Air Compressor Maintenance Minimizes Rotary Screw Compressor Downtime
Air compressors are indispensable equipment in manufacturing facilities, so keeping them in good working order through a regular air compressor maintenance routine is essential to avoiding compressor – and production – downtime. Although rotary screw air compressors are very reliable, scheduling routine maintenance for this type of screw compressor will further ensure reliability for years to come.
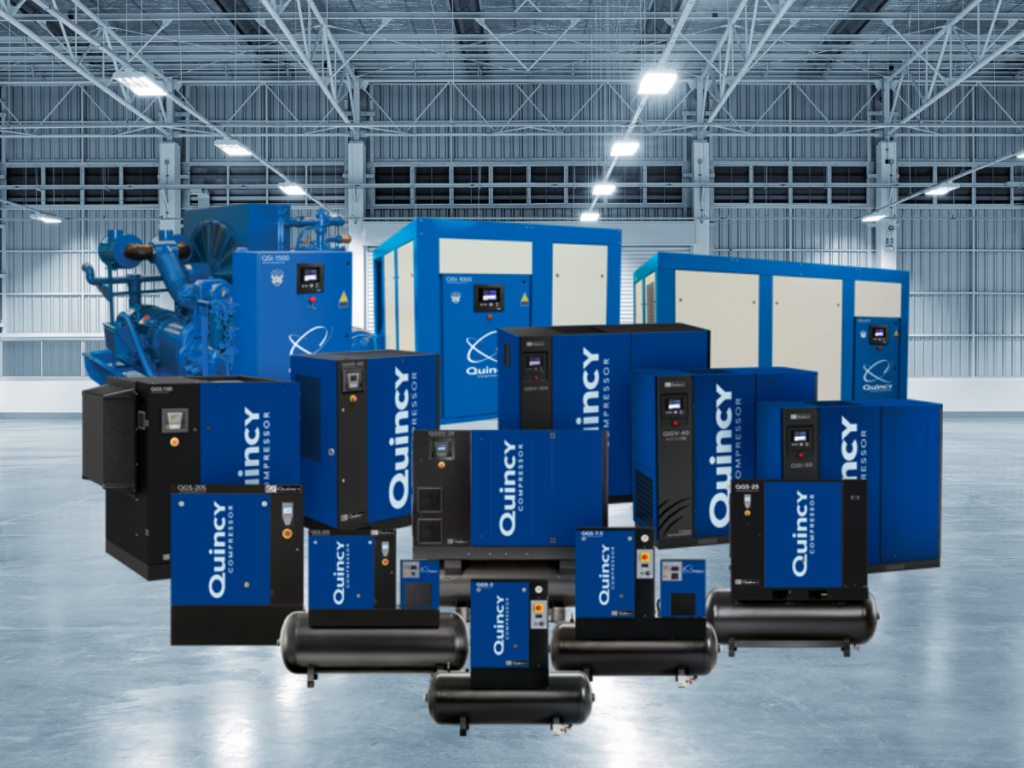
What are Rotary Screw Compressors?
A rotary screw air compressor is a type of positive displacement air compressor that uses rotary movements to compress air. Rotary screw compressors feature two interlocking rotors – one male and one female – which mesh closely without touching. Air enters the compression chamber through the inlet valve and is captured in the void between the rotors. As the rotors turn, they compress the trapped air.
Rotary screw air compressors offer continuous operation, or a 100% duty cycle, making them suitable for facilities that demand a constant supply of compressed air.
Advantages of rotary screw compressors include:
- Simple maintenance: Because of their design, wear and tear is kept to a minimum, so routine air compressor maintenance is relatively simple.
- High performance: The high airflow rates offered by rotary screw compressors allow them to power heavy-duty pneumatic tools and equipment, even in challenging conditions subjected to extreme temperatures.
- Compact footprint: By design, rotary screw compressors offer a compact footprint, making them suitable for facilities where space is at a premium.
- Low noise – Rotary screw compressors are typically enclosed for quiet operation.
The Importance of Air Compressor Maintenance
The goal of preventive air compressor maintenance is to identify and address problems before they result in prolonged periods of downtime. A solid routine of preventive maintenance will provide a return on investment in the form of reduced air compressor repair costs, energy savings, improved uptime and extended service life.
While rotary screw air compressors are reliable in design, practicing routine air compressor maintenance will provide several worthwhile benefits, including:
- Reduced downtime: Routine inspections and preventive maintenance activities catch and manage small issues before they become serious problems that require costly and time consuming air compressor repairs. This helps to minimize downtime of the compressor and the equipment that depends on it.
- Increased efficiency: By properly maintaining your rotary screw compressor, it will ensure that it operates as effectively and efficiently as possible, saving energy, reducing electric bills and ensuring optimal operation.
- Minimized air compressor repair costs: By identifying and addressing issues before they result in catastrophic failure, air compressor repair costs – including labor and replacement parts – will be reduced.
- Prolonged lifespan: When you stick to a routine of regular air compressor maintenance, it is possible to extend the unit’s life expectancy, ensuring a return on investment, preventing shutdowns, and reducing capital expenditures.
- Warranty validation: Many manufacturers require regular air compressor maintenance to keep the warranty valid.
Best Practices for Air Compressor Maintenance
Although rotary screw air compressors are built for reliability, they contain several components that require periodic attention to ensure long-term performance of the unit.
To reap the benefits of preventive air compressor maintenance for your rotary screw air compressor, be sure to incorporate the following activities into your maintenance schedule on a regular basis, as noted.
On a regularly scheduled basis, per manufacturer recommendations | On a daily basis |
Change the oil: Per your manufacturer’s recommended schedule, oil should be changed on a regular basis. If your compressor runs at high temperatures, you may need to change it more often. Oil samples should be taken every few months to ensure that it retains the right consistency and that it has not become contaminated. | Noise and vibration: Unusual or new noises and vibrations signal that something may be amiss and serve as early warning signs of compressor failure. If anything out of the ordinary is experienced, address it immediately. |
Change oil filters: These can become clogged and interfere with operation. It is typically recommended to change oil filters after 2,000 to 4,000 hours of operation. | Condensate traps and drains: Be sure these are functional. If traps and drains do not operate properly, moisture may build up, which can result in corrosion of air compression system components. |
Inspect air filters: Be sure to check that air filters aren’t clogged, as this will reduce the efficiency and performance of the air compression system. They should be changed or cleaned when a pressure drop is noted. | Check for leaks: To ensure energy efficiency of the unit and optimal performance of end-use equipment, check for and address any leaks in the air compression system, especially around connections. |
Check belts and couplers: Look for signs of wear and cracks and check belt tension on a monthly basis. Replace or adjust as needed. | Fluid levels: In oil-lubricated screw compressors, oil levels should be checked each day using the sight glass. Add oil if levels are too low to avoid damaging key internal components. |
Grease motor bearings: Greasing the motor bearings on a regular basis will help prevent motor failure. | |
Clean cooler and cooler pre-filters: The coolers should be inspected and cleaned on a regular basis, which should be determined by the dust load of the facility. If the cooler is equipped with pre-filters, these should be inspected, cleaned and replaced as needed. |
Performing these preventive maintenance activities on a regular basis will help ensure trouble-free operation of your rotary screw compressor, while also minimizing the costs of failure and downtime and increasing the performance and efficiency of the unit. For assistance creating a schedule of air compressor maintenance or to inquire about a air compressor maintenance program, please get in touch with the experts at JHFOSTER, a Tavoron company.