Strategies for Running an Efficient Compressed Air System
In industrial facilities, compressed air is a widely used resource because it’s a safe and readily available form of power for operating machine tools, material handling equipment and other pneumatic powered machinery. However, if not properly designed, operated and maintained, it can be a major facility expense as it requires 8 hp of electricity to generate just 1 hp of compressed air.
Although keeping an industrial compressed air system running efficiently can be a challenge, it is possible. Obviously, selecting and installing properly sized equipment is the first step toward efficiency but, short of an equipment overhaul, most facilities are bound to existing compressed air systems, so this article suggests low- or no-cost, every-day operational best practices and maintenance tactics that will help optimize the performance of existing compressed air systems and keep them running in the most efficient manner possible. As a bonus, employing these strategies is likely to improve air quality and prolong the life of the equipment. But perhaps the biggest benefit of running an efficient compressed air system is the potential for significant cost savings.
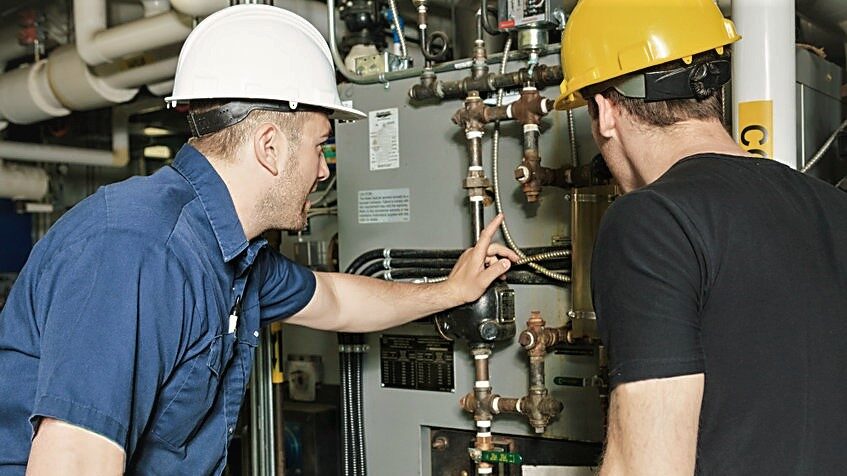
Operational Best Practices
In the daily operation of compressed air systems, it’s easy to overlook some of the biggest energy wasting practices, but performing simple tweaks and incorporating some new habits can go a long way toward boosting efficiency.
Improve air flow | Friction, created as air circulates through the compressed air system, can reduce overall efficiency. Any kinks or sharp bends in the distribution network should be straightened when possible. Properly sized piping is critical and will reduce friction and improve air flow and efficiency vs undersized restrictive piping. The suggested “sweet spot” for distribution point of use hoses is about 3/8 inches in diameter, which will provide adequate air flow for most applications, but still prevent friction. A system with smooth, frictionless air flow will use the same amount of energy; however, getting the compressed air to its destination will not require as much effort, thus increasing efficiency. |
Cooler air takes less energy to compress than warmer air. As a matter of fact, a 5°C decrease in air inlet temperature will lead to a 2% increase in compressor performance. Unfortunately, the heat generated during normal operation will raise the temperature of the area around the compressor, as well as that of the inlet air. For this reason, some compressors are equipped with heat exchangers or heat recovery systems that reuse waste heat and/or refrigerant systems to cool incoming air. If this is not the case with existing equipment, give the compressor a break, open vents or run fans when the surrounding area heats up to reduce temperatures and improve efficiency. | Cool it off |
Improve intake air quality | Providing cool, dry, contaminant-free intake air will increase the efficiency of the system and improve the quality of the air it produces. As discussed above, cooler air requires less energy to compress, so be mindful of the inlet air temperature. The quality of the intake air also affects system efficiency as contaminants create friction, damage system components and impact the quality of outlet air. Additionally, humid air causes corrosion, which is harmful to system components and outlet air quality. Ensure inlet air quality is adequate and outlet air meets application requirements by making sure drains are fully functional, the dryer is in good working order and filters are checked and changed frequently. This will not only boost system efficiency and improve air quality but will also prolong the life of the system. |
It’s not uncommon to operate an air compression system at higher-than-necessary pressures due to differing equipment demands and to compensate for pressure drops; however, reducing the pressure has the potential to lower electrical energy costs. Using pressure regulators at end points can help keep pressure in check. Also, reducing inappropriate usage of compressed air for blowers and other tools will help minimize the load on the compressed air system and reduce pressure drops caused by unauthorized air demands, further increasing efficiency. | Correct the pressure |
Use the controls | Most compressed air systems are equipped with modulating, variable speed and variable displacement controls, which offer more efficiency and flexibility than just turning the compressor on and off. Controls will allow the system to adapt to different airflow requirements, pressure demands, speeds and output in the most efficient manner. If a central control system exists, use it to link all the compressors and dryers and create the best control scheme for delivery of required air output within an optimized pressure band to further boost efficiency. |
Maintenance Strategies
Proper maintenance of a compressed air system will have a positive effect on the system and can greatly impact efficiency. When looking to boost efficiency, pay close attention to the filters and potential leak points.
Filters | Filters are there for a reason! Dust, dirt, grease and other debris can clog filters, creating pressure drop and poor air quality. If filters aren’t maintained, the system will use more energy to provide the required pressure. Filters should be checked on a regular basis and, when it’s time to change them, consider low-pressure drop, long-life filters that are properly sized based on the maximum flow rate of the system. |
Leaks | Leaks are the Achilles’ heel of an air compression system as they waste energy and create drops in system pressure. Areas most likely to leak include open condensate traps, shut-off valves, joints, seals, couplings, hoses, tubes and fittings. An ultrasonic acoustic sensor or the old-school soapy water method can be used to locate leaks. Repairs may include tightening or replacing components, but it is worth the effort since detecting and fixing leaks can save as much as 10% on the average electricity bill. |
While efficiency of a compressed air system can be improved through the design and installation of new, modern equipment, many facilities must work with the system at hand. In those situations, simply incorporating operational best practices and keeping up with maintenance will go a long way toward increasing system efficiency and will likely yield better performance, improved air quality, longer equipment life and reduced costs.
For more information on improving the efficiency of your compressed air system, please contact JHFOSTER.