6 Benefits of Pick and Place Robots in Medical Manufacturing
Due to increasing market demand and strict governmental regulations, medical device manufacturers must maximize throughput while producing products with strict consistency in a contamination-free, sterile environment. For these reasons, pick-and-place robots present an ideal solution for material handling, assembly and other operations in this unique industry.
The Unique Needs of Medical Device Manufacturing
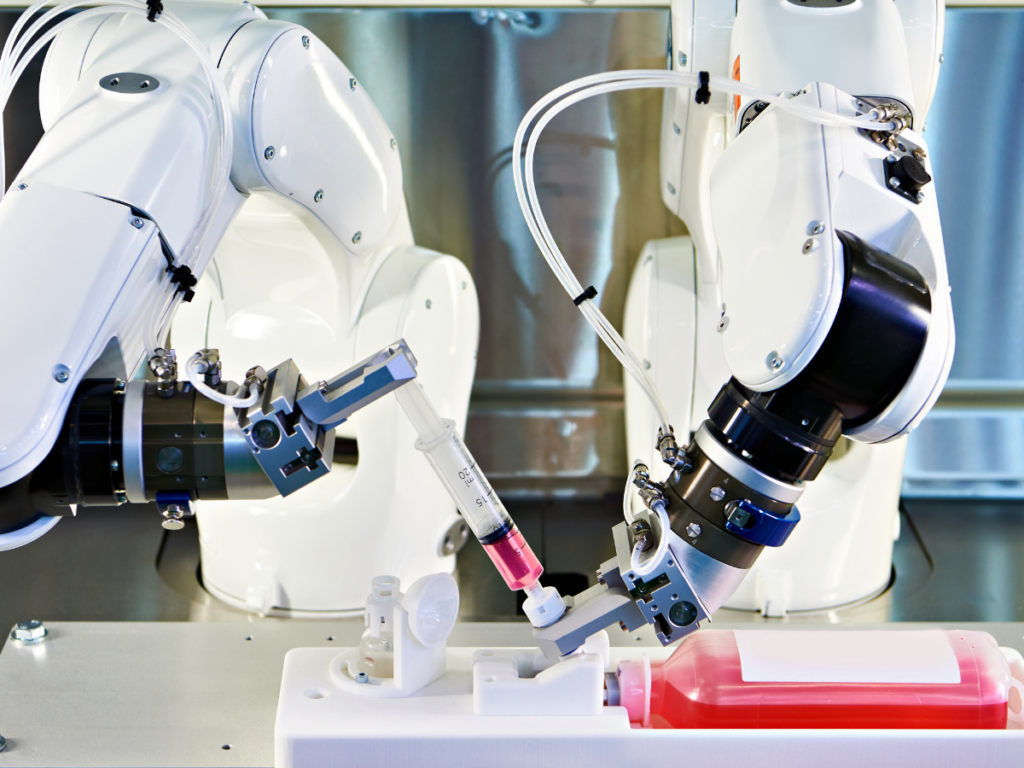
Like most manufacturers, medical device producers face increasing pressure to optimize processes to increase efficiency and maximize productivity. However, medical device manufacturers have an additional burden in that the products and devices made in their facilities are closely regulated and monitored for consistency of process and quality of product since the devices are intended to be used in patient care.
U.S. Food and Drug Administration (FDA) regulatory mandates require not only that medical devices are manufactured and packaged in clean, sterile environments, but also that there is no variation from product to product, which requires precise, consistent and repeatable production processes. Meanwhile, the medical device manufacturing industry is also dealing with a range of challenges, such as rising costs, labor shortages and supply chain issues, making it difficult to meet throughput goals.
Fortunately, automation – especially pick-and-place robots – can help medical device manufacturers overcome these obstacles while simplifying compliance with regulations regarding sterility and consistency.
6 Benefits of Pick and Place Robots for Medical Manufacturing
Pick-and-place robots are typically mounted on a stable surface and are equipped with an arm that reaches over and around the workstation. The arm is often fitted with end-of-arm attachments that are specially designed for gripping the piece the robot is to pick up and move.
They are used for the simple task of picking up a part and moving it to another location for further processing. While it may seem like the applications for pick-and-place robots are limited to simply moving objects from one spot to the next, this versatile automation technology can in fact be applied to a multitude of tasks, such as material handling, dispensing, kitting, assembly, sorting and inspection.
In these and other applications within the medical device manufacturing industry, they bring a wealth of benefits to the table, including:
- Speed: Pick-and-place robots are capable of extremely high speeds – with some moving as many as 300 parts per hour, which means they can move many more objects than a manual worker can in the same amount of time, maximizing efficiency of the production line.
- Increased Throughput: The ability of pick-and-place robots to move more products in the same span of time increases throughput without adding additional production lines or shifts. Additionally, because robots do not require breaks or shift changes as manual laborers do, production can continue without interruption, providing an additional boost to productivity and helping medical device manufacturers meet the growing demand for products.
- Consistency: Consistently producing products to exacting standards is key for medical device manufacturers since variation between products is not permitted per FDA regulations. Replacing manual laborers with pick-and-place robots in sensitive operations will provide greater consistency as human error will be eliminated, making compliance with medical device manufacturing regulations easier than ever before.
- Precision and Repeatability: Pick-and-place robots are designed to perform an operation with extreme and repeatable precision, so medical device components will be picked from the location and placed precisely with no variation each and every time. This means that components will be consistently assembled, sorted or packaged with high levels of precision, accuracy and repeatability, boosting quality and ensuring compliance with regulations that prohibit even the slightest error or variation.
- Reduced Risk of Contamination: Sterility and cleanliness are crucial elements of medical device manufacturing and are closely regulated. Automation lends itself to the mass production of medical devices as it eliminates the risk of contamination stemming from human workers entering the production environment. Further, pick-and-place robots can be designed with sanitary needs in mind, further reducing contamination risks and ensuring compliance with regulations regarding cleanliness and sanitation.
- Offset Labor Shortages: Using pick-and-place robots in place of manual laborers for simple material handling tasks frees up existing employees to perform jobs that require problem solving skills or creativity, which adds more value to the operation. In addition, workers will feel more satisfied with more complex roles and will be more likely to remain in their positions.
Surprising Medical Manufacturing Applications for Pick-and-Place Tech
While it seems like the applications for pick-and-place robots would be limited to simply moving a component from one location to another, these precise solutions can do much, much more. Here is a sampling of the ways in which medical device manufacturers are currently employing pick and place robots:
- Filling vials and syringes
- Bin picking for device assembly of devices
- Bin picking for packaging medical equipment
- Picking and/or assembling kits of dental tools, surgical tools, etc.
- Polishing and deburring
- Finishing components for medical devices such as prosthetics, pacemakers, hip and knee replacements, etc.
- Quality control and inspection of components, devices, pharmaceuticals, etc. (if equipped with vision systems and programmed to do so).
- Case packing wipes, gloves or other sterile products
- Precise application of adhesives during assembly processes
- Precision assembly of medical device components, hearing aids, pacemakers, syringes, autoinjectors, etc.
- Kitting and packaging items, pharmaceuticals and supplements into blister packs or other sterile packaging
- Sorting, counting and weighing supplements and pharmaceuticals
- Sorting and packing sensitive items such as glass vials, autoinjectors and pre-filled syringes
- Assembling kits for diagnostic testing
Pick-and-place robots are a cost-efficient way for medical device manufacturers to keep up with demand for sterile and consistent medical devices even in the midst of rising costs and labor shortages. For more information on how you can apply pick-and-place robots in your medical device manufacturing operation, please contact JHFOSTER today.