7 Ways Pressure Flow Controls Optimize Pneumatic Systems
While most facilities with properly sized air compressors should have an adequate supply of air to power their automated pneumatic systems, problems may arise during fluctuations in demand and times of peak usage when air demand exceeds capacity, causing unstable system pressure.
In response to fluctuations, the pneumatic system can overcompensate and boost system pressure in an attempt to meet demand. However, over-pressurization increases energy consumption and causes the compressor to cycle on and off, which can damage the equipment. In addition, unstable system pressure can result in subpar operation of pneumatic tools, equipment and automation.
Fortunately, pressure flow control valves and devices provide a simple solution to this challenge because they balance pressure and demand to better manage the distribution of compressed air.
This blog will serve as a guide that explains the concept of pressure flow controllers and why they are essential in providing precise air flow control across automated and other pneumatic systems.
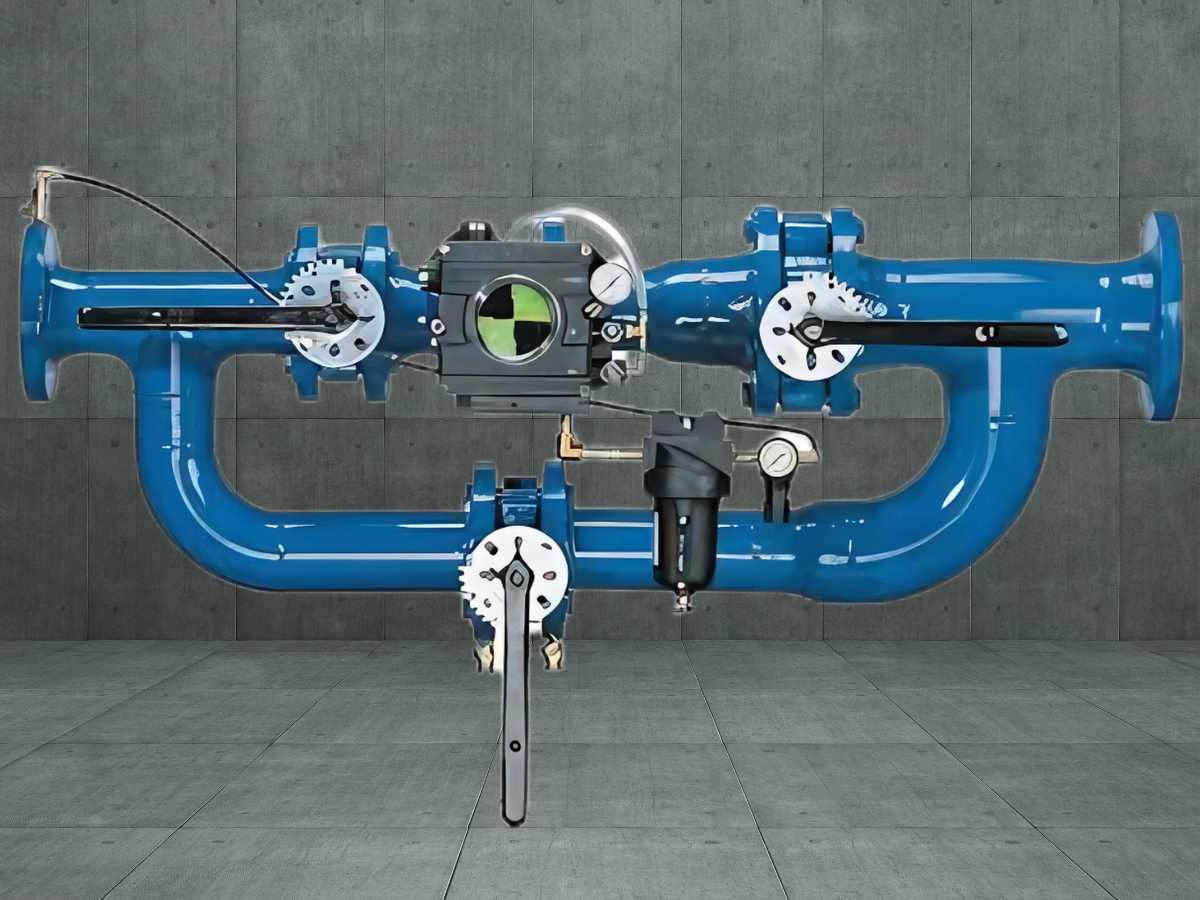
What is a Pressure Flow Controller?
In simple terms, a pressure flow controller is a pressure regulator that adapts to changes and fluctuations in air flow demand by releasing stored compressed air in a precise and controlled manner. The addition of a flow control valve to a pneumatic system helps to maintain stable system pressure, even during fluctuations in demand and times of peak usage.
There are two basic types of flow controllers:
Pilot-operated air flow control valves
Pilot-operated pressure flow controllers, such as a pneumatic flow control valve, feature a mechanical pilot valve that regulates pressure by sensing downstream pressure and adjusting the main valve so that it maintains pressure and flow at the specified set point. While pilot-operated pneumatic flow control valves are less precise than electronic flow control valves, they are suitable for use in applications with stable air demand. Pilot-operated flow control valves are also less complex and less expensive than their electronic counterparts.
Electronic flow controllers
These flow controllers employ sensors and electronic actuators that measure and adapt the flow in real time, providing fast and precise reactions to changing operating conditions. They are the go-to pressure flow control device for automated pneumatic systems and applications with strict pressure tolerances.
7 Ways Pressure Flow Controllers Optimize Pneumatic Systems
When applied as a safeguard between the supply side and the demand side of compressed air systems, pilot-operated air flow control valves or electronic flow controllers along with properly sized supply side storage prevent over-pressurization and encourage more efficient use of air by providing a fast, yet precise response to fluctuations in air demand, thereby stabilizing system pressure and eliminating damaging compressor cycling.
The ability of pressure flow control valves to stabilize compressed air system pressure has several advantages, including:
- Energy efficiency: By stabilizing system pressure, pressure flow controls minimize instances of over-pressurization and compressor cycling so the pneumatic system will consume less energy and become more efficient, reducing energy waste and utility bills.
- Reducing artificial demand: Because pressure flow controllers regulate the air compression system so that it operates effectively at minimum pressure, artificial demand and leaks will consume less air, further reducing energy consumption.
- Better performance of pneumatic equipment: A flow control valve will stabilize the system so that pneumatic tools and automated equipment will experience smoother, more effective and more consistent operation.
- Increased productivity: When pneumatic tools and automated equipment are operating under optimal conditions due to stabilized pressures afforded by pressure flow controls, the reliability of the operation is enhanced and will result in greater levels of productivity and throughput.
- Minimized downtime: Because pneumatic flow control valves prevent excessive compressor cycling and stabilize pressure, there is less wear and tear and stress on pneumatic system components, as well as the tools and equipment they serve. This helps to prevent breakdowns, reduce downtime and minimize maintenance spending.
- Longer equipment service life: By preventing compressor cycling and pressure surges, pressure flow controls minimize air compressor deterioration, preventing premature failure and providing a longer operating life for the compressor.
- Reduced costs: Pressure flow controls stabilize pressure, helping to reduce energy costs. The resulting reduction of over-pressurization and compressor cycling will also minimize maintenance requirements and prolong equipment replacement, further reducing operating costs.
Pressure flow controls provide an effective way to stabilize pneumatic system pressure, even during fluctuations and periods of peak demand, helping to boost energy efficiency and reduce equipment repair and replacement. And, by maintaining stable pressures, pneumatic flow control valves help to optimize the performance of automated pneumatic systems and air-operated tools, increasing productivity by providing smooth and consistent operation. To learn how the installation of pressure flow controls can optimize your pneumatic system, please contact the compressed air experts at JHFOSTER, a Tavoron company, today.