An Introduction to Linear Motors for Straight-Line Motion Applications
As the price for linear motors becomes more cost competitive, these devices are more often being considered for motion control projects that demand high speed, fast acceleration and very precise linear motion. While linear motors have been around for a while and can provide significant advantages when properly applied, many people don’t know exactly how a linear motor operates or in what type of applications a linear motor will shine. This blog aims to serve as an introductory guide to linear motors and discusses applications where they are successfully being used as a motion control component.
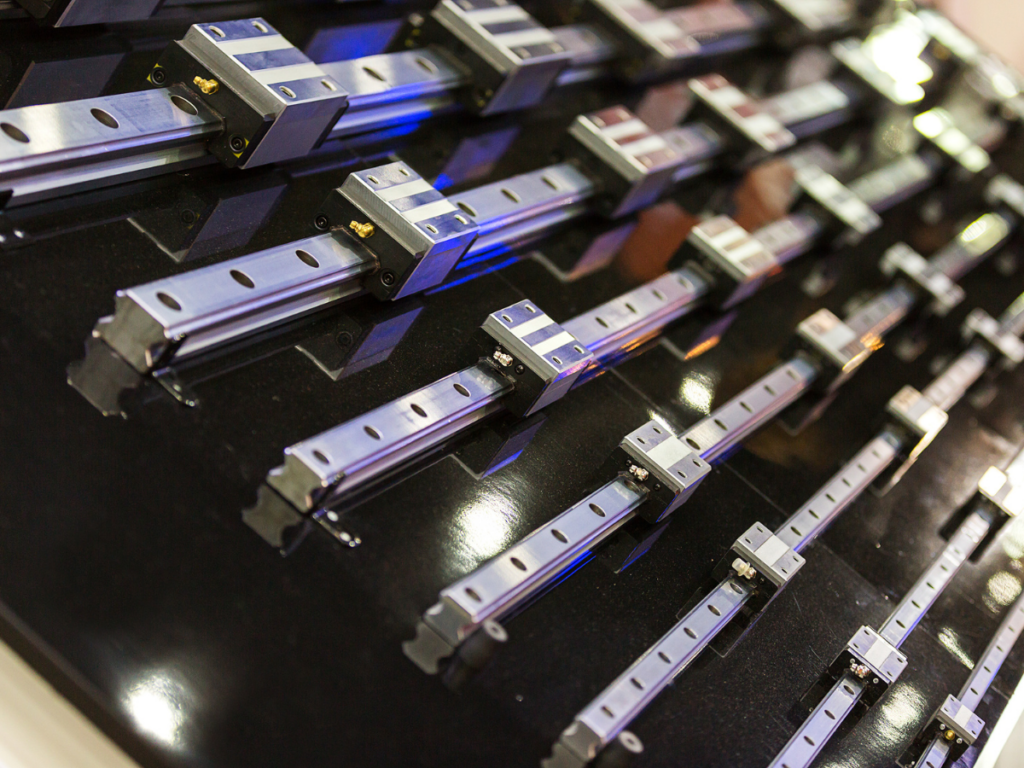
How Do Linear Motors Work?
A typical linear motor can be described as an “unrolled” or “flattened” standard rotary motor. By unrolling a standard rotary motor in this way, linear motors generate force in the direction of travel and produce linear motion similar to that of a linear actuator (which uses a mechanism to convert the turning motion of a rotary motor into straight-line motion). However, the way in which the straight-line motion is accomplished differs in linear motors.
By design, a typical linear motor is made up of permanent magnets and a moving carriage of coils and the direction of current running through the coils magnetizes them and moves them in a straight line along the track. This allows linear motors to apply thrust directly to a load in order to generate linear motion, which means they do not require an intermediate mechanism, such as the ball screw, rack and pinion or rod used in linear actuators. It should also be noted that because linear motors directly couple the load to the motor to create linear motion, there is no associated gearbox as is found in standard rotary motors.
The design and operation of linear motors results in a straight-line motion profile that provides extremely high speeds, super-fast acceleration and outstanding positional accuracy. In addition, because there are no moving parts associated with a gearbox or intermediate mechanism, they are low maintenance devices and are highly energy efficient.
Applications for Linear Motors
Because linear motors have no moving parts and typically include a magnetic or optical linear scale for positional feedback, they are able to achieve very accurate and repeatable positioning. They can also allow the use of more than one carriage, each driven independently on the same guide. In addition, linear motors offer impressive travel lengths along with high speeds and quick acceleration, with typical ratings up to 10 m/s velocity and 10 g acceleration. These features combine to make linear motors attractive and suitable for use in applications such as:
- Packaging, assembly and part-loading equipment
- Semiconductor and LED metrology
- Digital printing
- 3D printers
- Biomedical and small parts manufacturing
- Plastic injection molding machines
- Printing and labeling machines
- Wood, glass and ceramic processing equipment
- Filling machines
- Metering, counting, feeding and dosing equipment
- Sealing and precision pressing applications
Considerations for Linear Motors
While linear motors do provide excellent speed, acceleration and accuracy, there are some things to consider before deciding on a linear motor. For example, linear motors can be difficult to enclose and protect, so they will require seals and protective covers in challenging applications and environments. In addition, because the epoxy used to contain the coils in some linear motor types does not easily dissipate heat, cooling via forced air or water may be required to avoid damaging the motor. Further, the stroke length of linear motors may be constrained in some applications by cable management issues as the power cables must travel along the full stroke length. In addition, because linear motors often contain large magnets, they may create performance issues in magnetically sensitive applications such as medical equipment.
Experts at JHFoster can provide more detailed information on linear motors and whether their high speed, fast acceleration and precision is the right choice for your motion control application.