Choosing the Right Actuator Type for Your Application
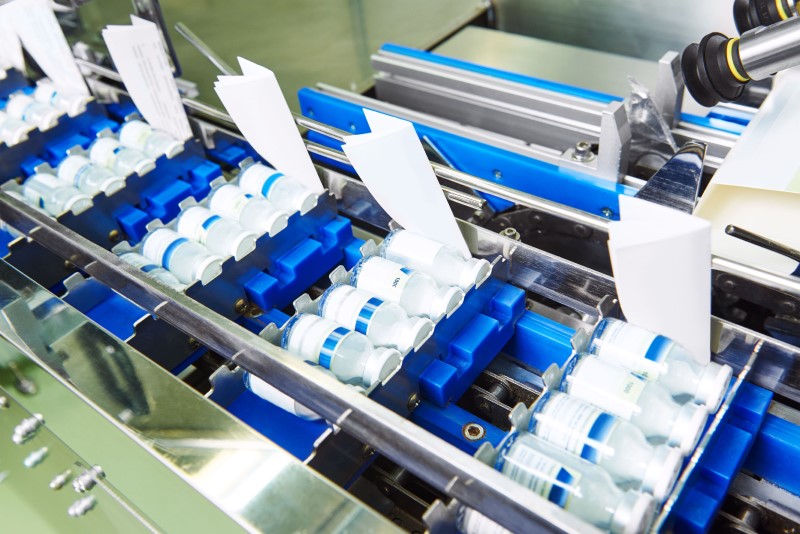
Sometimes the choice between the three main actuator types – electric, pneumatic and hydraulic – is a no brainer. For example, if you need heavy-duty motion, a hydraulic actuator would be the obvious choice, a potentially explosive environment necessitates the use of a pneumatic actuator and a sterile operation would demand an electric actuator. But beyond these and other obvious situations, choosing the best type of actuator for a motion control application can be tricky.
And, while any type of actuator must provide precise positioning, start and stop without delay and perform reliably in the application, considerations beyond these basic requirements must be examined during the selection process. So, this blog will discuss the operating principles, the pros and cons of electric, pneumatic and hydraulic actuators and key specifications to help make your selection process easier.
What is an Actuator?
Before getting into the selection process and the specifics of each actuator type, it’s important to understand the function of actuators in motion control applications. As mechanical components that convert energy into lifting, ejecting, pressing, clamping and other motions, actuators are found in almost every machine and device that features moving parts and are used in industrial applications to activate equipment such as pumps and valves.
Actuators are categorized by both the type of motion they produce and the form of energy used to create that motion. Linear actuators provide straight-line motion and rotary actuators provide circular motion. Further, hydraulic actuators depend on hydraulic fluid to create and control motion; pneumatic actuators use pressurized air to activate and manage motion; and electric actuators generate motion via electricity.
Electric Actuators: Advantages and Disadvantages
Electric actuators receive electrical currents that energize an electric motor, which in turn generates a force that moves the desired component. Electric actuators usually include feedback devices and self diagnostics, which make them more complex, but also very precise, repeatable and reliable. Because they offer clean, electronic control, electric actuators provide many performance advantages in applications such as electronic and medical devices and clean room or sanitary applications.
Electric Actuator Advantages:
- Precision control and performance
- Very accurate positioning and velocity control
- Excellent response times
- High speeds
- Environmentally and clean-room friendly as they do not require the use of hydraulic fluids or compressed air
- Reduced operating costs as they are very energy efficient and do not require fluids or compressed air to operate
- Small in size
Disadvantages of Electric Actuators
- Not as much strength and power as other actuator types
- Complex designs
- Higher upfront costs
Pneumatic Actuators: Advantages and Disadvantages
Pneumatic actuators use compressed air as the energy source and convert it into mechanical energy to create force in motion control applications. They are known for high speeds and are ideal in applications such as air-operated tools and industrial equipment. They are a convenient choice in industrial settings as most are already equipped with an air compressor and are safe to use in locations where fire or explosion hazards exist.
Disadvantages of Pneumatic Actuators
- Can be inefficient due to pressure losses associated with the use of compressed air
- May be slower to respond if air pressure is inadequate
- Air can become contaminated with oils or moisture found in the pneumatic system
- Can be costly to operate if the compressed air system is not optimized and efficient
Advantages of Pneumatic Actuators
- Accurate and repeatable motion profile
- Can be safely used in explosive environments
- Minimal maintenance and reliable operation
- Low upfront cost
- Simplicity of design
- Easy installation
Hydraulic Actuators: Advantages and Disadvantages
Hydraulic actuators rely on hydraulic fluid that is supplied by a pump to create and control movement. Adding pressure to the fluid will generate force while reducing pressure will lessen the force. Hydraulic actuators can provide significant force and are a self-contained system, making them a favorite in heavy-duty applications such as construction and agricultural vehicles and equipment.
Disadvantages of Hydraulic Actuators
- Leakage of hydraulic fluids may pose an environmental hazard and prevent use in applications where contamination of product is prohibited
- Slower speeds
- Not as precise, accurate or repeatable as other actuator types
- Can become inefficient and inaccurate if there are fluid leaks
- Higher upfront costs due to companion components such as pumps and fluid reservoirs
- Higher lifecycle costs for fluid replacement and maintenance
- Not safe for use in applications where fire is a potential hazard as hydraulic fluid is flammable
Advantages of Hydraulic Actuators
- Provide extreme force, strength and power
- Easy to control
- Dependable and reliable operation
- Long service life
- Self-contained and portable as they do not require a pneumatic system or electrical input to operate
Other Selection Criteria
All actuator types exhibit both advantages and disadvantages and often these strengths and weaknesses will dictate whether an electric, pneumatic or hydraulic actuator is the best choice based on the application needs and/or the working environment. In all cases, it is important to consider the requirements of the application to ensure that the selected device will adequately fulfill the needs of the motion control profile, so consider the following during the selection process:
- What type of motion is needed, linear or circular?
- How much force is required?
- What stroke length is needed?
- Positioning accuracy and repeatability needed?
- How fast does it need to move and respond?
- What is the duty cycle (how often the actuator will operate)?
- What is the device footprint?
- Are there special considerations such as use in outdoor environments, potential for fire or explosion or contamination concerns?
Once you have a clear understanding of the needs of the application, it is easier to choose the right actuator for the job. Reputable suppliers like JHFOSTER can provide additional assistance during the selection process to ensure that you purchase an actuator that is well suited to the application and of the highest quality for the most reliable, efficient and cost-effective operation.