Optimizing Operations with IO Link Asset Monitoring & Diagnostic Solutions
The introduction of Industry 4.0 technologies has allowed manufacturers to begin monitoring assets and employing diagnostic solutions in real time to help optimize operations and increase efficiencies by decreasing downtime and ensuring the most effective use of equipment. However, installation of Industrial Internet of Things (IIoT) technologies can be both time consuming and challenging. For this reason, many manufacturers are seeking reliable monitoring solutions that are easier to implement and provide many of the same benefits.
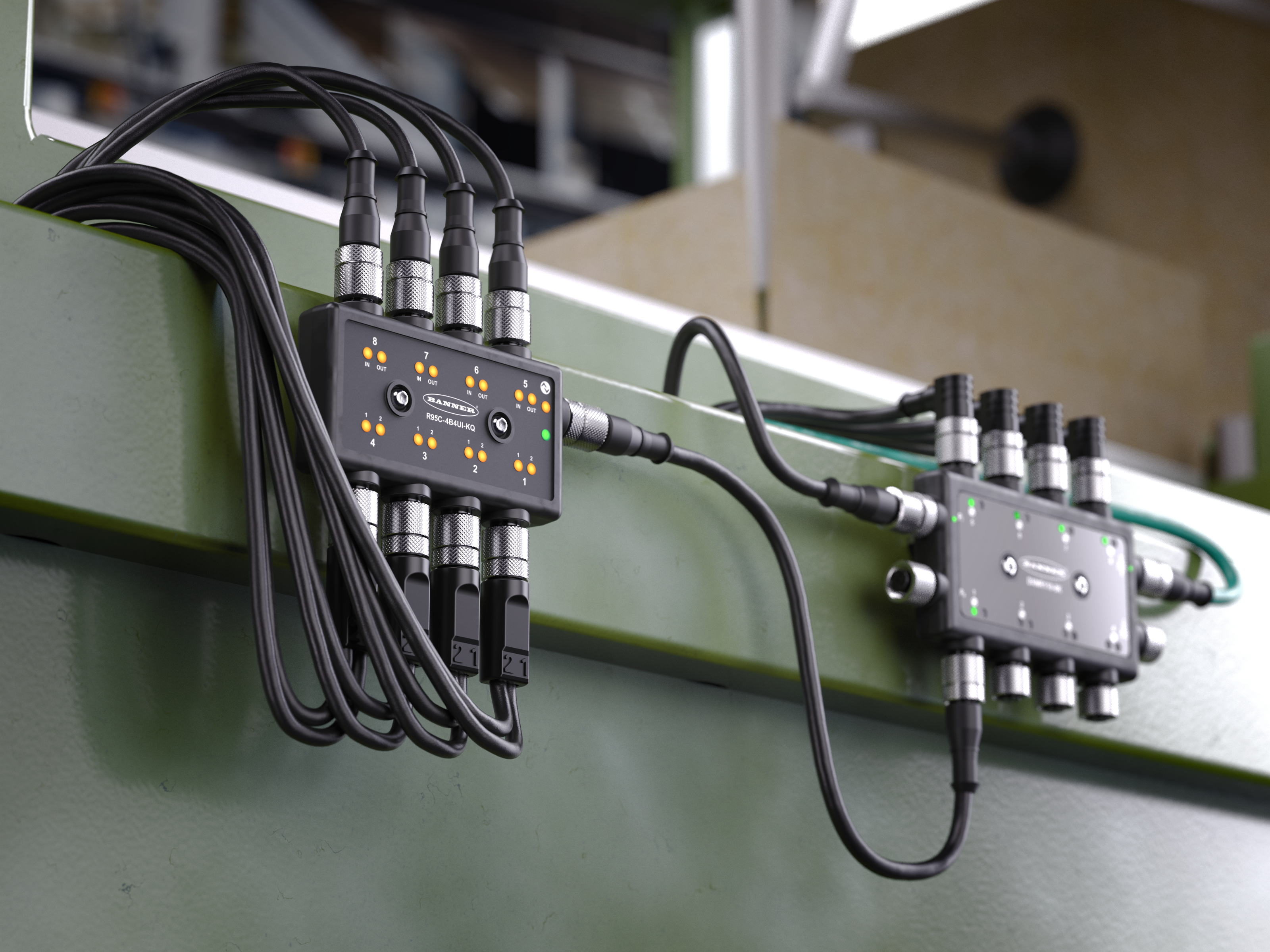
IO-Link Systems Provide Reliable Monitoring Solutions
IO-Link systems are the answer. IO-Link is an open-standard serial communication protocol that allows for the bi-directional exchange of data from sensors and devices that are connected to a master. The IO-Link master can transmit this data over various networks, fieldbuses or backplane buses, making data accessible for immediate action or long-term analysis via an industrial information system or controller such as a PLC or HMI.
IO-Link systems can provide and process several types of information, including:
Process data | Service data | Event data |
addresses the state of the sensors and other connected devices | provides information about the device itself, including configuration information, status and diagnostics | includes data about events that occur during the process but are not typically part of the process. |
This capability provides users with information about their processes and equipment and allows monitoring of machine and device performance, availability and efficiency.
Effective IO-Link systems are available from many manufacturers. For example, Banner Engineering offers IO-Link products that reduce wiring, increase data availability, enable remote asset monitoring, simplify device replacement and provide extended diagnostic solutions. Banner Engineering provides a variety of IO-Link devices for industrial applications including sensors, lighting products, converters, hubs and IO-Link masters.
Using IO-Link for Remote Asset Monitoring
The short-distance protocol provided by IO-Link systems enables data collection from sensors and devices in the field which manufacturers can use for asset monitoring, management and control of field devices.
This makes information from connected data points readily accessible to operators, maintenance technicians and plant managers and provides insight into machine performance. This type of remote asset monitoring means operators can be alerted and react to equipment and process issues in real-time, enabling them to address concerns and potential problems before failure occurs.
Applying advanced diagnostic solutions and asset monitoring via IO Link systems in the following ways allows manufacturers to increase uptime, improve equipment health and efficiency and optimize operations throughout the plant.
Remote asset monitoring
Because the IO-Link system can transmit data over various networks and fieldbuses, the data is available for real-time action or deep analysis to help provide data and information about devices and for remote monitoring of equipment performance. This permits manufacturers to quickly take action to address equipment health issues, process upsets or other events to reduce downtime incidents, which boosts equipment availability, productivity and overall efficiency and improves the bottom line by minimizing costs associated with lost production and prolonged outages.
Diagnostic solutions
IO-Link systems provide diagnostic data for continuous data monitoring and device status. Maintenance activities can be scheduled based on the diagnostic information supplied by the system. Alarms can be created to alert maintenance technicians about problems with sensors and devices before they fail. The ability to predict issues such as a poorly functioning sensor allows maintenance to be performed proactively instead of reactively, bolstering equipment availability and uptime.
The Benefits of IO-Link Systems
While remote asset monitoring and advanced diagnostic solutions are available via other methods, IO-Link systems provide several benefits that make it easier to receive and apply data for these purposes.
IO-Link runs on standard 24-volt DC power, so unshielded, three-core cables can be used. This promotes standardization, reduces wiring requirements and makes IO-Link systems very cost effective and quick to install.
Device replacement is also easier. Device configuration instructions can be saved on a port of the IO-Link master, allowing operators to easily replace sensors because device configuration for replacement sensors is automatically loaded. This not only simplifies device replacement, but also reduces the labor requirements and increases uptime.
Using IO-Link systems, operators can make device configuration changes from the control system. Device programming and configurations can be stored on the PLC and uploaded via IO-Link based on the product that is being run, minimizing time spent on setting up product changeovers and maximizing efficiency.
Because they offer standardized wiring, remote configuration and simplified device replacement, IO-Link systems provide a cost-effective and time-efficient way to introduce Industry 4.0 initiatives into a manufacturing facility, allowing manufacturers to easily access advanced diagnostic solutions and asset conditioning monitoring management to help minimize downtime and costs and optimize operations via enhanced productivity and better overall equipment effectiveness.
For more information on Banner Engineering’s IO-Link system products and how they can be employed as an IIoT-friendly and reliable monitoring solution, please contact Sensors Incorporated today.