Robots and Workplace Safety
Industrial facilities can be a dangerous place for employees. In addition to the usual trips, slips and falls, fast-moving equipment and hazardous areas in manufacturing facilities present the potential for accidents and injuries. The use of robots can help improve the safety record of industrial workplaces by filling in for and safeguarding human employees in accident-prone or hazardous locations.
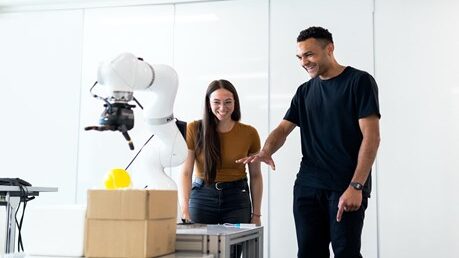
However, because today’s collaborative type robots are designed to work alongside and move among human workers, there is also a need to ensure that personnel remain safe around robotic equipment. This article will explore both the safety benefits of using robots, as well as the necessary precautions that must be taken when humans and robots share space.
How Robots Improve Workplace Safety
Injuries caused by repetitive motion, heavy lifting and contact with dangerous machinery and hazardous locations not only physically harm workers, but they also hurt the employer’s bottom line due to lost labor, medical expenses and worker’s comp claims. Using robots to perform high-risk tasks or to work in hazardous areas can help reduce the likelihood of workplace injuries and reduce accident-related expenses. The following are some examples of how robots can improve safety throughout the facility:
Reduce the risk of MSDs: Musculoskeletal disorders (MSDs) are a common issue in industrial facilities where workers need to perform repetitive motion tasks and heavy lifting. Using robots in pick-and-place, warehousing and similar applications reduces the need for workers to carry, lift or move heavy objects, resulting in fewer back, repetitive-motion and MSD injuries for employees.
Reduce worker fatigue-related injuries: When workers grow tired or become bored from performing mundane activities, they are less likely to pay attention to the task at hand or to their surroundings, which often results in fatigue-related injuries on the manufacturing floor. Robots are pros at handling repetitive tasks with accuracy and they do not fatigue, so their performance does not decline. Swapping robots for humans in these sorts of activities will reduce injuries and free workers to perform other, value-added tasks around the facility.
Eliminate the need to work in hazardous locations: Many manufacturing facilities have areas where fumes, high heat, toxins or other hazards make it dangerous for human workers to perform their duties, even when wearing personal protective equipment. Robots can be used in these locations in place of humans in an effort to avoid serious health complications caused by environmental factors in the workplace.
Limit contact with hazardous machinery: With fast-moving equipment, cutting, welding and other dangerous machinery operating throughout a manufacturing plant, even precautions such as signage and barriers may not be enough to keep operators and maintenance techs out of harm’s way. Robotic and automated safeguarding systems that include limiting and presence-sensing devices and sensors can be used to keep human personnel a safe distance from dangerous machinery or to ensure that the equipment stops if an employee enters the danger zone.
Safety Precautions for Robots
While robots can certainly boost facility safety in the applications discussed above, where humans and robots coexist, there is still a need to evaluate safety programs to ensure that workers remain safe when sharing the workplace with robots, as these automated solutions move at high speeds and forces and may contain cutting tools or sharp edges.
While there are currently no Occupational Safety & Health Administration (OSHA) standards regarding the use of robots in the workplace, the Agency does provide guidance concerning hazard recognition, hazard evaluation and solutions. OSHA recognizes eight primary hazards associated with robots, including:
Impact and collision hazards | Pneumatic hazards |
Crushing and trapping hazards | Slipping, tripping and falling hazards |
Struck-by-projectiles hazards | Environmental hazards |
Electrical hazards |
Additionally OSHA recognizes that many robot-related workplace accidents occur during the assembly, installation, testing, programming and maintenance of robots, so precautions should be taken when performing these activities. For all potential hazards, OSHA suggests that education and training are provided for every employee who works on or near robots.
Noting the lack of standards, the National Institute for Occupational Safety and Health (NIOSH) at the Center for Disease Control and Prevention (CDC) is currently working to monitor and improve robot-related safety through programs that provide scientific research in an effort to guide the development and use of occupational robots that enhance worker safety and health.
Additionally, many robots, especially collaborative robots, which are specially designed to share work cells with and work alongside humans, are equipped with built-in safety features, such as monitored stand still, hand-guided controls, speed and separation monitoring and power-and-force limiting technology. There are also ISO standards that describe how to conduct a hazard assessment for each situation in which a collaborative robot is used in a facility. More detailed information on the safe implementation of collaborative robots can be found here.
While robots can indeed provide workplace safety benefits and reduce worker injuries, they also pose some safety risks of their own. For this reason, it’s important to recognize and address any potential robot-related hazards via a hazard assessment, proper safeguarding and employee training and education. By ensuring that robots are designed, installed and operated in a safe manner, it is possible to not only keep workers out of harm’s way around robots, but to use industrial robotic solutions to enhance the overall safety of the workplace.
For more information on industrial robots, their safety features and how to conduct a safety assessment, please contact a representative at JHFOSTER.