3 Ways Pneumatic Control Valves Support Sustainability Efforts
While the main objective in any manufacturing facility is to produce product, minimizing a plant’s environmental footprint and advancing sustainability efforts are undoubtedly growing corporate concerns. For this reason, there has been a strong emphasis on improving the efficiency of pneumatically driven processes. While there are many ways to reduce the energy consumption of pneumatic systems, such as preventing leaks and reducing pressure, few recognize the role that pneumatic control valves can play in bettering the efficiency of pneumatically operated processes, as well as the overall environmental footprint of the plant.
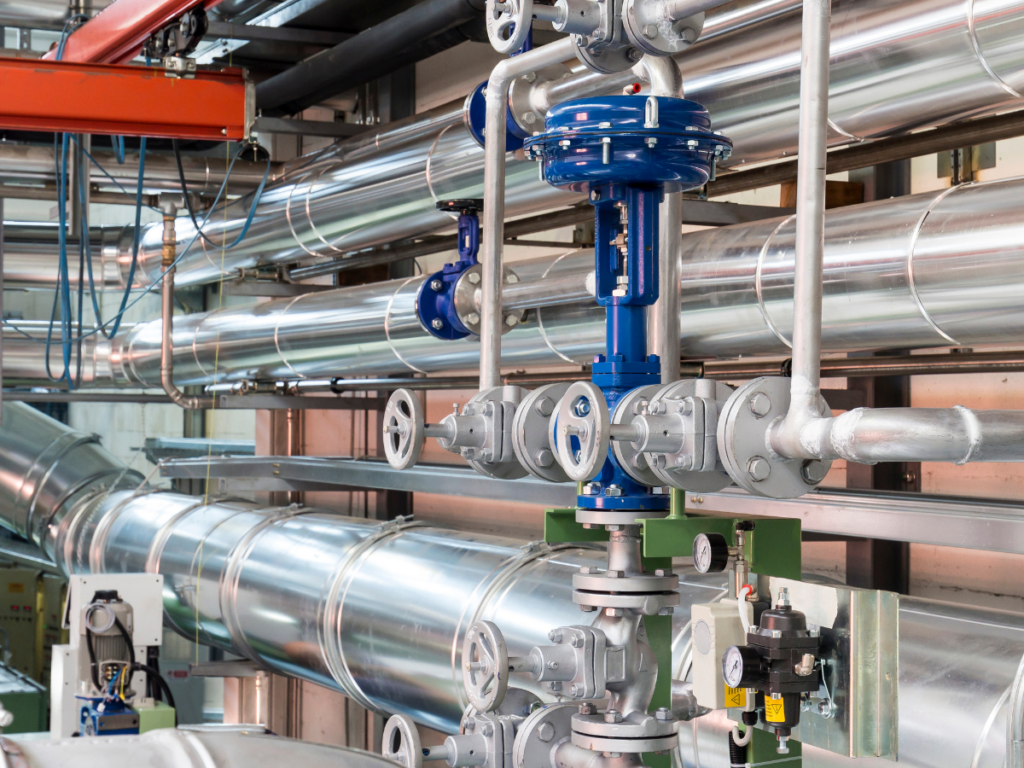
What is the Main Function of a Pneumatic Control Valve?
Pneumatic control valves can regulate the direction, rate, pressure and amount of compressed air that is allowed to pass through a pneumatic system. In order to control the passage of air into the tubing or pipes of the pneumatic system or into pneumatic devices or equipment, the valve is actuated to an open or closed position, according to system demands. The movement of the valve is accomplished either mechanically, pneumatically or electronically via a solenoid or motorized actuator, depending on the design of the pneumatic system.
There are several types of pneumatic control valves and the application dictates which type is specified. Some commonly used pneumatic control valve types and their characteristics include:
Butterfly valves, which offer compact size and are lightweight, making them suitable for applications in which space is limited, but the flow of air must be regulated.
Poppet valves, offer high flow and durability. Also commonly used on automated machines and production fixtures.
Ball valves, which are durable and require very little maintenance, making them suitable for controlling flow in high-pressure applications.
Spool valves, durable and commonly used on automated machines and production fixtures.
Globe valves, which are commonly used in applications with linear flows and offer precision and accuracy.
Further, pneumatic control valves may be categorized by the number of entry or exit points, by their resting state or by their actuation method. Here are a few ways in which you may see them categorized:
- 2-, 3- and 4-way directional valves are classified based on the number of ports they offer. Each port serves a purpose such as inlet or outlet.
- Normally open or normally closed valves are categorized by their unactuated, or resting, state. These regulate airflow when in their unactuated state, so normally closed valves do not allow airflow, while normally open valves allow air to flow freely.
- Spring-offset pneumatic control valves use a spring mechanism to open or close ports when the valve is in its resting or unactuated state. The springs may work to return the valve to its prior position after actuation.
3 Ways Pneumatic Control Valves Help Boost Plant Efficiency
Lately lowering energy consumption is a high priority in the manufacturing industry and it’s no secret that unchecked pneumatic systems can be energy hogs. U.S. Department of Energy (DOE) statistics estimate that manufacturers spend over $5 billion each year on energy for compressed air systems and that compressed air systems account for 10% to 30% of the energy used in the average industrial facility. However, the DOE also suggests that energy efficiency of a typical compressed air system can be improved by 20% through system optimizations, including stopping leaks, regulating pressure and using appropriately sized components.
Because pneumatic control valves are used to control flow and pressure, they also play a pivotal role in minimizing the energy consumption of the pneumatic system, thereby improving the overall environmental footprint of a facility in several ways, including:
Providing flow control | The main role of pneumatic control valves is to provide precise control over the rate, pressure and flow of air through the system. By accurately maintaining the appropriate flow rate, control valves can help optimize not only the performance of the pneumatic system but can also increase its overall efficiency. |
Improving energy efficiency | Because pneumatic control valves control the flow of air, they can help reduce energy waste in a facility by ensuring that only the necessary amount of air, at the appropriate pressure and rate, is sent to the pneumatic system or device. This prevents the system from applying too much air, thus saving energy. |
Enhancing process control | Since pneumatic control valves precisely control the pressure, rate and flow of air in the pneumatic system, they also play a role in controlling the process. By maintaining the desired flow rate and pressure, pneumatic control valves not only optimize the performance of the process, but they can assist with bettering the efficiency of the process and the facility. |
5 Ways to Boost the Efficiency of Pneumatic Control Valves
While pneumatic control valves are already integral to increasing the efficiency of the pneumatic system and supporting sustainability goals of the facility thanks to their role in controlling the rate of air in pneumatically operated processes, there are ways that the efficiency of the valves themselves can be improved, further reducing a energy consumption and supporting sustainability efforts, including:
- Use properly sized pneumatic control valves: Correctly sizing pneumatic system components, including the control valves, can help improve the energy efficiency of the system. So, when selecting a pneumatic control valve be sure it is properly sized. Remember that an undersized control valve may cost less upfront, but it will require the compressor to work harder in order to get the required pressure to the actuators.
- Use properly sized tubing and fittings: Using the correct diameter and shortest tubing possible in a pneumatic system will help reduce both energy consumption and cycle times. Hoses supplying compressed air to machines, and tubing between the pneumatic control valves and system cylinders should be kept to a minimum, as longer lengths will require more pressure to supply the proper rate and speed of air to the end point.
- Reduce pressure when possible: Use of a main plant flow control valve, set to maintain a constant minimum pressure within the compressed air distribution system, and point of use pressure regulators on machines set at the machine manufacturer’s recommended pressure will help maximize efficiency and reduce leak losses.
- Minimize leaks: DOE statistics show that manufacturing plants lose about 30% of the generated compressed air to leaks, valves and seals are common areas of leakage in pneumatically operated systems and processes. To help prevent leaks, ensure that seals are not deteriorated and that the proper valve design is used. Also, in some cases installing a valve that shuts off the compressed air supply to a machine when its off-line can help reduce leaks.
- Use energy efficient pneumatic control valves: As energy efficiency becomes a higher priority, valve manufacturers are working to make their offerings more energy efficient. Many now offer pneumatic control valves that are designed with better efficiency in mind. They may offer low-friction seals and optimized flow paths to minimize pressure drop and reduce energy usage.
Recognizing the role that pneumatic control valves can play in reducing the energy consumption of the pneumatic systems and processes in a facility and taking steps to ensure that they are properly sized and sealed and employ energy saving designs and features can help manufacturers boost the energy efficiency of the pneumatic systems, thereby improving the environmental footprint of the entire facility, which can make a significant impact when sustainability is the goal. For more information on pneumatic control valves, please contact JHFOSTER.