3 Advantages and Disadvantages of Cobots
As more manufacturers embrace factory automation technologies, many are exploring the use of collaborative robots, or cobots, as they tend to be more budget friendly than traditional robots and are well suited to industrial applications such as material handling, assembly, inspection and packaging. However, before implementing a collaborative robot, it’s important to understand the differences between a cobot and an industrial robot and to examine both the advantages and disadvantages of this popular automation technology.
How Does a Cobot Differ from a Robot?
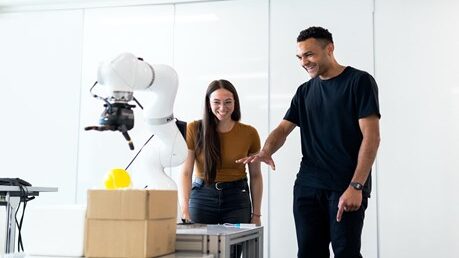
Collaborative robots are a modern generation of industrial robots that are designed to work safely in close collaboration with human workers in industrial settings. The main difference between cobots and traditional robots is that collaborative robots are equipped with advanced navigation, safety sensors and software algorithms that allow them to automatically stop upon collision with humans or obstacles and exert minimal forces if there is an impact.
This means that unlike traditional robotic automation, cobots can safely operate around and collaborate with people without the need for safety barriers or isolated work cells.
As with traditional robots, the goal with collaborative robots is not to replace human operators, but rather to boost the throughput of industrial processes by efficiently automating repetitive tasks while allowing human workers to focus on operations that require more advanced cognitive thought and/or greater dexterity.
Finally, collaborative robots tend to be more adaptable and easier to reprogram than traditional robotic automation technologies, giving them more flexibility around the facility than standard industrial robots, which are typically employed for one purpose over their lifetime in the factory.
Because cobots offer capabilities that can be used in almost every manufacturing setting, additional investments for safety barriers isn’t required in many applications. They are also flexible enough to be introduced to different areas within the same organization and are often lower in price than traditional robots, manufacturers often select cobots over traditional robots, especially when they are just beginning to adopt automation. While this is a good strategy, it’s crucial to consider the benefits, as well as the shortcomings, associated with collaborative robots before committing to a cobot. Below we highlight the top three advantages and disadvantages of these manufacturing marvels.
Top 3 Advantages of Collaborative Robots |
Cobots are Cost Efficient: Collaborative robots tend to be less expensive than traditional robots at the time of purchase because they are smaller in size and less complex. In addition to the initial savings, over their lifetime cobots provide further cost advantages. For example, they usually do not require a separate work cell or safety guarding to keep human operators safe as is required when using traditional robotic automation. This saves capital on the cost of infrastructure materials, design and labor and does not require as much space in the plant. Additionally, because cobots are easy to program, an automation expert’s assistance is not usually needed and manual laborers who collaborate with the cobots do not need |
Cobots are Safer: Thanks to their safety features, collaborative robots can slow down or stop when sensing the approach of a human or physical barrier in its path, helping to avoid crashes and collisions. Further, built-in force limiters mean that if a collision does occur, the impact will not be enough to injure a human operator. |
Cobots are Flexible and Adaptable: Because collaborative robots are smaller, they tend to be somewhat portable, making them easier to relocate to different areas around the facility. And because collaborative robots can be programmed via hand guiding, the use of an automation expert is not needed to teach the robot a new movement or task. These characteristics allow collaborative robots to be used in various processes around the facility if product or process changes occur in the future. |
3 Disadvantages of Collaborative Robots |
Cobots are unable to handle Heavy Loads: Collaborative robots are typically only suitable for handling loads of 3 to 25 kg, while most traditional robots can easily manage payloads of up to 2 tons. This limits the use of cobots in heavy-duty applications. |
Cobots Offer Limited Speeds: Because collaborative robots are designed to work in close proximity to human operators, they cannot provide the high speeds associated with traditional industrial robots. A typical cobot speed is about 250 mm per second, significantly less than that of standard robotic automation. This speed may be further reduced if additional safety measures are used to ensure speed reductions when humans are nearby. While these features improve the safety of cobots, the reduced speeds prevent use in applications that require the highest speed and efficiency. |
Cobots are Not Independent: Although cobots can run 24/7, by design collaborative robots often require human assistance to complete a task. So, in situations where shift workers are not available around the clock to provide collaboration or supervision, cobots may not be able to work at full capacity and may have limited efficiency and throughput in the operation when compared to traditional robotic automation technologies. |
While collaborative robots offer several advantages and are a frequently a wise choice when looking to increase efficiency through automation, it’s important to fully consider the drawbacks before investing in a cobot. If speed, heavy loads and 24/7 operation are requirements of the application, traditional robotic technologies may be more suitable. A risk assessment also needs to be performed to assure all safety standards and requirements are met. A representative at JHFOSTER can help you select the appropriate technology for your factory automation needs.