The Anatomy of Reciprocating Compressors
Air compressors are integral to most facilities where compressed air is used to power pneumatic tools and machinery and may be used directly in the manufacturing of products. Because there are so many different applications and facilities, there are several types of air compressors available to suit various needs. Here we will explore reciprocating compressors, one of the most commonly used types, by taking a deep dive into the anatomy of these manufacturing marvels, with a focus on reciprocating compressor components and how they work together to provide compressed air for industrial facilities.
What are Reciprocating Compressors?
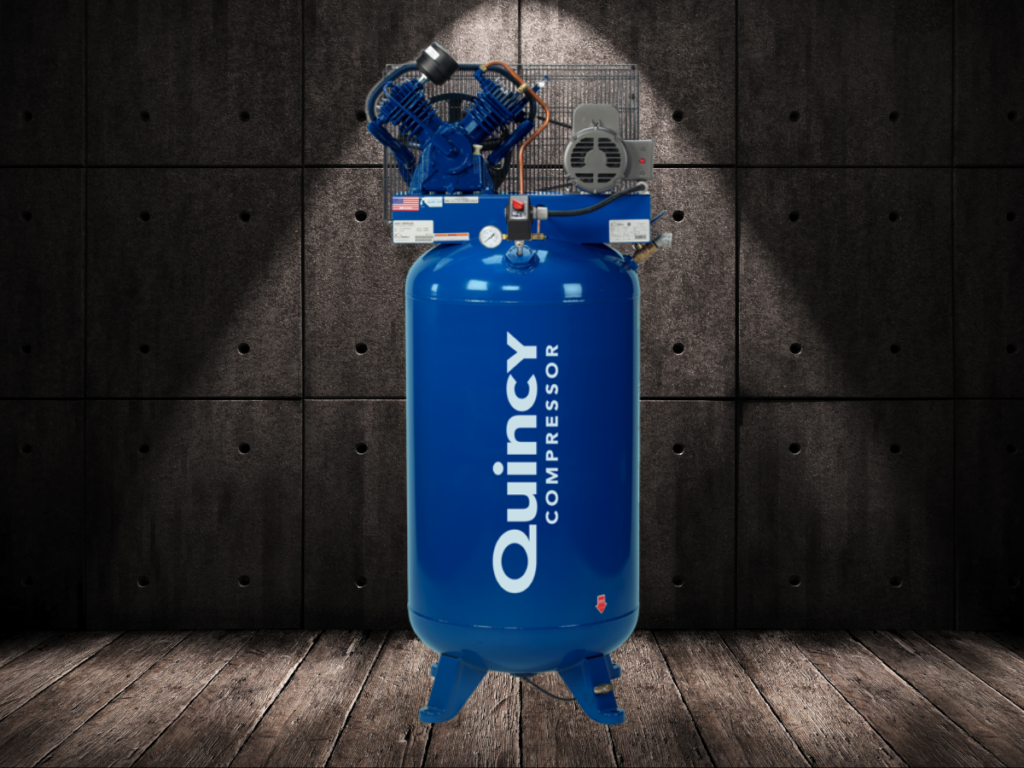
Reciprocating compressors, sometimes called piston compressors, are positive displacement air compressors that provide compressed air to an application. Reciprocating compressors use pistons to compress air. They are well suited for applications that require intermittent air.
Reciprocating compressors are simple in design as there are just a few components involved in the operation, including:
- The piston: The piston is the reciprocating compressor component that compresses the air by moving in a reciprocating, or back and forth, motion inside the cylinder, which is also known as the air compression chamber.
- The cylinder or air compression chamber: As mentioned above, this is the air compressor part where the air is compressed by the piston.
- The crankshaft: This air compressor component is connected to the shaft of an electric motor and transfers rotary motion to the piston to initiate the reciprocating motion used for compression.
- The connection rod: This internal device connects the piston to the crankshaft.
- The suction valve: Air is brought in through the suction valve by the movement of the piston.
- The discharge valve: This valve discharges compressed air into the storage tank of the air compression system.
- The storage tank: This is where compressed air is stored until there is demand.
How Does a Reciprocating Compressor Operate?
Using the air compressor components mentioned above, a reciprocating compressor operates as follows:
The piston moves downward to create a vacuum within the cylinder, drawing air into the cylinder through the intake valve. Then, as the piston moves upward the intake valves closes, the air is trapped in the cylinder and compressed. The discharge valve opens and releases the compressed air into the next stage or storage tank where it is cooled and eventually delivered to the end point of use. This reciprocating process is repeated creating a steady stream of compressed air.
It should be noted that there are two types of reciprocating compressors: single-stage and two stage. In a single-stage reciprocating compressor, the air is compressed in a single stroke, while a two-stage reciprocating compressor compresses the air to an intermediate pressure first and then to a higher pressure during the second stage, providing greater levels of efficiency.
Advantages and Disadvantages of Reciprocating Compressors
Reciprocating compressors have several advantages, but also a few disadvantages.
Pros | reciprocating compressors are most effective when sized to run intermittently, and can produce high pressures of up to 6,000 psi, making them suitable for many industrial applications. They are available in both oil and oil-free models so they may be used in general manufacturing, as well as sanitary applications that require oil-free air, making them versatile. Reciprocating compressors typically have a lower price tag than many other types of air compressor technologies. |
Cons | reciprocating compressors generate a lot of noise during operation. Some reciprocating compressors have a duty cycle of only 50%, which means they will need to be turned off after running to allow the compressor to cool down between cycles. If continuous air is needed, a different type of air compressor with a 100% duty cycle should be selected. In addition, some reciprocating compressors have a lifespan of about 10,000 running hours before they need an overhaul or replacement, so it may not be the best choice in a continuous operation. |
Because an air compressor is a hard-working, essential piece of equipment in a manufacturing facility, selecting the right type is a crucial decision that can impact efficiency. Please contact an expert at JHFOSTER, a Tavoron company, to determine whether a reciprocating compressor, with its simple design and intermittent operation, is the right choice for your application.