Using Remote Vibration Sensors to Build a Smart Maintenance Strategy
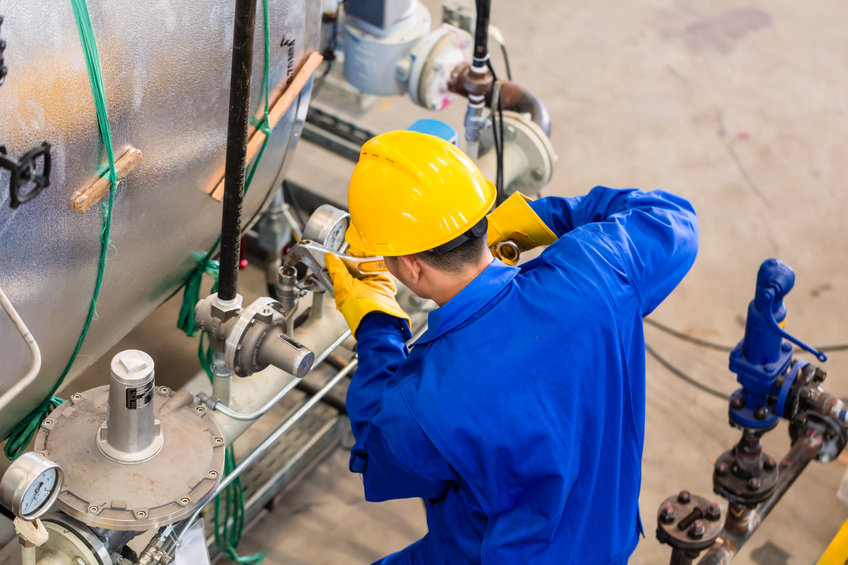
In every industrial facility, the machinery that is vital to production often relies upon pumps, motors and compressors to operate. Unfortunately, this type of equipment is prone to breakdowns that can cost thousands of dollars per hour in lost productivity, repair and labor. One way to prevent equipment failure is by using remote vibration sensors to create a smart maintenance strategy.
By recording and studying the changes in the vibrational patterns of critical equipment, it is possible to find minor abnormalities and identify changes in a machine’s operational behavior that may suggest potential failure so issues can be addressed before resulting in costly interruptions and lengthy downtime.
While most machines vibrate during normal operation, excessive vibration can cause premature wear and tear, shorten the lifespan of machinery and create imbalances that may crack or break components in industrial equipment. Additionally, abnormal vibration patterns may indicate possible issues with equipment. For this reason, implementing a vibration monitoring program as part of an overall maintenance strategy makes it possible to detect changes in vibration as they occur so potential problems can be recognized, diagnosed and repaired before they result in a breakdown.
The Benefits of Vibration Monitoring
A vibration monitoring program can and should be included in all maintenance strategies, including condition-based maintenance, predictive maintenance and prescriptive maintenance programs, as it offers a variety of time and money saving benefits, including:
- Cost Savings: Because vibration monitoring helps to identify potential equipment failures before they occur, it can prevent downtime and repairs, which can cost thousands of dollars per hour in a manufacturing facility and wreak havoc on the production schedule for days to come.
- Improved Uptime: Since vibration monitoring allows early detection, issues with vibrating machinery can be identified and rectified before they negatively affect performance and operations. This means it is likely that monitored equipment will run with higher levels of efficiency, reliability and uptime.
- Identifying Correct Maintenance Intervals: Rather than performing maintenance tasks on a schedule that is dictated by a calendar, vibration monitoring encourages maintenance activities to be performed when needed. This should extend time between maintenance intervals, reduce unnecessary maintenance and labor costs and increase machine availability.
- Reduced Energy Costs: Equipment that suffers wear and tear, imbalances, misalignment and other issues does not run efficiently. By identifying any vibration-related issues and correcting them, it helps ensure that machines are running optimally, leading to lower energy consumption and operating costs.
- Improved Asset Management: The information collected from a vibration monitoring program provides maintenance technicians with a better understanding of the facility’s assets by providing insight into equipment health and lifespan, allowing them to make more informed decisions about repairing machinery or determining when the time is right to replace assets.
Using Remote Vibration Sensors for Vibration Monitoring
Vibration monitoring is a five-step process that includes:
1. Collecting vibration data | The first step in vibration monitoring, collecting the vibration data, can be accomplished using hand-held devices, wired sensors or remote (wireless) sensors; however, the use of wired or wireless sensors makes the job less time consuming and reduces the chances of introducing errors into the data because technicians do not need to walk from machine to machine taking readings, nor do they need to return to the maintenance office and record the data manually. Remote vibration sensors provide more benefits than wired sensors as they do not require expensive wiring and can be mounted on machinery that is difficult to reach or located in distant parts of the facility. |
2. Creating a baseline | The second step, creating a baseline, should include the collection of vibration data from the machine or machines when they are running in optimal condition. Having a baseline measurement for healthy equipment will allow comparison with data that is collected later to determine when there is a change in vibrational patterns under the same running conditions to identify potential issues. |
3. Storing vibration data | Using remote sensors as part of an online monitoring system makes the third step, storing the vibration data, easier. The creation of historical data sets will make comparing baseline and future data sets possible. |
4. Analyzing vibration data | Analyzing the vibration data is key to the success of the vibration monitoring program as simply collecting data is not enough. Rather, as data is collected, it should be compared to the baseline vibration levels so that abnormalities, anomalies and potential failures can be identified with adequate time to schedule repairs and order replacement parts. |
5. Making informed decisions | Using the data in this way allows maintenance techs to make informed decisions based on the stored and analyzed data. This means that when an abnormal running condition or a potential failure is detected, work orders can be issued and prioritized, parts may be ordered in advance and repairs can be conducted in a timely fashion to prevent lengthy, unplanned and expensive downtime, potentially saving thousands of dollars in lost production time and costly failures. Informed decision making also gives the maintenance managers confidence when creating maintenance schedules and budgets, while the earned reliability gives production managers assurance that they will meet production goals. |
With the introduction of the connected plant and Industry 4.0, the use of advanced analytics software and machine learning algorithms along with remote vibration sensors can further enhance the process of analyzing the vibration data as it allows techs to make decisions in real-time and removes the burden of analyzing the data using spreadsheets or other methods. It can also provide insightful diagnostics, which can reduce time spent troubleshooting.
As part of a vibration monitoring program, remote vibration sensors are available for a range of equipment, applications and budgets. Remote vibration sensors can be helpful in creating a more efficient vibration monitoring program that is part of a smarter, more proactive maintenance strategy because they reduce or eliminate the need for a maintenance technician to walk the plant taking measurements with hand-held tools and then transferring the data manually. Rather, remote vibration sensors permit the data to be automatically gathered, stored and analyzed so that maintenance teams can dedicate the time to correcting abnormalities and avoiding future failures, so the plant can remain up and running and, most importantly, profitable. For more information on remote vibration sensors and how they can help you create a vibration monitoring program, please contact JHFOSTER.