The Essentials of Industrial Control Panel Wiring
When it comes to industrial automation and control systems, the way industrial control panel wiring is laid out and managed plays a significant role in the performance, efficiency, safety and maintenance of the control panel and the equipment it operates. A thoughtful, well-organized wiring system can help increase the efficiency of the equipment, boost safety for operators and maintenance staff and reduce troubleshooting and maintenance time. This blog will explore seven essential best practices for wiring industrial control panels.
What is an Industrial Control Panel?
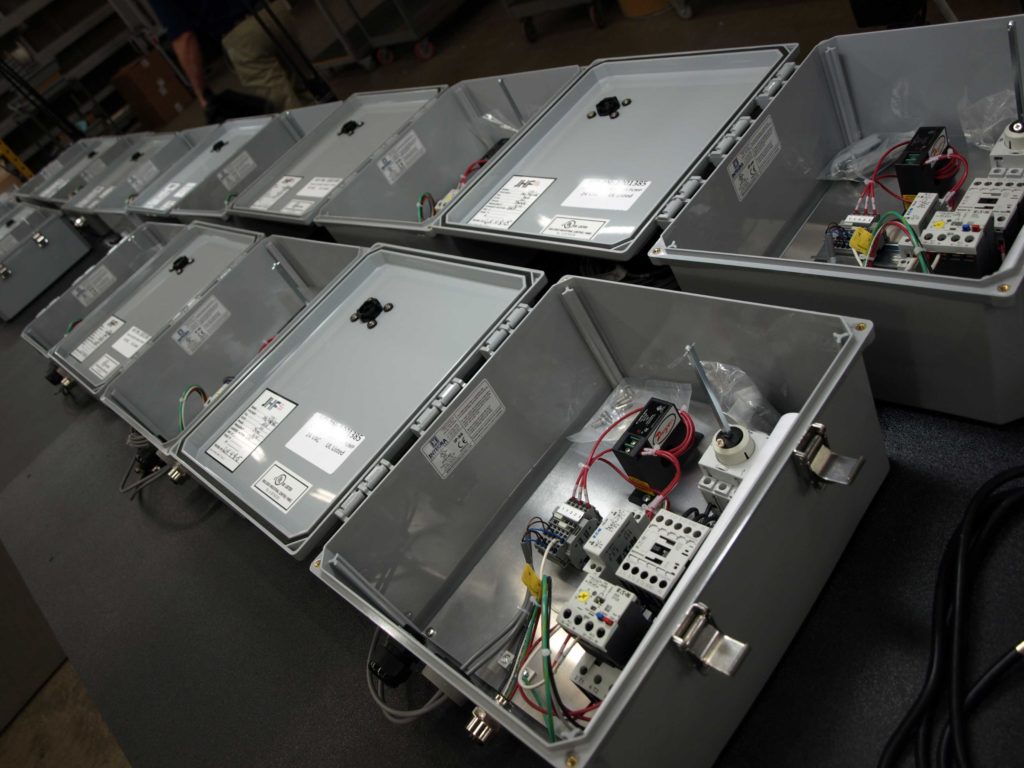
Industrial control panels are used to monitor and control automated industrial equipment. Common functions include turning equipment on and off, regulating speed or other parameters, monitoring and controlling operations and providing access to emergency stop devices.
Several types of industrial control panels may be found in industrial facilities, including:
PLC control panels |
HMI control panels |
Relay control panels |
Pump control panels |
The Importance of Effective Industrial Control Panel Wiring
Because industrial control panels serve as the nervous system for automated equipment in that they send the power and signals that control the operation of machinery and equipment, it’s important to keep in mind that control panel wiring directly impacts performance.
Proper wiring techniques within control panels provide valuable benefits, including:
- Enhancing safety: Proper control panel wiring selection and layout can prevent issues such as short circuits, fires and accidental contacts.
- Improving efficiency/reducing downtime: When control panel wiring is effectively laid out and labeled, it provides easy access to components and electrical panel parts, reducing the time it takes to troubleshoot issues and perform necessary maintenance and enhancing control panel and equipment operation and uptime.
- Regulatory compliance: There are several standards regarding industrial control panels and control panel wiring, including National Fire Protection Association (NFPA) 70, Underwriter’s Laboratory (UL) 60947/UL 508 and NFPA 79. These must be followed to ensure safety and compliance.
Regulations Regarding Control Panel Wiring
Due to the safety risks associated with industrial control panels, there are several standards that apply to control panel manufacturing, as well as to the design and installation of control panels. These should be adhered to for safe operation of the equipment and to prevent fire and electrical risks. Three relevant guidelines include:
NFPA 70
Put forth by National Electrical Code (NEC) and issued by NFPA, this standard applies to U.S. electrical installations and covers many topics. The most relevant to wiring include circuit protection, voltage limitation, wiring clearances, routing and materials, required signage and labeling and temperature ratings for electrical devices inside an industrial control panel.
NFPA 79
This standard focuses mainly on wiring regulations for industrial machines, including control panels that operate at 600 V or less. There is information regarding proper wiring size and wiring installations, including wire trays and conduits. This is a critical standard for control panel wiring and design.
This standard applies to industrial control equipment, including control panels and includes information about motors, load circuits, power circuit wiring and guidelines for control circuit design.
7 Best Practices for Control Panel Wiring
Per the standards listed above, there are many specifications about control panel wiring size, type, space, routing, safety circuiting, grounding and labeling. While understanding, adhering to and applying the guidelines presented in the NFPA and UL standards is mandatory for compliance and will ensure the highest levels of performance and safety, below are seven best practices to keep in mind for efficient and safe industrial control panel wiring.
- Pay attention to sizing: NFPA 79 discusses wiring regulations for industrial control panels operating at 600 V or less, as well as detailed information about wire size selection. Typically, wires and cables should have the proper insulation thickness for the application to ensure that the proper voltage is applied to the components and electrical panel parts. Keep in mind that different components within the same control panel may have different voltage demands, so different wiring gauges may be needed.
- Select the right type of wire: Industrial wire is available as stranded or solid. Solid wire offers a single core, while stranded wire is a twisted bundle of slimmer wires. Stranded wire generates less heat and is more resilient and flexible, but may not be suitable for certain high-current applications. Pay attention to the type of cable jacketing and wire insulation materials, as well. Different materials offer different performance, temperature, flame resistance, corrosion resistance and other specifications. The selected wire must be able to withstand the environment and the application in terms of durability, temperature resistance and other factors.
- Optimize wire lengths and bundles: Long lengths of wire result in a disorganized and unmanageable control panel interior and may increase the risk of voltage drop, which will decrease performance of the equipment. For this reason, it’s important to have wires that are just long enough to allow for maintenance and component replacement, but not so long as to create “a plate of spaghetti.” Wire bundling can be used to enhance organization of the wires but should be done with caution as it increases the chance of overheating.
- Practice safe wire routing techniques: Organized wire routing is critical to the safety and performance of the equipment. Wires should run top to bottom and should not be placed diagonally or cross over other electrical panel parts. Control panel wiring should be arranged in a logical order that does not interfere with other components as this could result in short circuiting or signal interference. Wire ducts may be used to organize wire paths and keep wires safely separated to avoid overheating and other issues. It’s also important to segregate power wires and the sensitive wires used for control purposes. If the two are placed too closely together, it may create electromagnetic interference and disrupt control signals.
- Separate high- and low-voltage wires: Segregating high-voltage and low-voltage control panel wiring provides a safer, more efficient wiring solution.
- Employ proper grounding: Improper electrical grounding presents a safety risk and can produce electrical noise that interferes with control panel and equipment performance. Grounding wires should be routed separately from power cables and safety circuits should be properly grounded to prevent shocks and electrocution.
- Remember labeling: Standardized wire colors can be used for different functions (power, signal control) and clear, durable labels should be applied to each wire so that operators and technicians can quickly identify the function of each component and associated wiring points. This will help with troubleshooting and maintenance of the control panel.
Industrial control panel wiring is an often overlooked part of the design, operation and maintenance of control panels, but it should not be ignored as it directly impacts the safety of the equipment and employees and plays a role in enhancing control panel performance. For assistance with control panel selection, design or wiring, please contact an expert at PTS Products, a Tavoron Company.