Legacy System Modernization with SCADA Integration
Many manufacturers rely heavily on their legacy systems, which are often customized to match the needs of the business, but as industrial technology continues to advance, many old-school legacy systems are becoming obsolete. However, legacy system modernization with SCADA integration can help manufacturers remain efficient, agile and viable in today’s competitive business climate.
Why Legacy System Modernization is Essential
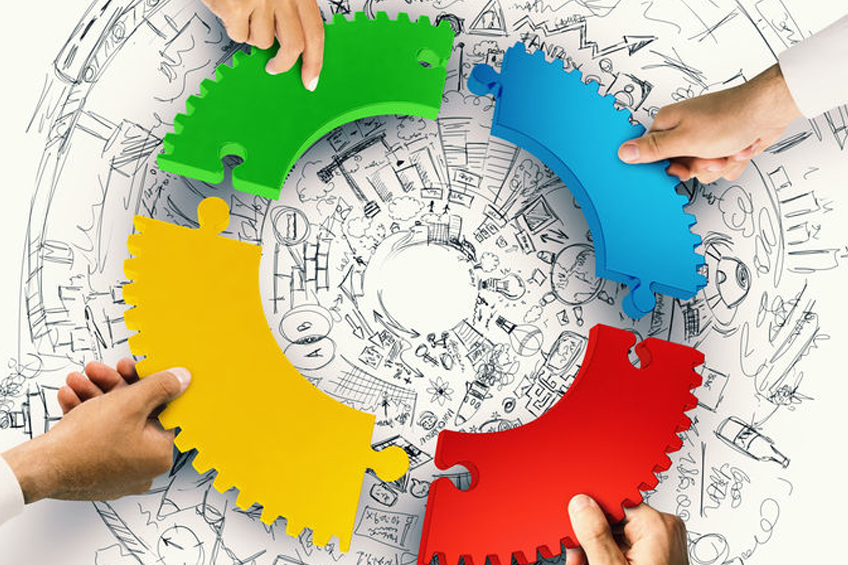
According to an Alteryx-commissioned IDC survey, nearly 90% of all businesses say they are hindered by their legacy technologies. This is because legacy systems are becoming obsolete and are no longer as functional as they once were. As a matter of fact, manufacturers who still rely on outdated legacy systems may experience:
- Compatibility and integration issues: Modern technologies such as SCADA programming and systems, HMI SCADA and data analytics are not always compatible with older legacy systems, which leads to issues with SCADA integration and other technologies. This means manufacturers may not take advantage of benefits such as predictive maintenance and modern automation efficiencies.
- Lack of support: Hardware and software for older legacy systems is becoming outdated and, in many cases, entirely obsolete. When this occurs, parts can become difficult to source and software may no longer be supported.
- Increased maintenance: As legacy systems age, they require more maintenance, which can become expensive and labor intensive. In addition, parts may be harder to source, extending downtime.
- Limited scalability: If legacy systems are not equipped to scale up as the company grows, it can result in inefficiencies and an inability to meet demand for products, resulting in lost business.
- Security risks: Cyberattacks and other security risks are on the rise, but older legacy systems lack modern security features, making them vulnerable to data leaks, ransomware and other common cyber risks.
What Does SCADA Stand For and Why Perform SCADA Integration?
SCADA stands for Supervisory Control and Data Acquisition. In a nutshell, SCADA systems are control solutions that monitor, collect and process real-time data from modern, automated manufacturing technologies. SCADA systems provide operators with a centralized platform where they can see relevant plant data and remotely control equipment and processes based on real-time data.
SCADA systems include several components that work together. SCADA systems gather real-time data from sensors and devices placed on equipment or in a process. The data is transmitted to a centralized SCADA server via wired or wireless networks, such as Ethernet, Wi-Fi or cellular networks. The SCADA server then processes and analyzes the data to provide information regarding equipment health, operational specifications, recent trends and other relevant data. The processed data is then presented to operators via an HMI SCADA interface, which can also be used to control and optimize the equipment or process performance. SCADA systems also offer a feedback loop so operators can monitor the effects of their actions. Finally, SCADA systems offer data logging capabilities so they may be used to store historical data for trend analysis, reporting and compliance.
Modernizing legacy systems through SCADA integration provides a host of benefits, including:
Real-time monitoring and control | Because SCADA systems provide a centralized platform for monitoring and control, operators are provided with real-time visibility and insight into the process, allowing them to make informed, actionable decisions about how to best control and optimize production. |
Reduced downtime | The ability to gather data from the equipment and process also provides insight into the health of the equipment so that maintenance issues can be addressed before they lead to costly downtime. |
Enhanced efficiency | By providing real-time control for process optimization and equipment effectiveness, SCADA integration allows manufacturers to increase their uptime and productivity. |
Improved quality | Because SCADA systems continuously monitor and provide real-time data into the process, operators can see when process parameters are moving out of specification and can quickly take action to return the process to normal operations. SCADA systems can also provide real-time quality checks to ensure that products are within parameters and alert operators when there are deviations, preventing faulty products from reaching consumers and halting production before a batch must be rejected. |
Scalability | SCADA systems are designed to grow as the company grows and can be integrated with other technologies, such as smart sensors, Enterprise Resource Planning (ERP), Manufacturing Execution Systems (MES) and other current technologies, which allow manufacturers to stay up to date with current technology and remain competitive. |
A SCADA Integration Case Study
Because legacy systems are often customized to meet the requirements of the manufacturer, legacy system integration and modernization will look different for each manufacturer, but legacy system modernization with SCADA integration is likely to provide advantages that allow businesses to increase their efficiency and better control their processes to increase agility, efficiency and productivity.
A good example can be found in the legacy system modernization with SCADA integration project performed at a milling plant in Portage La Prairie, Manitoba, by Celco Automation. Here, the legacy SCADA system was no longer supported by the software manufacturer and although the PLC network was functional, the operator interfaces needed improvement.
The milling plant required assistance with converting their outdated and unsupported WinCC graphical interfaces to a new SCADA system on a modern hardware platform. The business wanted to run both the legacy and new SCADA systems in parallel to ensure complete functionality of the newly configured system.
As a first step, Celco converted the programming from outdated Statement List to the more commonly used programming style of Ladder Logic. This conversion would lower the risk of the SCADA migration and provide for a generally more robust system ensuring maintainability for many years.
No migration path existed between the existing WinCC SCADA software and a current SCADA software package, so each screen graphic was recreated by SCADA integration expert, Celco, in Ignition to have a similar “look and feel” to the previous screens to improve functionality and to minimize the operator learning curve. Each PLC tag was manually entered and animated in the graphics and operators were able to view operations in all areas of the plant from their stations.
The third phase of the project involved improvement on the data collection and KPI (Key Performance Indicator) reporting. Celco developed new KPI screens that vastly improved the ability of the client to make production decisions, as well as an improved predictive maintenance program that ensures the plant is running at peak operating efficiency.
Following the modern SCADA and legacy system integration project, the mill now employs a fully functional SCADA platform, which they can leverage and use as the plant expands and new equipment is added.
Legacy system modernization via SCADA integration is essential to survival in the highly competitive manufacturing sector. For assistance with SCADA and legacy system integration, please contact Celco, a Tavoron company. Their SCADA engineers and integration experts are experienced in updating legacy applications with modern SCADA systems, SCADA programming and HMI SCADA to restore functionality and bring efficiency, productivity and quality to new levels at your facility.