Custom vs. Standard Industrial Control Panels
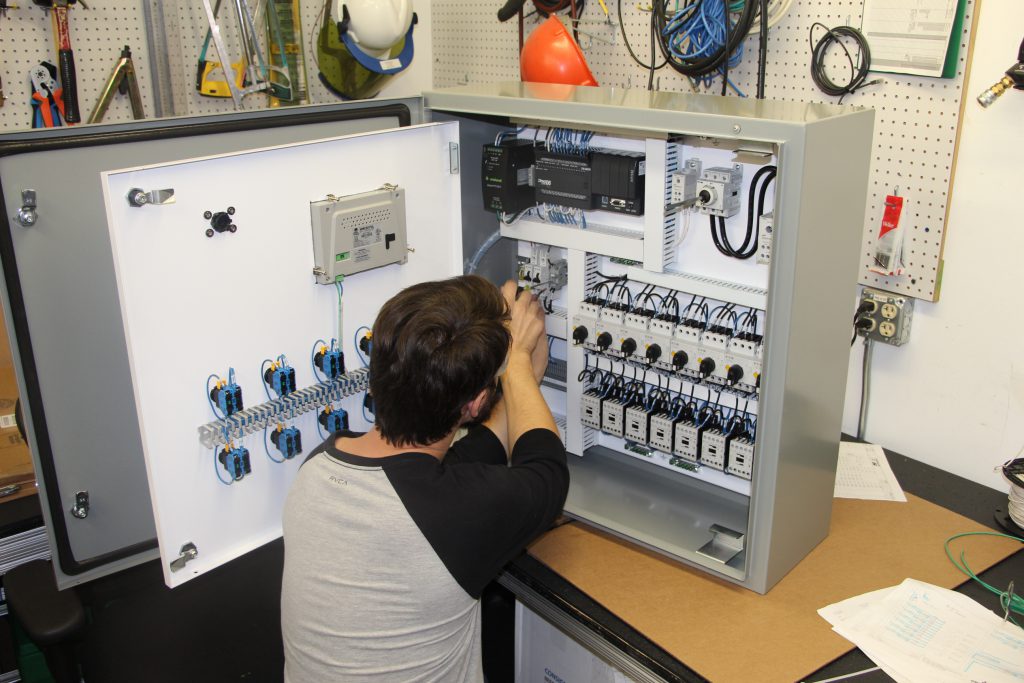
Industrial control panels impact safety and provide electrical supply and control to the machines and equipment that allow a business to successfully make its product, so it’s crucial to choose a control panel that meets the needs of the operation. While it can be overwhelming to consider all the available choices, the first step is usually choosing between a custom control panel or a standard electrical control panel.
This blog will compare these options so you can decide whether a custom-built or a standard model is best for your application.
The Key to a Good Control Panel
Before exploring the differences between a custom control panel or a standard one, it’s important to understand the attributes of a “good” control panel.
Every control panel – whether it’s custom built or standard – should offer:
- UL listing: UL standards exist for a reason – to ensure safety and high levels of functionality – so it is essential that any selected control panel is UL listed. UL-listed control panels have been made to rigorous standards and will meet regulatory mandates.
- A solid layout: A properly laid out control panel provides accessible functionality, as well as adequate space to upgrade the system and perform electrical panel maintenance when needed.
- Appropriate size: A control panel that is too small can present a major problem. Within the panel, there should be enough room around each component for expansion and heat dissipation to protect the system from damage and perform necessary electrical panel maintenance activities.
- Logical component placement: In order to make life easier for operators and maintenance techs, it is essential that components within the control panel are arranged in logical groups so that power can be properly distributed and maintenance can be easily performed.
- Organization: Wires and components should be well organized to simplify identification of the current path and allow users to run additional wires in the future without creating a control panel interior that looks like a “bowl of spaghetti.”
- Proper labeling: If control panel component labeling is ignored or done haphazardly, it can create issues when it is time for maintenance or if cutting power becomes necessary. Each label should be visible and should use clear language or symbols to avoid confusion
The Pros and Cons of Standard & Custom Control Panels
After establishing that a control panel provides safety and functionality to industrial equipment and the features that compose a good control panel, it is still often difficult to choose between purchasing a standard model or a custom-built one. To help narrow down the choice, we will explore the pros and cons of each below.
Standard control panels are readily available through suppliers and usually arrive at the facility very quickly. They are often less expensive than having a control panel custom designed to your specifications because they are produced in bulk quantities specific to customer demand. Standard control panels are typically designed for fast and easy installation and offer a simple, universal design.
On the flip side, standard control panels are limited to standard sizing and material options. Further, even though they are designed for easy installation, it may be necessary to add or resize holes to accommodate specific needs before use. Standard control panels are typically made from stainless steel or polycarbonate, which may not meet the unique needs of an application.
Custom control panels offer several distinct benefits in that measurements, holes, hinges and other components can be designed to meet the exact specifications of the application. They can be made to accommodate special needs, such as operation in hazardous or outdoor locations, additional cooling systems, special locking mechanisms and unique or specialized materials.
However, custom control panels are typically more expensive because they are made to order. This also means that the lead time is generally longer than that of standard control panels. Custom control panels tend to be a bit more complex in design; however, this complexity is often a result of being designed to accommodate unique specifications or specialized components.
Standard vs. Custom Control Panels: Deciding Factors
With the pros and cons of both standard and custom control panels in mind, there are a few factors that should be considered before choosing between these options. Answering the following questions should help make the decision easier:
What are my needs? | What is my timeframe? | What is my budget? |
Does the application have unique considerations or require special features? Factors such as hazardous locations, outdoor installations, high temperatures, special components or specific dimensions may make a custom electrical control panel a better choice. | Because standard enclosures are easier to build, they offer a very short lead time, while custom control panels take longer to design and manufacture. That said, if the project timeline is a significant factor and you know you need a custom control panel, be sure to leave enough time to allow for design and fabrication. | As mentioned above, standard control panels tend to cost less, while custom control panels come with a higher price tag. If capital is strictly limited and the needs of the application do not require special components, materials or other considerations, a standard control panel may be the option. |
While standard control panels are usually the faster, less expensive option for simple installations, custom control panels can benefit applications with unique needs that require flexibility and adaptability. In either case, working with a trusted supplier, such as JHFOSTER, or an experienced fabricator, such as PTS, a Tavoron company, will ensure that you receive a