Why Every Rotary Screw Air Compressor Needs an Air Dryer
Moisture is the enemy of every compressed air system as it can damage components including piping and valves, as well as the pneumatic machinery and tools it operates and can lead to the delivery of impure air that may result in contamination of finished goods. However, water vapor is an inevitable byproduct of the air compression process, making an air dryer an essential part of any compressed air system.
This blog will discuss the basic operation of rotary screw air compressors and the importance of integrating an air dryer to treat wet air so that you can avoid unnecessary maintenance, production shutdowns and the manufacture of low-quality products.
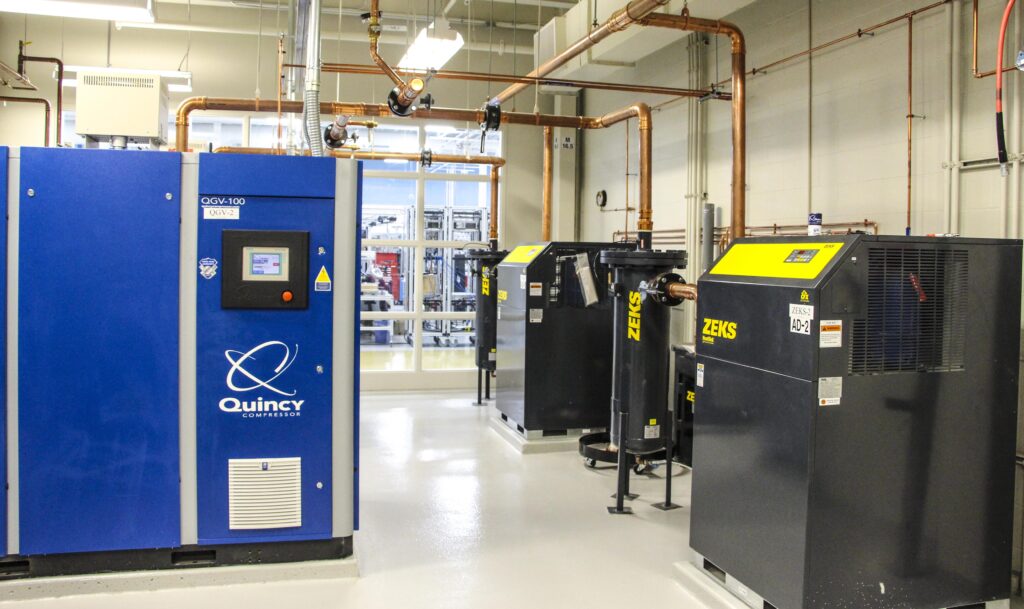
What is a Rotary Screw Air Compressor?
Sometimes called a “twin screw compressor,” a rotary screw air compressor is one of the most common types of air compressor used in industrial facilities. A rotary compressor features a pair of enmeshed helical screws through which intake air is forced. As they revolve, the screws interlock and create a series of chambers. As the air is pushed through the revolving screws, its volume is reduced, thus “compressing the air.” At the same time, this creates a vacuum that pulls more intake air into the chamber.
Why Does a Rotary Compressor Create Moisture?
While the compressed air produced by a rotary screw air compressor is needed to power industrial equipment and tools and sometimes used in the manufacturing or production process itself, the compression process can generate unwanted moisture. This is because when hot, humid intake air is squeezed into a smaller volume under high pressure, the air is unable to retain that same volume of moisture and, as the air cools after the compression process, the resulting water vapor condenses into a liquid.
An air dryer can serve as a moisture remover and help ensure that the compressed air entering the pneumatic machinery or the process itself is clean and dry.
The Importance of Air Dryers
Compressed air that retains too much moisture creates a variety of problems, including:
- Corrosion of air compressor parts and piping
- Damage to pneumatic machinery/tools and controls
- Reduction in the lifespan of the compressor and air compressor parts
- Excessive maintenance requirements for air compressor parts and system components
- Contamination of end products
- Frozen lines or components in frigid locations
A compressed air dryer can go a long way to preventing moisture-related damage, reducing maintenance requirements, extending the life of the rotary compressor and system components and improving product quality.
Fortunately, many rotary screw air compressors are available with integrated air dryers, including refrigerated, desiccant and deliquescent (or chemical) type dryers, that will serve as a moisture remover and ensure the production of clean, dry compressed air that is suitable for many industrial applications.
However, integrated air dryers will typically only remove up to 70% of the moisture generated during the compression process, so in humid locations, applications that require very dry or very pure air or facilities that want to avoid excessive maintenance or can’t afford downtime, an additional add-on air dryer is likely a necessity.
In either case, the type of air dryer selected will depend on the specific moisture-tolerance levels and air quality requirements of the application.
Common air dryer types include:
Refrigerated Air Dryers – Refrigerated air dryers cool the air using heat exchanger, a refrigerant circuit and a compressor. Incoming air is chilled, which causes the moisture to condense and collect in a separator until it is drained out, then the air is reheated. Refrigerated air dryers are energy efficient and are ideal in areas where the pressure dew point is above freezing. They find use in many applications including general manufacturing and auto shops. |
Desiccant Dryers – This type of air dryer usually features “two towers” filled with desiccant materials that attract and remove water from the air. Common desiccants are available in silica gel or activated alumina. These types of dryers can sometimes require frequent maintenance and dew point monitoring systems to assure the compressed air meets stringent application requirements. Desiccant air dryers are ideal in low-temperature climates and applications that demand the cleanest, driest air, such as hospitals, pharmaceutical and food processing, electronics production and paint shops. |
Deliquescent or chemical dryers – These air dryers use deliquescent chemicals (such as sodium) to remove water vapor from compressed air. As compressed air passes over the chemicals, water vapor is absorbed. These air dryers do not use electricity, so they will save on the cost of electricity, but the deliquescent chemicals must be replaced once they are saturated, which is an additional cost |
Membrane Dryers – Using selective permeation and a multiple-stage filtration system, membrane air dryers separate moisture from the compressed air. Following the initial separation, the membrane removes remaining water vapor, resulting in clean, ultra-dry treated air. They are compact and require almost no maintenance; however, regular inspections are necessary to ensure that there is no damage, fouling or clogging in the membrane. |
An integrated or add-on air dryer is the best way to keep your compressed air system and its components free of troublesome, damaging moisture and to keep the treated air as clean and dry as possible. To learn more about whether an integrated or add-on air dryer is the best solution for your application and which air dryer type is most suitable, please contact JHFOSTER today.