Robot Demonstrations Help During the Selection Process
As industrial facilities struggle to meet throughput demand due to labor shortages and tight budgets that make it nearly impossible to invest in large expansion projects, it is fortunate that robotic automation is becoming more affordable and accessible because robots can help alleviate these challenges. For instance, robots can help increase capacity without expanding lines by reducing troublesome bottlenecks due to their high speeds, precision and efficiency. Robots can also make up for worker shortages because they are able to complete dull, repetitive tasks 24/7, without breaks.
With all the advantages robots bring to the table, it’s no wonder many industries are contemplating robotic automation projects. However, it can be difficult to select the right robot for an application.
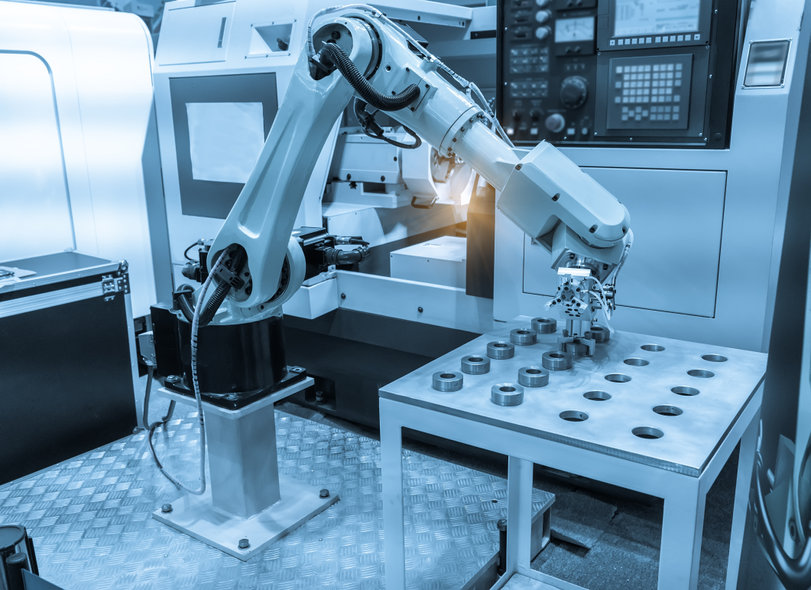
In addition to knowing the various types of robots and the most important selection criteria, working with a reputable, knowledgeable partner can be a huge help during the robot selection process. Not only can a trusted partner assist with finding the right robot for an application, but they likely provide robot demonstrations that showcase the capabilities of the robot under consideration.
This blog will explore robot types, selection criteria and the benefits of a robot demonstration.
What Types of Robots are Available?
Cartesian Robots | Cartesian robots feature three prismatic joints that deliver linear motion by sliding along three perpendicular axes (X, Y and Z). Simple to operate and easy to customize, Cartesian robots are widely used in pick-and-place, loading and unloading and assembly applications. |
SCARA | SCARA (Selective Compliance Assembly Robot Arm) robots feature two parallel joints, allowing lateral motion in one selected plane. SCARA robots offer high speeds and excellent repeatability, making them good choices for assembly, packaging, palletizing and machine loading applications. |
Articulated Robots | Articulated robots feature an arm mounted to a base with a twisting joint and often have a small footprint. Their flexibility makes them suitable for use in packaging, welding, material handling, automotive assembly, steel cutting and machine tending applications. |
Delta Robots | Consisting of parallel joint linkages connected on a common base that is mounted above the workspace, Delta robots can perform delicate and precise motions at high speeds. |
Polar Robots | Polar robots feature an arm with two rotary joints and one linear joint that connect to a base with a twisting joint and provide a spherical work zone. This allows them to sweep around a large area, as well as above or below obstacles, while using very little floor space. Injection molding, material handling, stacking and unstacking, welding and die casting are common applications. |
Collaborative Robots | Collaborative robots are designed for integration into workspaces that are shared with human co-workers. They find use in pick-and-place, palletizing, quality inspection and machine tending applications |
What Characteristics are Most Important?
The best robot for the job is the one that can perform the required task in a way that provides gains in efficiency and productivity, while also complying with budget restrictions and safety requirements. Below are some of the technical considerations when selecting a robot:
- Application Details: The most important consideration is the application – what do you need the robot to do and where will it be placed? It’s important to clarify the task, which means itemizing and considering each step, along with factors such as the distance the robot will need to move or reach and the weight of any objects the robot will have to manipulate.
- Required Reach and Payload: It is essential to know the maximum distance the robot will need to reach to efficiently accomplish the task. Range of motion, expressed in degrees, should also be considered. Payload refers to the maximum load the robot can handle, including both the parts it will be handling and any end-of-arm tooling. Knowing the required reach and payload for the application will help shorten the list of robotic options.
- Flexibility: The number of axes directly relates to the flexibility of the robot. A 4-axis robot will satisfy most requirements; however, more axes will be required in confined spaces where the robot arm needs to twist or move in reverse.
- Running Speed and Travel: The robot’s speed over the required distance is a major factor in how quickly the robot can accomplish the task.
- Repeatability: Repeatability is the ability of the robot to reach the same position each time it completes a routine, so in applications where high accuracy is required (such as assembling electronics), repeatability is an important requirement.
- Space and Footprint: The available size of the area in which the robot will be expected to perform is important during the selection process. Confined areas and obstacles should be considered.
The Importance of Seeing a Robot in Action
While the above-mentioned selection criteria will help narrow the choices for an industrial robot, it’s often helpful to see the selected robot in action. Reputable partners will offer a robot demonstration to give potential customers a very good idea of how the robot operates and what capabilities it offers. Programming demonstrations are also typically available and helpful. Viewing the robot in person allows more informed decision making as it provides a glimpse into the speed, flexibility, footprint and other important characteristics. Witnessing a live demo will also help prospective users become familiar with the programming and safety features and provide an opportunity to discuss specific applications.
For more information on how robotics can improve your process, help selecting the right robot and/or to schedule a robot demonstration, please contact JHFOSTER.