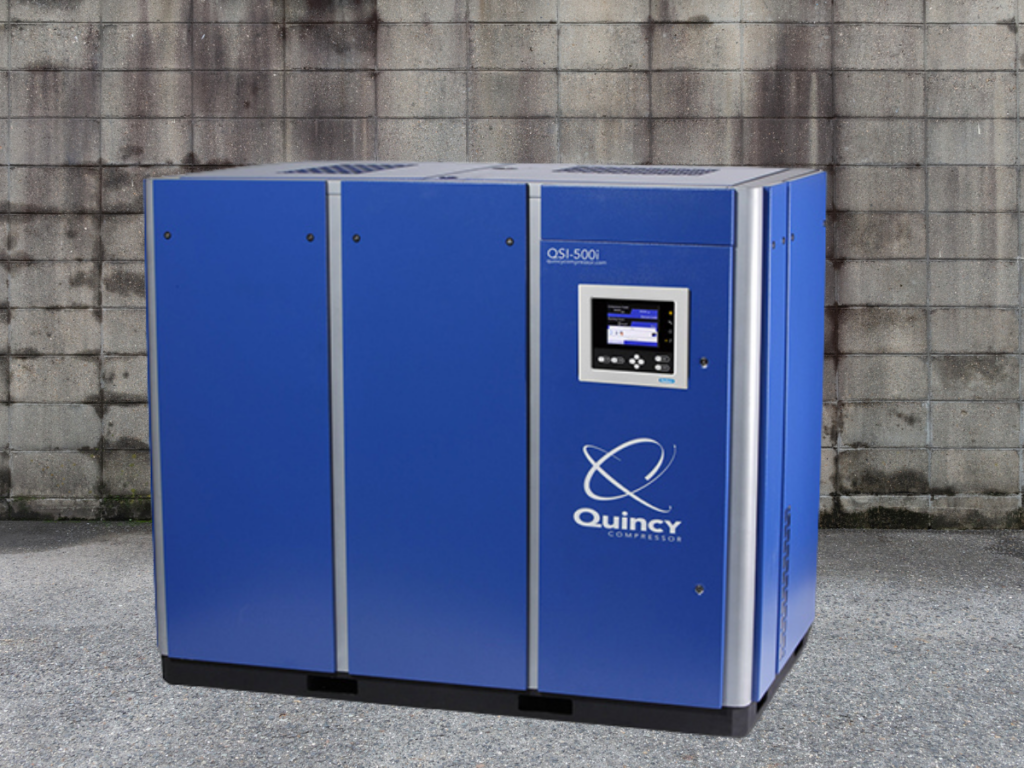
Why Compressor Room Design is Important
The site and layout of the compressor room has a significant influence on the overall performance, efficiency, reliability and operating cost of the entire compressed air system.
This is because the placement of an industrial air compressor can greatly impact its ability to provide enough air to end points, as well as its energy consumption, lifespan and operational and maintenance costs.
For example, if the compressor is placed at too great a distance from the point of use, it may create pressure drops that will force the system to work harder to provide air to the point of use, resulting in higher levels of energy consumption and wear and tear on the unit and its components. Or, if the temperature in the area is too hot or humid for the compressor, it can degrade the compressor and related equipment over time, increasing maintenance needs and reducing air quality over time.
For this reason, it is essential to create an air compressor room environment that will encourage the best air flow, promote efficient use of energy and reduce avoidable maintenance issues for optimal system performance.
5 Considerations for Compressor Room Design
When planning the location and layout of the air compressor room, these five considerations will go a long way to ensuring prime performance of the system:
Placing an industrial air compressor as close as possible to the equipment it services will optimize performance. If the air must travel long distances to the point of use, pressure drops will reduce airflow to the equipment and negatively impact performance of the machinery and tools. In addition, pressure drops result in higher energy bills and wear and tear on the compressor, which will require maintenance and ultimately reduce the service life of the unit.
Additionally, the foundation for the air compressor should be level and stable enough to support the weight. A surface that is not level will lead to vibration and wear and tear, which will reduce the unit’s lifespan. Proximity to the power supply and availability of a floor drain (that meets environmental regulations) to manage system condensation are also important elements of a suitable location.
The air compressor room environment should maintain proper temperature and humidity levels. The optimal temperature for the compressor room is generally agreed to be between 50 and 85°F.
If air compressor installation is in a room with higher temperatures, the compressor may be forced to work harder and will likely experience mechanical issues, resulting in more frequent maintenance. If compressor installation is in an area where temperatures are likely to climb above the manufacturer suggested range, fans and ventilation may be used to cool the area and oil selection should be geared toward the environment.
Conversely, if the temperature dips too low – which is a likely scenario in an outdoor air compressor installations – it can result in wear and damage due to thickening oil and/or condensate freezing inside the compressor or air delivery pipes. If an industrial air compressor must be placed in a location where temperatures may fall below 40°F, heat tracing around the pipes and an internal heater for the unit are smart investments.
The humidity level in the compressor room also plays a role in its performance. Drier air does not hold as much moisture, so it is easier for the compressed air treatment system to eliminate damage-causing moisture, reducing maintenance costs while maintaining compressed air quality requirements. The use of air coolers and/or air dryers is always suggested as a way to ensure that moisture from hot, humid air is removed from the system.
Industrial air compressors produce a lot of excess heat during operation, so providing enough air circulation and ventilation is also very important as this will help reduce escalating temperatures in the air compressor room, ensuring that the unit does not experience heat related issues or shutdowns due to overheating. Exhaust air can be ducted outside during summer months to reduce compressor room temperatures and help ensure that the intake air is cooler and easier to treat. Exhaust air can sometimes be ducted into the building to assist heating during winter months.
Dirt and dust can be drawn in with the ambient intake air and cause system maintenance issues, while also reducing the quality of produced air. Installation of air compressors should ideally be in a location with access to clean air to reduce the amount of contaminants drawn into the system. In addition, intake air should be filtered to ensure that contaminants are removed before they can enter the system.
There should be enough space available in the compressor room so that there airflow around the compressor and access for inspection and service.
Air Compressor System Design
Once a location that ticks the above-mentioned criteria is chosen, air compressor system design is the next step in creating an effective air compression system.
Below are some tips on air compressor system design, along with links to more detailed information on each topic:
- Properly size the air compressor: Make sure that the industrial air compressor is properly rated for the CFM, PSI, and duty cycle required for the application. More detailed information can be found here.
- Choose the right piping material: While there are many options available and all have pros and cons, the material selected should meet the airflow and pressure requirements of the system, as well as the environmental conditions of the facility. More details on available piping types can be found here.
- Properly size the piping: Piping is available in a variety of different diameters so be sure that the diameter can safely manage the system airflow, volume and pressure. Piping that is too narrow will restrict airflow, increasing energy usage and reducing the performance of the end-use tools and equipment. Detailed information can be found here.
- Use short and straight lengths of pipe: Layouts with too many bends and sharp directional changes will create turbulence and pressure drops within the system, forcing the compressor to work harder to supply air, increasing energy bills and hurting the performance of attached equipment. Try to design a system that uses straight and short lengths of pipe. Tips for designing the air delivery system are available here.
- Reduce moisture: Moisture concentration is a product of both the ambient intake air and the act of compressing the air. Air dryers and coolers help reduce the amount of moisture present in the system. Drains and condensate lines should be provided to release accumulated moisture and prevent rust and corrosion. Information on removing water from the compressed air system is available here.
Air Compressor Installation Tips
Once the compressor room location is chosen and the system has been properly designed, air compressor installation is the next step. Proper installation of air compressors will provide optimal performance, long service life and safe operation, so ensure that installation is done correctly by:
Ensuring that the foundation is level, stable and able to support the weight of the industrial air compressor.
Selecting the best location for placement of the air compressor unit.
Making sure the electrical supply meets the power requirements of the unit.
A more thorough installation checklist can be found here.
Selecting a suitable environment for the compressor room, creating an efficient air compressor system design and ensuring safe and proper air compressor installation will provide an air compression system that performs well and offers high levels of efficiency and safety. For assistance with sizing and selecting an industrial air compressor, designing a compressor room or air compression system or installation of an air compressor, please reach out to the compressed air experts at JHFOSTER, a Tavoron company.