Robotic Palletizers Increase Efficiency and Throughput
As the labor shortage and tight budgets continue to stymie industry, modern robotic palletizers provide a way to boost the throughput of palletizing operations, helping manufacturers gain efficiency and output. While old-school palletizers sometimes created issues with product damage, today’s robotic palletizers have been designed to be gentle and fast, as well as more space- and cost-efficient, making them a smart option for many applications.
Robotic Palletizers vs. Conventional Palletizers
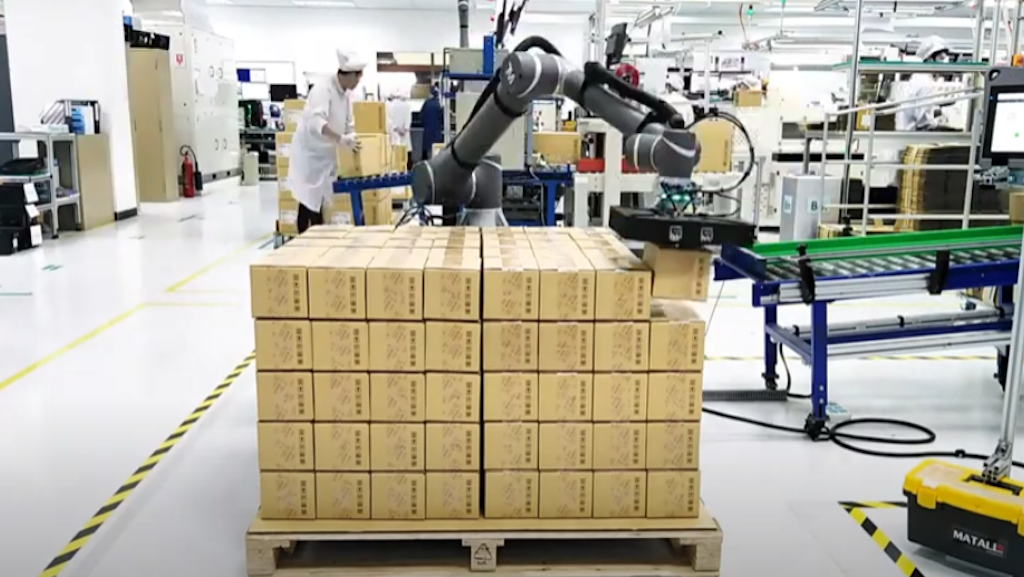
Conventional palletizers have very fast cycle times – up to 200 cases per minute, but that speed comes with some drawbacks. Because conventional palletizing technologies rely on a series of conveyors and components to move products along the line and form them into rows that are then stacked onto pallets, they often require a lot of floor space in the facility.
In addition, products can be damaged or crushed in the process, creating waste and customer dissatisfaction.
On the flip side, although modern robotic palletizers do require an infeed conveyor, they typically offer a smaller, more concise footprint. In addition, robotic palletizers rely on a robotic arm with end-of-arm tooling designed to gently pick up, orient and place individual products into a single stack, which is then moved as one unit, resulting in less product handling and damage and more efficiency. While their ability to perform several functions, such as picking up product and then orienting it so that the bar code is outward facing in the stack, makes them a bit slower than conventional palletizers, they offer the ability to multi-task and combine materials in a way that allows for more efficient handling.
How Do Robotic Palletizers Work?
Robotic palletizers are designed to automate the process of stacking goods and products onto pallets. As products or goods to be palletized move down an infeed conveyor, a robotic arm picks up and orients one or more products and then quickly and accurately places them on the pallet, arranging them into a single stack load. This is called creating a “unit load,” and is a more efficient way to handle the task, as it is faster, more cost effective and more efficient to handle one stacked load than it is to move multiple individual items.
Robotic palletizers continue to do this, constructing layers of product, using slip or tier sheets if needed. Once the pallet is fully loaded, it is removed from the area by an outfeed conveyor for shrink wrapping and the process begins again with a new pallet. While their ability to handle multiple tasks at once (picking and manipulating products for proper display of labels, then stacking them, for instance) does make them slower than conventional palletizers, they are still fast and can run up to 2,000 cycles per hour. In addition, they bring more value to the task as they perform in a more efficient way, while also reducing damage because they can handle stacks versus individual products and offer the use of gentle grippers and other end of arm tooling.
Modern robotic palletizers can handle a range of applications, including standard cases, mixed pallets and bags or they can be customized to handle items like bales or heavy, hazardous materials.
Types of Robotic Palletizers
Classified by configuration and construction, robotic palletizers are available in several different types, including:
In-Line Palletizers | Palletizing/Depalletizing |
These consist of a single robotic palletizer that handles the operation with additional features, such as the ability to place tier or slip sheets and dispense pallets. They can service one or multiple palletizing lines and employ articulated arms with specialized end of arm tooling. In-line palletizers may employ different types of robots, such as pedestal-style robotic arms that are mounted to a stable surface in the work area or gantry-style robots that are suspended from a gantry and move along tracks above the work cells. | These are capable of performing all the functions of an in-line palletizer, but can also perform depalletizing functions in which individual items are separated from the load stack. They are capable of unloading products from mixed pallets and sorting them according to SKUs. However, it’s important to note that these robots do not typically perform both functions – the term simply means the palletizer can be programmed for use as a depalletizer. |
Layer-Forming Palletizers | Mixed-Configuration Palletizers |
These palletizers consist of an integrated system of robots with each performing a single task. For instance, one robot may layer the products, while a second stacks them, which increases the throughput of the palletizing operation, so they are typically applied in high velocity/throughput applications. | Capable of taking boxes and cases of varying sizes and shapes and creating a stable layer, mixed-case palletizers come in a variety of styles. A robot may be mounted to a track, allowing it to move between a series of pallets, select a product and then set it onto the receiving pallet in a stable configuration. Or, there may be a series of conveyors that feed product into a staging area where a robotic arm selects and orients the products, forming layers of properly configured products into a load that is then guided to the final destination where it is lifted onto a pallet by a robot. |
Advantages of Robotic Palletizers
In industries where palletizing is a standard task, it often causes bottlenecks and results in damaged products or mistakes and can cause injuries if handled by manual laborers. However, robotic palletizers offer a lot of benefits including:
- Increased throughput: Robotic palletizers are more efficient and capable of lifting heavier loads than their human counterparts and can operate 24/7, reducing bottlenecks, injuries and inefficiencies in the process.
- Improved safety: Again, replacing manual laborers with robotic palletizers decreases the incidences of repetitive motion injuries associated with bending, lifting, twisting and stacking, as well as those associated with crushing hazards.
- Less waste/better quality: Because robotic palletizers are designed to function without damaging the products, there is less waste and scrap. And, because they are programmed to stack products according to a pre-set configuration, they do not make mistakes, which reduces the incidence of incorrect product being placed on a pallet.
Robotic palletizers are designed to provide the most efficiency possible in a palletizing operation. If your organization seeks to improve throughput and would like to see if robotic palletizers are the right solution, please contact JHFOSTER.