Understanding VSDs, Inlet Valves and Other Rotary Screw Compressor Parts
Rotary screw air compressors are a mainstay in many industrial facilities as they offer a 100% duty cycle, which means they can run 24/7 without taking a break, unlike piston-powered air compressors that provide intermittent duty cycles. While one might think that a continuous duty cycle results in higher electric bills, the truth is that rotary screw compressors can provide both high-quality air and excellent efficiency, thanks to variable speed drives and other key components.
This blog will explore the operating principle behind rotary screw compressors, as well as the components that allow them to provide a continuous source of high-quality air without sacrificing energy efficiency.
The Versatility of Rotary Screw Compressor Design
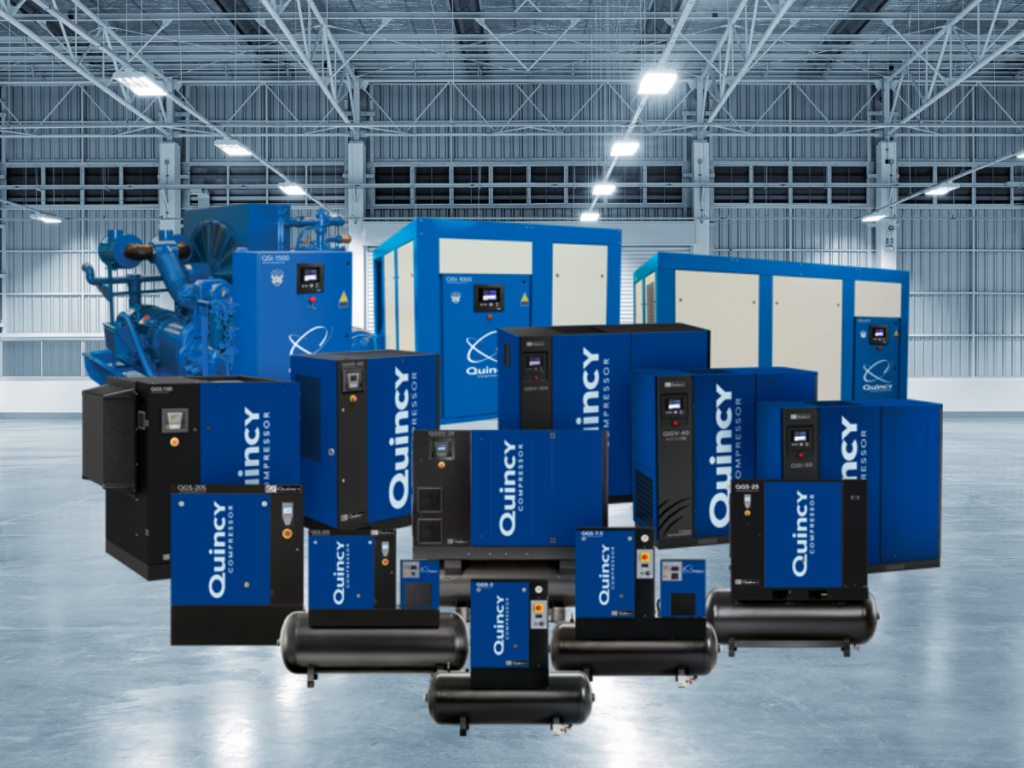
Before discussing the components that contribute toward the efficiency of rotary screw air compressors, it’s important to understand how they work. The design of a rotary screw compressor features two interlocking helical rotors, which mesh closely. Air is brought into the compression chamber through the inlet valve and captured in the space between the rotors. As the rotors rotate, they interlock and compress the trapped air.
This design permits continuous operation, or a 100% duty cycle, making rotary screw compressors suitable for operations that require a constant supply of compressed air.
In addition, rotary screw technology is available in both oil-lubricated and oil-free models, making them versatile for use in just about any industry that requires a continuous air supply, including those that demand the cleanest, highest purity air, such as the food and beverage, medical device, electronics and pharmaceutical manufacturing industries.
Using a Variable Speed Drive Can Improve Efficiency
While the design of rotary screw compressors permits a 100% duty cycle and contributes to its overall efficiency, there have been some developments that further the potential energy savings, including the option of a variable speed drive motor.
In applications that wish to use a rotary screw compressor, but have an air demand that fluctuates, a variable speed drive automatically adjusts the compressor’s operating speed to meet the demand in real time, which can have a great impact on the efficiency of the unit.
This is because a rotary screw air compressor’s flow rate and power consumption are proportional to its speed, so as the demand fluctuates, variable speed drive technology allows the motor to adjust the speed to match the current demand. This means that when the demand is low, the motor will run at a reduced speed, requiring less energy to operate, and when demand for compressed air is higher, the variable speed drive will automatically boost motor speed to meet the higher demand.
In comparison, a rotary screw air compressor with a fixed-speed motor operates at the same speed all the time. Rather than adjusting the motor speed, the fixed-speed air compressor adjusts the air inlet valve depending on the demand, but the motor always operates at the same speed.
In general experts recommend using fixed-speed compressors in operations with a steady air demand and variable speed drives in facilities with a fluctuating air demand.
How the Inlet Valve and Inlet Filters Impact Efficiency
While it is often assumed that the inlet valve doesn’t contribute to the efficiency of a compressor because its main function is to allow ambient air into the compressor’s housing, in a rotary screw compressor, the inlet valve has a significant impact on the unit’s efficiency.
The inlet valve regulates the amount of air that enters the compression chamber – opening fully when it is loading and closing during unloading. So, a fully functional inlet valve is an essential component for efficiency.
In addition to the inlet valve, inlet filters also play a role in the efficiency of the air compression system. If intake air contains moisture, dust or other particles, these contaminants can build up and clog the filter media and make their way to the internal components of the compressor, causing pressure drops that force the compressor to work harder, greatly reducing the efficiency of the system.
For this reason, air inlet filters should always be installed at the intake to prevent the introduction of contaminants that can minimize the efficiency of the system. Maintenance of inlet filters is also crucial to efficiency, so inlet filters should be checked and changed before dirt build up causes pressure drop within the system. Properly maintained inlet filters will also help ensure the quality of the compressed air.
The Role of Pressure Switches on System Efficiency
A pressure switch or sensor for an air compressor is the device that monitors the discharge pressure. When pressure drops below a set point, the pressure sensor signals the compressor controls to start compressing more air and, when the compressor reaches maximum pressure, the sensor signals the controls to reduce output accordingly.
While the main function of the pressure sensor for an air compressor is to avoid over pressurization of the system to ensure safety and prevent damage to the compressor, it also plays a role in the efficiency of the compressor because it ensures that the compressor operates only as necessary, reducing rapid cycling and energy consumption.
As a bonus, the pressure sensor also prevents unnecessary wear and tear on the compressor, extending the lifetime of the unit. In addition, by providing appropriate pressure levels at all times, the pressure sensor helps ensure smooth operation of the tools and equipment that rely on compressed air.
Because they promote safety, efficiency and smooth operation, replacement of malfunctioning pressure sensors is essential.
Oil-lubricated and oil-free rotary screw air compressors are widely used throughout many industries because they provide a reliable and continuous flow of high-quality compressed air. Thanks to their design and components such as variable speed drives, inlet valves, inlet filters and pressure sensors, they are an extremely energy efficient source of compressed air. To determine whether a rotary screw compressor is suitable for your operation, please contact JHFOSTER today.