Understanding the Safety Functions of Collaborative Robots
As the use of collaborative robots continues to expand in industrial workplaces, humans are more frequently sharing space with cobots, as they’ve come to be nicknamed. While collaborative robots are considered “inherently safe” by design, there are understandably concerns regarding the safety of human operators working in close proximity to swift-moving industrial equipment. However, advances in embedded safety technology combined with the development and updating of safety standards, make it possible to achieve safe collaborative environments that enable industrial facilities to take advantage of the benefits offered by cobots.
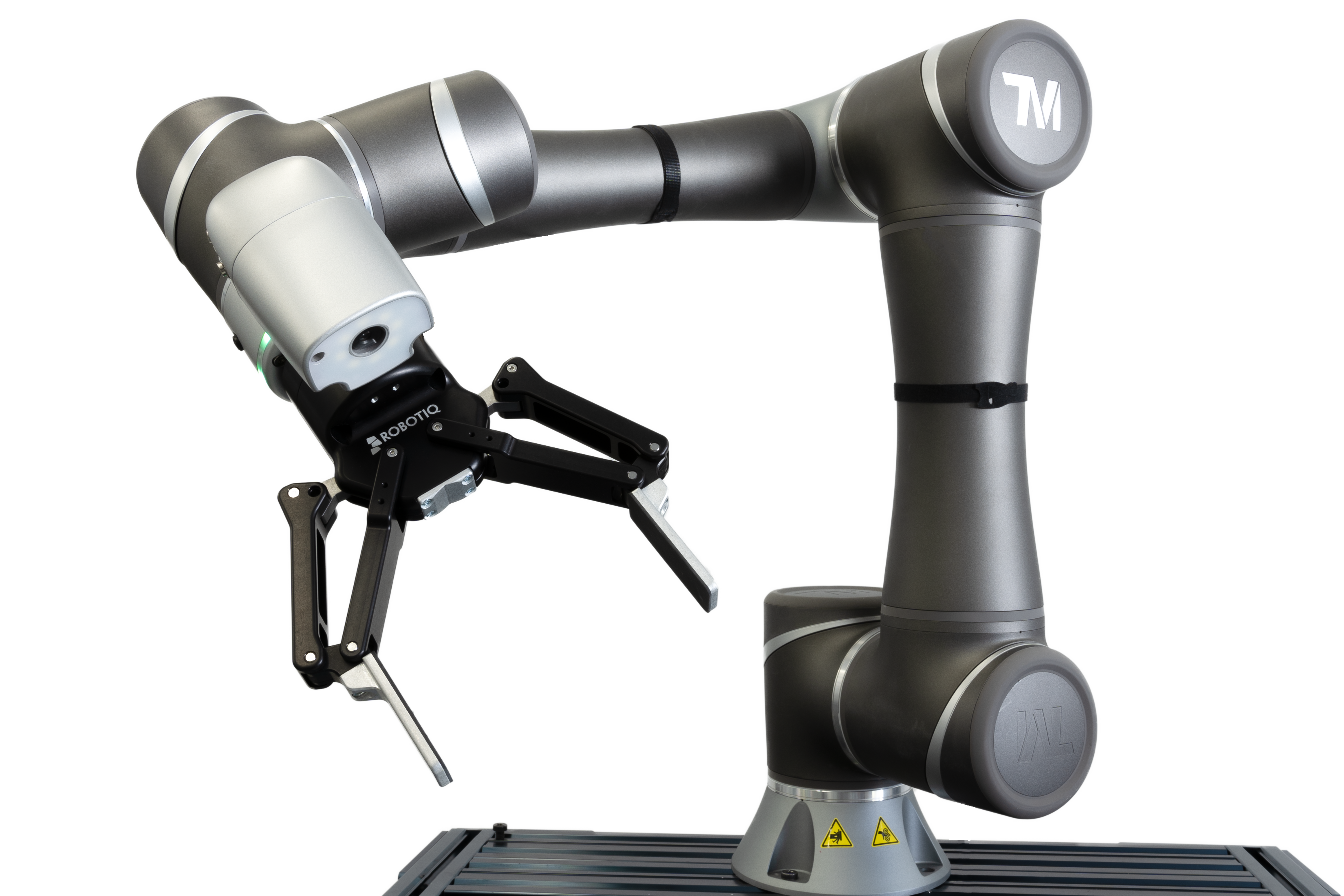
What are the Benefits of Collaborative Robots?
Collaborative robots are designed for integration into workspaces that are shared with human co-workers. Compared to traditional industrial robots, they are easier to program and integrate as they do not require cages or guarding. Cobots often manage routine tasks such as lifting, assembly and inspection, but they perform these jobs with more speed and accuracy than human workers and without growing fatigued. The result is often beneficial and leads to:
- Increased efficiency/productivity: Because they are built for speed and accuracy, cobots can complete tasks faster than human workers and can do so without breaks, which helps to increase productivity and throughput.
- Increased product quality: Cobots are programmed to perform tasks and are often equipped with specialized end effectors and machine vision systems that allow them to perform assembly, inspection and pick-and-place activities precisely and without errors. This precision and repeatability reduces scrap and waste and ensures consistent product quality.
- Increased safety: Since collaborative robots handle tasks that create fatigue or cause repetitive motion injuries in human operators, using cobots often reduces injuries and increases the safety record of the facility.
What Functions Allow Close Proximity between Cobots and Workers?
While the use of collaborative robots can help avoid repetitive motion injuries in employees, there are valid concerns regarding the safe use of cobots in areas where they will be working free from cages and guarding and near human workers as their speed, size and end effectors may cause harm if they come into contact with operators. For this reason, cobots are quickly evolving to include more advanced safety features. As a matter of fact, ISO 10218-1 and 10218-2 standards were developed to help ensure safety in industrial robots and ISO 10218-2 specifies four safety-based functions that allow a robot to be considered safe in a collaborative environment:
- Monitored standstill: Formerly known as safety-rated monitored stop, this collaborative function uses sensors in the safety control system to detect operators and forces the robot to stop if it is too close to human workers. This is generally the preferred method if humans and cobots are working in the same cell or in overlapping tasks, such as a worker loading parts directly onto the end effector.
- Hand-guided controls: This safety method allows the operator to manually control or move the robot for its next task via hand-operated control devices. This is often used to teach the robot to follow paths and motions that it will need to complete the work.
- Speed and separation monitoring: This safety function, also called SSM, allows operators and robots to work in the same area while maintaining a safe distance. If sensors detect that a human worker is too close, a command will be sent that forces the cobot to slow down or stop. Evolving safety sensor technology is making this a common function in today’s cobots.
- Power and force limiting technology: This feature, known as PFL, is designed to control and reduce the robot’s force and torque in order to avoid injury if a cobot accidentally makes contact with an operator. Some cobots have fixed and non-adjustable PFL, while others have adjustable or configurable PFL. In adjustable PFL, if the cobot exceeds preset parameters, it will automatically come to a protective stop.
Ensuring Safety in Collaborative Applications
Thanks to built-in safety functions, it is less likely that a collision will occur and, if it does, the above-mentioned functions were developed to help reduce the severity of injury. However, the inclusion of these safety features does not guarantee that the cobot is safe to use “out of the box.” This is because the collaboration will vary from application to application and facility to facility. For instance, one collaborative robot may work independently away from human operators while inspecting or assembly parts while another cobot may be placed in an environment where it wields a sharp end effector while working at high speeds in close proximity to a human employee and yet another may follow a human worker up and down warehouse aisles in a pick-and-place application.
Obviously, each of these applications has a different level of risk, so to fully ensure the safety of the collaborative robot in a specific scenario, it is necessary to provide a risk assessment for each cobot before placing it on the facility floor. Standards ISO/TS 15066 and RIA/TR 15.606 outline the methodology for assessing risks and recommend that the process evaluates the collaborative workspace, as well as how a human worker will interact with the cobot. Each possible contact situation between an operator and cobot must be considered and the risk assessment should determine the nature and severity of each potential type of contact.
If the assessment reveals that there are hazards despite the built-in safety features, action must be taken to bring potential collisions within allowable ranges and provide any necessary protective measures to fully ensure the safety of human operators around collaborative robots. Performing a thorough risk assessment and implementing any necessary precautions is the only way to fully ensure the safety of operators who share space with cobots.
As more safety features are developed and as the technology behind these features advances, industrial facilities will more than likely continue to add collaborative robots to the automation mix in an effort to increase efficiency, productivity and product quality. However, it’s important to remember that while the cobot has the capability to be safe, it is only safe if it is used in a safe manner. For this reason, it’s important to perform a risk assessment and design for safety at the beginning of the project. When all the risks are considered and avoided through proper design, it helps ensure that cobots and humans can work together without incident.
For more information on collaborative robots and their safety functions, please contact an expert at JHFOSTER.