What to Expect from a Professional Air Compressor Repair Service Call
Manufacturers depend on their air compressors so maintenance and repair are essential; however, in-house maintenance staff often lack the time to conduct routine preventive maintenance and the experience to handle more complex compressor repairs. Fortunately, professional, experienced repair technicians are available to help you take care of your compressor so it will continue to take care of your manufacturing business for years to come.
Here we share the details about what you can expect from a professional air compressor repair service, as well as when and why you should call in the pros.
The Importance of Air Compressor Service and Repair
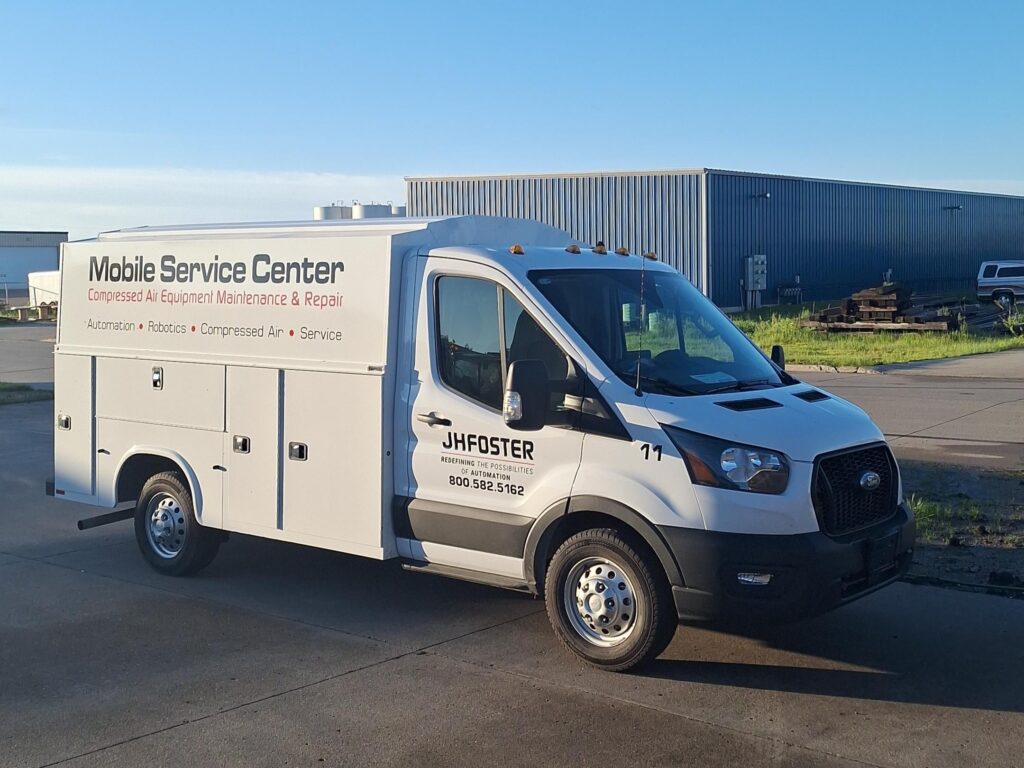
A well-maintained air compressor will not only keep your business up and running, but it will also save money. Performing regularly scheduled inspections and preventive maintenance allows repair technicians to find minor issues before they become larger problems that stop production and result in costly downtime and emergency air compressor repairs.
Among the benefits of regular air compressor service and repair are:
Enhanced reliability | Scheduled inspections and preventive maintenance identify and remedy small issues to prevent significant damage down the road. By addressing early signs of wear and tear on critical components, reliability of the air compressor is enhanced, increasing facility uptime and extending the lifetime of the air compressor. |
Minimized downtime | By detecting and attending issues when they are minor, lengthy bouts of unscheduled downtime are minimized, reducing production losses and lengthy outages. |
Improved air quality | Regular preventive maintenance, such as filter changes and ensuring proper drainage, will help keep the air compression system free of dirt, dust and moisture that can hinder the purity of the treated air, thus ensuring high-quality compressed air. |
Energy efficiency | Addressing clogged filters and air leaks will allow air to flow freely, helping to prevent pressure drops and boost energy efficiency of the compressor. |
Cost savings | By properly maintaining air compressors and repairing small issues before they result in pressure drops or unscheduled downtime, the business will save on repair costs, electric bills and premature replacement of the compressor itself. Additionally, downtime will be minimized and productivity will increase. |
What to Expect During Routine Air Compressor Service and Repair
While most in-house maintenance technicians can handle inspections and minor service or repairs, most lack the time and resources needed to keep up with regular preventive maintenance activities. For this reason, it’s often wise to call in experienced air compressor repair technicians to conduct scheduled preventive maintenance and minor repairs.
Typically, a preventive maintenance visit from a professional air compressor repair service includes:
- A thorough inspection of the system.
- Load/unload pressure, ambient/discharge temperatures, running voltages and other measurements will be taken to help calculate the leak rate, set alarm thresholds and identify energy losses.
- Water condensate levels should be checked and drains should be inspected for functionality.
- Safety and control systems will be tested to ensure that all shutoffs, alarms and controls are operating properly.
- Cooling systems, coolant levels and fans will be inspected to prevent overheating during operation.
- If any parts are found to have damage or wear and tear, replacement will be recommended and handled, if approved.
When to Call in a Professional Air Compressor Repair Service
Even if the maintenance department has the expertise and time to perform regularly scheduled preventive maintenance activities, there are times when a professional repair technician may be needed to handle more complicated or complex repairs.
Some issues that may necessitate a call to an air compressor service and repair expert include:
- Diagnosing pressure drop: Pressure drops can be caused by any number of issues, such as clogged inline filters or compressed air leaks, which may be difficult for in-house personnel to diagnose and locate within the system. Managing pressure drops is important because pressure drops result in inefficient performance and may stress the air compressor and components, resulting in downtime or premature failure.
- Complex repairs: Issues such as moisture in air lines, motor damage and other complex repairs may require the attention of an air compressor repair service to ensure the issue is properly identified and repaired.
- Complete shutdown: If the air compressor experiences an unexplained shutdown, a call to a professional repair technician is likely required to diagnose and fix the problem.
- Repair vs. replacement recommendations: While proper maintenance should assure the longevity of the air compressor, there will come a time when owners must choose between repair or replacement. Experienced air compressor repair service technicians can make informed recommendations.
- Safety inspections: Air compressors are generally safe to operate, but periodic shutdowns for safety inspections are recommended. They may reveal issues with safety shutoffs, alarms or controls, as well as wear, corrosion, faulty valves or electrical problems that could pose safety issues if neglected.
The Advantages of Using an Experienced Air Compressor Repair Service
Even if in-house maintenance staff knows how to repair air compressors, there are some valid reasons for outsourcing routine maintenance and compressor repair to a trained repair technician, including:
Reduced downtime
Professional air compressor repair services have access to a wide variety of parts and components that may take in-house maintenance staff significant time to source and receive. This means professional services can typically complete repairs faster than in-house staff, allowing downtime reductions.
Experienced repair technicians
While in-house maintenance staff may be well trained, they aren’t likely to be certified specialists with extensive experience in air compressor repair. Professional repair technicians have the training, knowledge, and equipment needed to identify and address a range of air compressor issues.
Advanced tools and technology
Professional air compressor repair companies invest in the latest tools and diagnostic equipment. This helps ensure that minor issues are identified and addressed before they result in catastrophic failure.
Focus on core business
Outsourcing air compressor service and repair frees up in-house maintenance staff to maintain production equipment, which is essential to the core business of manufacturing.
If you’re interested in learning more about professional compressor repair, please inquire about JHFOSTER’s air compressor repair service and how it can benefit your business.