Automated Inspections Maximize Food and Beverage Quality Assurance
Food safety and customer satisfaction both play a vital role in the highly competitive food and beverage industry, making product and packaging integrity crucial. The key to keeping consumers coming back for more is to ensure that food and beverage products are safe for consumption and securely protected within the packaging, which must be consistently free from damage and correctly labeled. In order to meet the stringent quality and regulatory standards necessary for success in the food and beverage industry while also supporting high levels of throughput, many participants in the market are automating packaging inspections to provide the highest levels of quality assurance at top speeds.
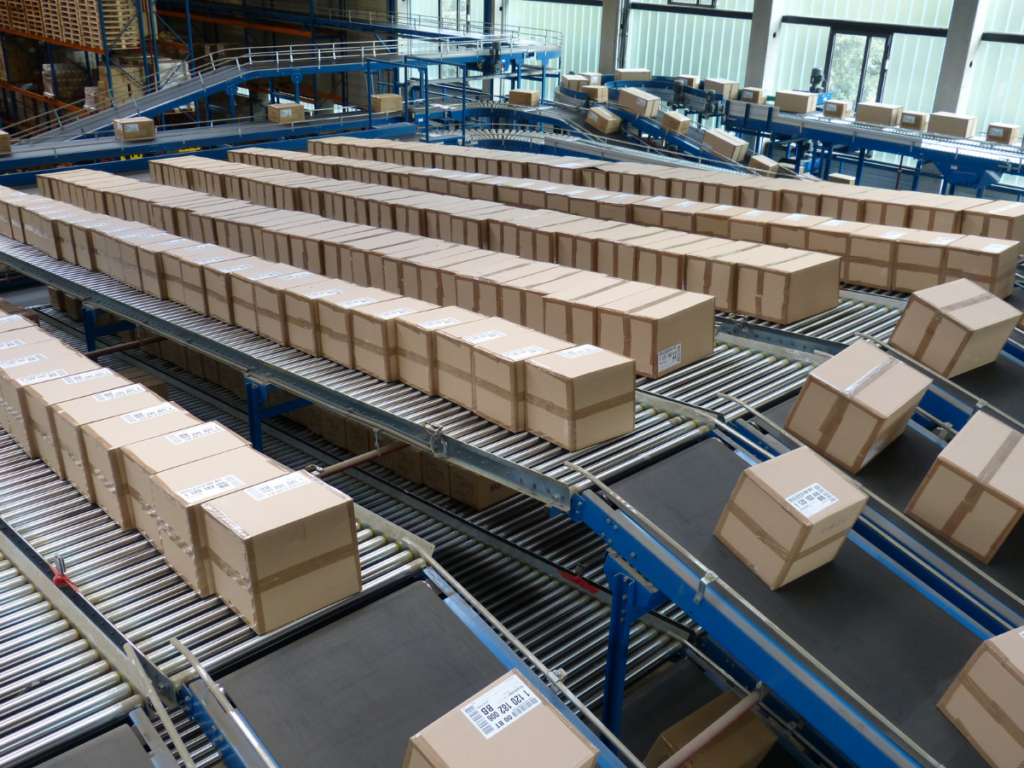
The Importance of Secure Packaging and Proper Labeling
Proper packaging and labeling are essential in the food and beverage industry as they help protect food products from contamination and provide essential information to consumers, helping to preserve safety and quality. Compromised packaging or improper labels can be disastrous for players in the food and beverage industry for a variety of reasons.
First, because the food and beverage industry provides products for human consumption, the U.S. Food and Drug Administration requires that these products are accurately labeled and packaged in a way that protects the contents from spoilage and contamination and provides essential information to consumers. Compliance with regulatory standards regarding packaging and labeling is a top priority because if packages and labels do not meet these requirements, there may be hefty fines and potential production shutdowns. Equally detrimental, compromised packages and mislabeled products can result in costly, reputation-damaging recalls.
In addition, packages that are flawed or mislabeled present issues for retailers, so products or packages that are damaged or improperly labeled or barcoded are likely to be rejected, which results in costly rework for the food manufacturer or packager, chargeback penalties and/or potential loss of contract imposed by the retailer.
Finally, when consumers see open or torn packages, damaged contents or incorrect label information, it can have a negative impact on the product or brand, resulting in dissatisfied customers who are likely to opt for competing products in the future rather than staying brand loyal.
Automated Systems for Food and Beverage Quality Assurance
To reduce the chances of sending damaged or incorrectly labeled food and beverage products out into the world, quality assurance must be a top priority for participants in this competitive market. In the past, food and beverage manufacturers and packagers relied on manual quality assurance checks; however, manually performing inspections is time consuming, which negatively impacts throughput. In addition, human errors often result in oversights such as mislabeled products or damaged packages passing unnoticed during quality assurance checks.
For this reason, automated packaging verification and inspection systems are a more reliable, accurate and efficient option for food and beverage manufacturers who must not only uphold the highest quality standards, but also significant levels of throughput. Many of today’s advanced automated inspection systems, such as the Control Reliable Inspection System, or CRIS, from Sensors Integration, are designed to optimize the speed, consistency and accuracy of the inspection process, increasing reliability and drastically improving quality assurance efforts.
The CRIS product and package verification system is designed to handle the demands of inspecting by reading the barcode and verifying that the correct product is in the correct package. It relies on a patented fail-to-safe inspection technique that ensures all mispackaged products are rejected from the production line by assuming that all items should be rejected until positively verified as a match.
For round products, the CRIS 360 product and package verification system offers multiple cameras to provide 360-degree product validation so that packages in any orientation can be correctly identified by barcode or pattern and then verified or rejected based on whether The system can also inspect round, touching, and randomly oriented products where other product verification systems cannot 100% inspect because of occlusions to the camera.
5 Benefits of Automated Inspection
Automating package and product verification and inspection with systems like CRIS provides a wealth of benefits for food and beverage manufacturers, but the five most compelling include:
- Reducing Recalls and Ensuring Compliance: Automated inspection helps to ensure that all packages and labels meet government regulations, provide protection for products and display accurate information for consumers. The high levels of accuracy afforded by advanced automated verification systems, such as CRIS, help to prevent regulatory fines and product recalls as the cameras and imagers guarantee that the product is in the correct packaging, eliminating the chances of regulatory action and recalls reducing potential expenses and loss of business.
- Ensuring Product Integrity: Advanced automated inspection systems are more likely to reject flawed packages, which are often responsible for food spoilage and contamination that occurs during transport, storage or on shelves. By using automated systems to consistently and accurately perform quality assurance checks, food and beverage manufacturers and packagers can rest assured that all packages are properly sealed and free from damage or defects that might promote contamination and spoilage. When they receive high-quality products safely sealed within packages that are intact and properly labeled, consumers are more likely to remain satisfied and brand loyal.
- Improving Quality Control: Consumers are likely to bypass or return for a refund products that have damaged packaging or contents. Using automated inspection and verification systems ensures reliable detection of defects and damage, which improves quality and minimizes opportunities for returns and refunds. By improving quality assurance through the use of automated inspection and verification, food and beverage manufacturers can reduce costs associated with returns and refunds, product and package waste and lost revenue due to unsatisfied customers.
- Minimizing Chargebacks: When retailers receive packages that are incorrectly labeled or barcoded, they are likely to return the shipment and charge fines to the manufacturer or packager. By using a more reliable and accurate automated quality assurance system, more defects and flaws will be flagged and removed from the production line before being shipped to retailers. This will help minimize chargebacks and the costs associated with penalties and rework, as well as the potential loss of business contracts.
- Maximizing Throughput and Accuracy: Automating product and package verification and inspection with a system such as CRIS allows food and beverage manufacturers to perform quality assurance inspections with more accuracy and at significantly higher speeds than when these activities are performed by human employees. This will help ensure high levels of product quality and will allow food and beverage manufacturers to boost throughput, getting products to consumers much faster.
To learn more about the ways in which the CRIS system from Sensors Integration can help food and beverage manufacturers and packagers prevent product recalls, retailer chargebacks and regulatory non-compliance penalties while boosting throughput, maximizing quality and product integrity and ensuring customer satisfaction, please contact Sensors Incorporated, a JHFOSTER company.