Reduce Waste and Increase Efficiency with Lean Manufacturing Techniques
In today’s highly competitive manufacturing environment, many businesses are considering employing lean manufacturing techniques to reduce waste and operating costs while improving product quality and efficiency. But what is really involved in lean manufacturing, what are the advantages and how is it implemented? This blog will discuss the principles of lean manufacturing systems, the types of waste in manufacturing, implementation strategies and lean manufacturing examples so you can decide if undertaking lean manufacturing process improvements is the right choice for your facility.
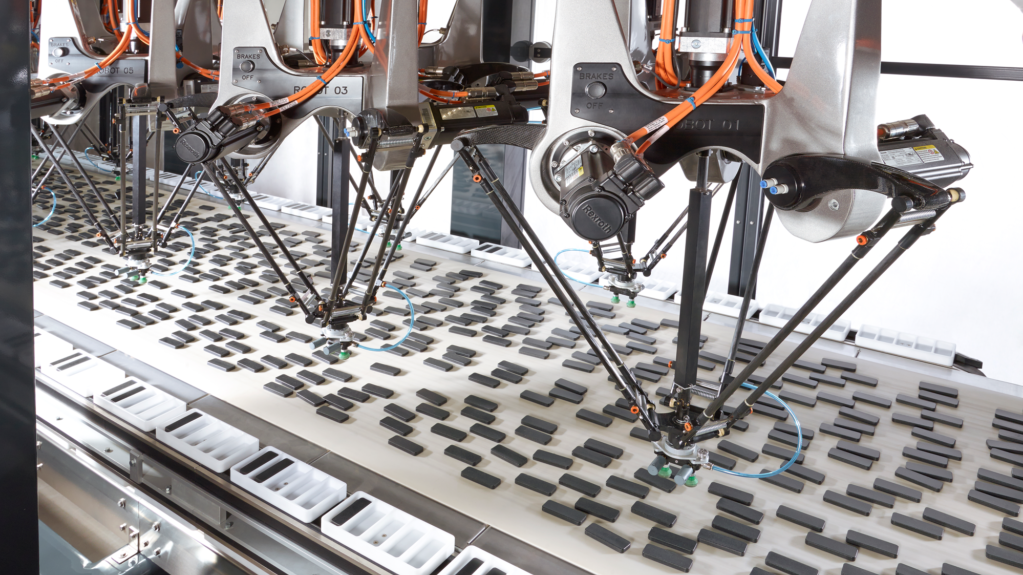
An Overview of Lean Manufacturing Systems
Lean manufacturing aims to eliminate waste, which is defined as any activity that does not add value to the operation, while also continuously improving the process to increase efficiency and product quality. The idea is that streamlining processes and procedures in an effort to minimize waste will naturally enhance productivity.
Waste in industry represents a roadblock to productivity and heavily impacts the bottom line. The types of waste in manufacturing can include anything from idle workers, downtime and bottlenecks, which waste time, to unused materials, excessive inventory and scrapped products, which represent wasted resources and money.
The 8 Wastes of Manufacturing
Specifically, lean manufacturing aims to eliminate eight areas of waste in manufacturing to create lean manufacturing continuous improvement and value within the manufacturing operation. The 8 wastes of lean manufacturing include:
- Unnecessary transportation
- Excess inventory
- Unnecessary movement of people, equipment, and machinery
- Waiting (idle people and idle equipment)
- Overproduction of a product
- Over processing or the addition of unnecessary product features
- Defects that require costly re-work
- Unused talent and ingenuity
By eliminating the 8 wastes of manufacturing from a process, a production facility is likely to find the following benefits:
Minimized waste | Waste negatively impacts the bottom line, the production schedule and resource allocation and provides no value to the manufacturing operation. Eliminating waste will help maximize efficiency of time and resources. |
Improved quality | Minimizing waste by eliminating defects, over-production of a product or unnecessary product features will improve product quality while also streamlining the production process to enhance efficiency and productivity. |
Reducing costs | Overproduction; too much inventory; defective products and resulting re-work; allowing employees or equipment to remain idle; and using unnecessary transportation can cost a manufacturing operation big bucks. Eliminating these will significantly reduce operating costs and enhance profits. |
Maximizing time | Eliminating overproduction will free up equipment and help streamline the process so that employees, equipment and other resources can be used where they contribute the most value to the process. Minimizing defects and rework will also free up more time for value-added production. |
Sustainable practices | Reducing waste and eliminating unnecessary travel and production steps goes a long way toward achieving more sustainable manufacturing processes as it helps to reduce resources, fuel and energy. As an added bonus, it slashes operational expenses. |
Improved customer satisfaction | Streamlining the delivery of higher quality products at a lower cost will enhance customer satisfaction and brand loyalty. |
What are Lean Manufacturing Techniques?
These benefits can be achieved by adhering to lean manufacturing techniques that are based on the five core principles of lean manufacturing, which include:
- Value: Value, according to lean manufacturing philosophy, is defined by the customer and how much they are willing to pay for products that offer desirable features. Manufacturers should seek to eliminate waste, such as time and effort spent adding unwanted or undesirable features to a product, to offset the cost of the product, while also increasing their profits.
- Map the Value Stream: The value stream encompasses the entire product lifecycle from raw materials to production to delivery to disposal. Materials, resources, production processes and transportation should be evaluated to identify areas from which waste can be eliminated, as well as opportunities for lean manufacturing continuous improvement.
- Create Flow: Creating flow by removing barriers to streamlined operations ensures that processes and employees function efficiently at all times, which will improve lead times and minimize waste.
- Establish a Pull System: A pull system involves beginning work only when there is demand for the product. This helps to eliminate waste such as over production, unnecessary inventory, unnecessary transportation and wasted resources. An effective pull system relies on strong communication and efficient, streamlined processes.
- Perfection: Lean manufacturing process improvement is not a one and done deal. Rather, lean manufacturing relies on constant evaluation of processes and resources to continually eliminate waste and streamline operations. In lean manufacturing, continuous improvement is necessary.
While it sounds very promising, many manufacturers don’t know where to start with lean manufacturing. One way is to focus on improving the efficiency of operations, which, in turn, helps eliminate waste. Another method is to focus on identifying and eliminating waste, which can reduce costs and foster more efficient production. Using either focus, there are several lean manufacturing techniques that can be employed to achieve improvement, including:
- Implementing automation to increase efficiency and eliminate time-consuming manual labor
- Focusing on continuous improvement of production practices and quality
- Being flexible and agile enough through automation technologies to allow efficient pull system production
- Aiming for perfection via automation to minimize wasted resources, defective products and time-consuming re-work
- Improving and automating process flows to eliminate bottlenecks and downtime, while also improving product quality by minimizing defects to reduce waste.
Lean Manufacturing Examples
Not every manufacturer can follow the example of Toyota, which is known for its relentless pursuit of lean manufacturing techniques, a practice which they have dubbed “Toyota Production System,” or TPS, which focuses heavily on “automation with a human touch” and just-in-time or pull manufacturing. You can read more about Toyota’s principles here: https://global.toyota/en/company/vision-and-philosophy/production-system/
However, there are some lean manufacturing examples that showcase how lean manufacturing techniques can be applied to tackle a specific problem. The American Society of Mechanical Engineers (ASME) offers several excellent lean manufacturing examples, here: https://www.asme.org/topics-resources/content/7-examples-of-lean-manufacturing-in-action.
One notable lean manufacturing example presented by ASME involves an automotive manufacturer that was losing significant production time during shift changes. The company had three shift changes each day that each averaged 30 minutes, costing the company 1.5 hours in lost productivity every day. A lean manufacturing expert was hired to work with teams across all three shifts to develop new changeover procedures that not only reduced downtime, but also allowed time for maintenance of the equipment prior to the next shift so they could begin work immediately. The resulting lean manufacturing system resulted in 1.5 hours of added production and increased throughput by more than $1 million annually.
Simple lean manufacturing techniques such as this, even when focused on just one problem area at a time, can go a long way toward eliminating wasted time and resources and increasing productivity, quality and profits. To learn more about how automation can help achieve lean manufacturing goals, please contact JHFOSTER today.