Creating a Maintenance Strategy for Industrial Control Panels
Industrial control panels, which control and monitor electrical power distribution, as well as the safety of processes, are crucial to the reliable, safe and efficient operation of industrial automation equipment. Creating a preventive maintenance strategy for control panels can help minimize unplanned downtime, extend the life of the equipment and prevent failure and safety hazards. However, it can be difficult to determine what maintenance activities should be performed on a regular basis. To assist with planning, this blog offers suggestions and provides a preventive maintenance checklist.
The Importance of a Control Panel Maintenance Strategy
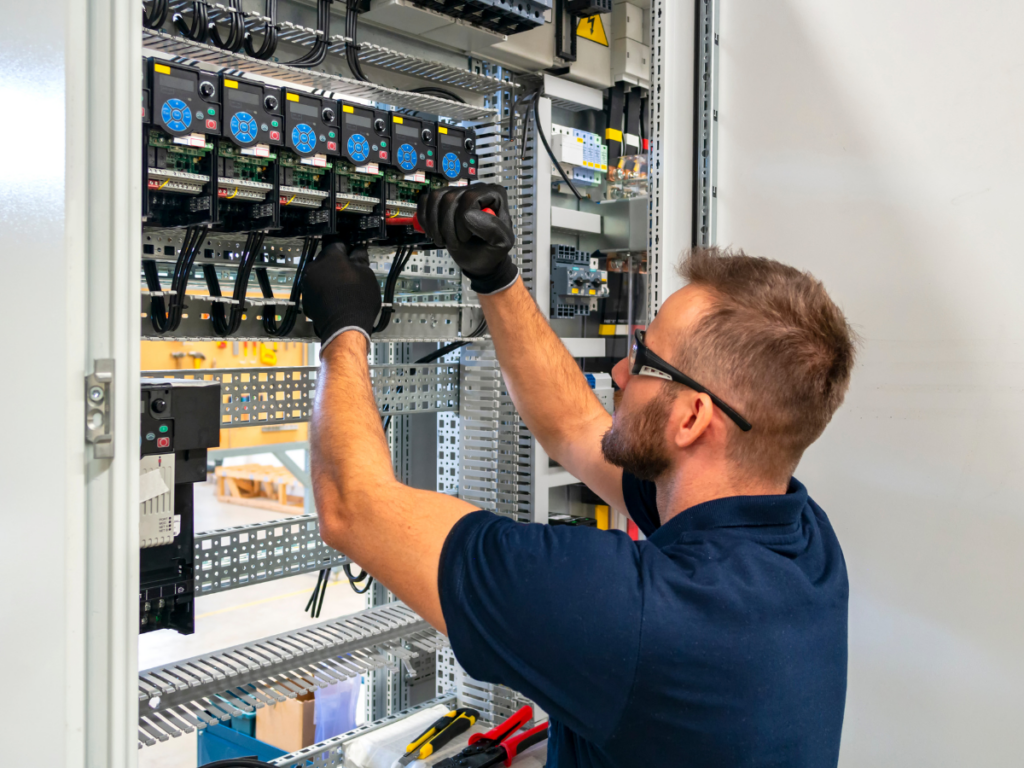
Devising a regular schedule of inspections and performing routine preventive maintenance activities on industrial control panels can go a long way toward ensuring proper operation, reducing downtime and preventing equipment failure and hazardous situations. Remember, preventive maintenance costs are always lower than the cost of equipment failure and downtime.
Here are the biggest benefits of creating a maintenance strategy for control panels:
Prevent Equipment Failure | The components within an industrial control panel are subject to wear and tear, but regularly performing inspections to identify potential issues and following up with necessary maintenance can resolve small problems before they result in costly equipment failure and shutdowns, which helps to reduce extended periods of downtime, while also ensuring the safe and optimal performance of the control panel, as well as the systems it controls. |
Minimized Downtime | Downtime is the arch enemy of productivity, but by performing a regular schedule of inspections and performing routine preventive maintenance activities, it is possible to identify potential issues before major failure and lengthy periods of unplanned downtime occur so production can continue according to schedule. |
Longer Equipment Lifespan | Control panels are essential and expensive pieces of industrial equipment, so users want to get the most out of the investment. Performing regular inspections and preventive maintenance activities not only safeguards proper functionality and reduces downtime, but it can also extend the useful life of the equipment by preventing catastrophic failure. |
Enhanced Safety | While control panels are responsible for the control of automated industrial processes, they also ensure the safety of electrical distribution and often provide emergency shut off for equipment and processes. If an issue within the control panel goes undetected, it is likely that the equipment failure could present or contribute to a hazardous situation. Proper inspection and routine maintenance of control panels help to increase the safety of the equipment, process and facility. |
What to Look for During a Control Panel Inspection
A regular schedule of inspection is the first step in an effective maintenance strategy, as it can help detect potential operational or safety issues. Before performing an inspection or maintenance activity on an industrial control panel, take proper safety precautions, including:
- Making sure the control panel is de-energized and disconnected from the power supply
- Wearing personal protective clothing, including insulated gloves and safety goggles
- Using properly insulated tools
- Using lock out tag out signage and procedures so others know maintenance activities are taking place.
Once safety precautions are in place, you can begin control panel inspections. Some things to look for during a routine inspection include:
Loose Connections
When equipment vibrates, it can dislodge wires, so it’s important to check the security of connections to prevent potential issues. Tighten any loose connections using properly insulated tools and ensure proper torque values per manufacturer recommendations.
Damaged Wires or Insulation
Control panel components are subject to wear and tear, so be sure to visually inspect the wires and insulation within the panel on a regular basis. Look for any damaged wires or insulation, especially those leading out of the control panel, as damaged wires or insulation can pose a safety hazard or short out the entire system. This is a good time to look for signs of overheating, burnt components and corrosion, all of which may precede a more serious issue.
Dust and Dirt
Industrial facilities tend to be harsh, dirty environments, which does not bode well for sensitive electrical equipment. While control panels can be made to withstand these conditions, it’s still important to make sure dirt and debris are not getting inside the control panel as a build up of dust, dirt or debris can cause equipment to malfunction or pose a safety hazard within the control panel itself.
Labels
Proper labeling is essential to the function and safety of an electrical control panel, as well as to regulatory compliance. Be sure to inspect labels and markings for accuracy and legibility and to ensure that they are current.
Often, a regular schedule of inspections will reveal issues that require attention ASAP to prevent unplanned downtime, equipment failure or hazardous operating conditions.
Control Panel Preventive Maintenance Checklist
While visual checks may reveal unexpected issues, it is still important to perform routine preventive maintenance activities in addition to conducting regular inspections.
The following preventive maintenance checklist should help ensure the optimal operation of your industrial control panel, while boosting safety:
- Insulation Resistance Testing: Using a Megger or insulation tester, check the integrity of the insulation and compare readings with industry standards. Low insulation resistance readings may suggest moisture ingress or insulation breakdown, so any areas of concern should be attended to immediately to confirm safety and functionality.
- Functional Testing: On a regular basis, circuit breakers, relays and other safety devices should be tested to ensure safety, while switches, meters and controls should be tested for proper operation. Listen for any abnormal sounds, vibrations or temperatures during functional testing as these could indicate a potential maintenance or safety issue that should be addressed.
- Replacing Components: If any damaged wires or components are discovered during an inspection or malfunctioning components are identified during testing, they should be replaced ASAP. Be sure replacement parts are compatible with the control panel and satisfy manufacturer specifications.
- Verification: After performing inspection, testing or maintenance, restore power to the control panel and monitor operations to be sure that it is functioning correctly. Any abnormalities during start up or operation, such as tripping circuit breakers or equipment malfunctions, must be addressed. Finally, verify that all circuits, controls and safety devices are fully functional.
Industrial control panels work hard to control, monitor and uphold the safety of your equipment and processes. A maintenance strategy that includes a regular schedule of inspections and preventive activities will go a long way to safeguarding the performance of your industrial control panels so that downtime is minimized, uptime is maximized and equipment functions optimally for as long as possible. For more tips on control panel inspection and preventive maintenance practices, please contact PTS, a Tavoron company, today.