Troubleshooting 7 Common Causes of Piston Air Compressor Failure
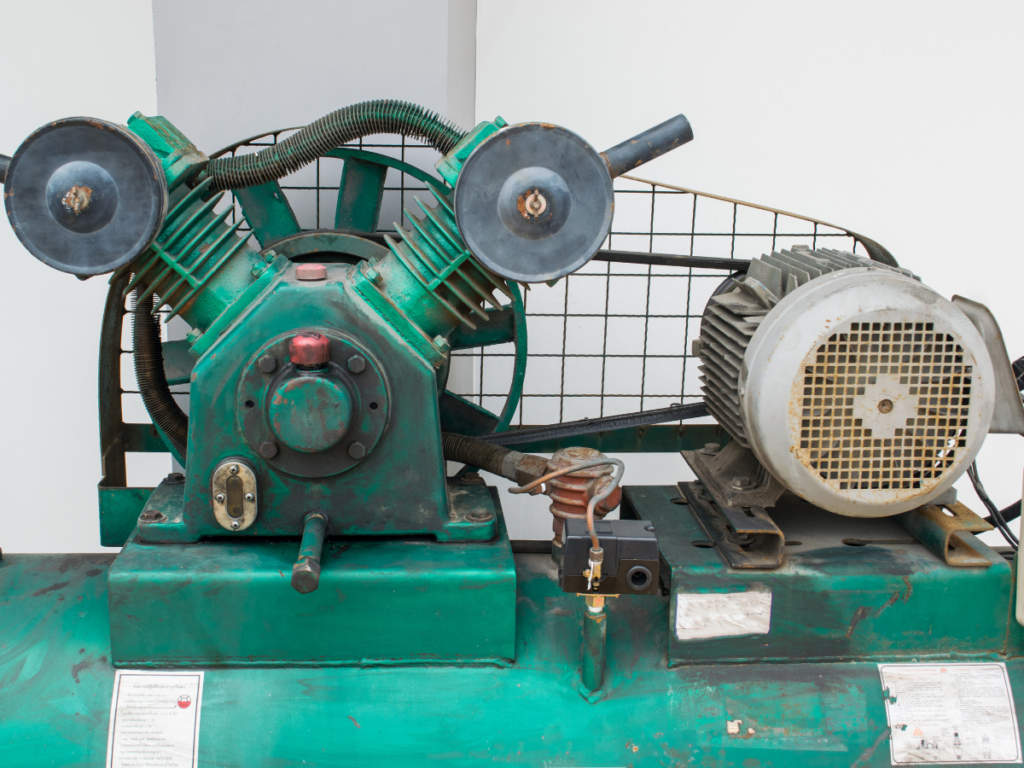
Compressed air is often dubbed as the “4th utility” in industrial facilities because it powers essential tools, machines and processes; however, heavy use of air compressors subjects them to wear and tear that will more than likely result in operational issues and potential failure at some point during the lifetime of the asset. The expense of downtime for the compressor and all the equipment it supplies can be staggering, so quick identification and troubleshooting efforts are key to avoiding lengthy shutdowns.
This blog outlines 7 common causes of piston air compressor failure and suggests solutions that should get the operation up and running again as swiftly as possible.
1. Failure to Start or Stop
Failure to start is one of the most encountered air compressor issues. Often it is simply the result of a disconnected power cord or deactivated power switch. Checking the power button, power switch and breakers will solve this problem. If this is not the case, another common culprit may be a lack of sufficient air pressure, which occurs when the cut-in pressure is not in the correct proportion to the amount of air pressure stored in the tank. For this issue, check the cut-in setting on the pressure switch and adjust it accordingly. Additionally, some piston air compressors have a safety feature allowing them to start but not create any compressed air when low on oil, so be sure to check and change the compressor oil regularly to avoid damaging the compressor.
In normal operation, an air compressor should stop running once the tank pressure hits the cut-off point. Failure to do so could be related to a defective pressure switch. If this happens the compressor will continue to run beyond the maximum pressure setting and in some cases, increasing tank pressure until the safety relief valve opens and releases the excess compressed air continuously until the compressor is shut down. If it is the pressure switch, changing it out should do the trick.
2. Motor and Power Issues
If the compressor is plugged in and working but constantly blows breakers or fuses, it could be a problem with where the compressor is plugged in – Air compressors should only be powered through properly rated connections as power bars or undersized extension cords frequently result in power issues or blown breakers and fuses. Additionally, a worn-out motor can result in power issues. If this is the case, it is likely time to replace the motor. Alternatively, if tripping breakers at start up only occurs when the tank is pressurized the cause could be a defective head unloader valve.
3. Oil Problems
Sometimes compressor failure is related to oil issues. Aside from not making oil changes a priority, which can cause severe damage to air compressors, there may be issues with oil leaks, worn piston rings or use of improper oil viscosity, which will lead to faster than normal oil expiration and damaged equipment. Aerosolized oil can also contaminate machine parts such as seals and plastics, as well as pneumatic tools and accessories and impact the quality of products. Common causes of aerosolized oil include restriction in the air intake, expired or incorrectly applied piston rings, too much oil in the crankcase and improper oil viscosity.
4. The Compressor Constantly Leaks Air
Not only do air leaks lead to excessive energy waste, but they also prevent air compressors from functioning properly. An obvious sign of excessive air leakage is when the compressor is shut off, but the pressure gauge continues to drop. Air leaks may also result in the air compressor failing to turn off and continuing to run because it is compensating for the pressure loss. To solve air leakage problems, it’s important to find the source of the leak and fix it.
5. Pressure and Flow Problems
Worn or damaged components such as the valves head gasket, piston rings, unloader valve, or pressure switch may create a situation where the air compressor is not generating enough air (not permitting the compressor to achieve its normal PSI) or is generating too much air (reaching abnormally high PSI). In either case, check and replace any of the above-mentioned components as needed. If that doesn’t solve the problem, the culprit may be an obstructed or dirty intake filter or a pressure switch that is improperly set. Also, make sure the safety relief valve is working properly.
6. Excessively Hot Emissions
Extremely hot emissions can damage nearby items or surfaces, as well as the internals of the compressor and should not be ignored. Hot emissions can result from dirt on the interior of the compressor, poor ventilation, a worn head gasket or valves or insufficient air intake.
7. Air Compressor is Too LOUD!
While most air compressors are indeed noisy during normal operation, making more noise than is normal is a problem that should be addressed. It may be related to loose parts or components, such as pulleys, belts, belts guards, clamps or coolers. These should be inspected and tightened as needed. If the piston is hitting the valve plate, it will be extremely noisy and should be addressed by removing the cylinder head and checking for dirt or debris on the piston head. An old or worn crankcase may also create excessive noise. Replacing the oil or bearings may solve the problem. If not, the pump should be replaced. Finally, an improperly mounted air compressor will cause a lot of noise and vibration. Tightening mounting bolts or replacing worn vibration pads to ensure that it is properly secured may help.
While it is almost inevitable that an air compressor will experience a breakdown at some point in its lifetime, many of these failures can be avoided with routine inspections and a preventive maintenance program. However, if air compressor failure does occur, this information should help troubleshoot and correct the problem, helping to avoid excessive downtime and expense. For information or assistance with a maintenance program or issue with your air compressor, please contact JHFOSTER.