Proper Machine Safeguards Prevent Injury & Save Money
Industrial presses, cutting and power tools and machines with rotating or fast-moving parts are accidents waiting to happen, yet a lack of proper machine guarding is one of the most cited Occupational Safety and Health Administration (OSHA) violations each year. Safety precautions may be one of the best investments for an industrial facility, as they protect employees from injuries and save facility owners money on lost labor, insurance and worker’s comp claims, as well as OSHA penalties. However, selecting appropriate safety equipment can be a challenge. This article explores the necessary considerations, making it easier to protect the most important assets in the plant – the workers.
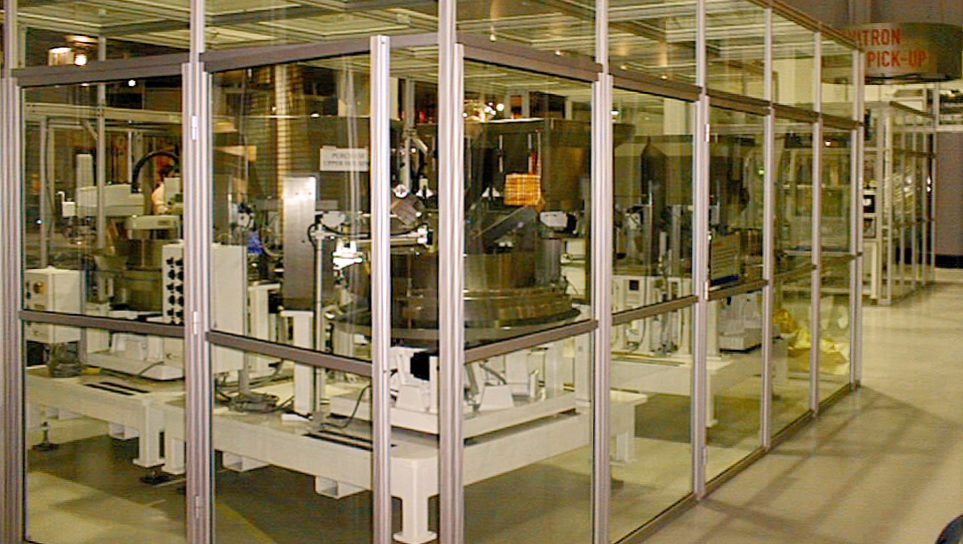
The Hazards
Industrial facilities can be a dangerous place for employees who perform high-risk activities on metal cutting, welding, rotating, milling, material handling and other fast-moving equipment. When not handled correctly or left unguarded, industrial machinery poses risks including skin abrasions, burns, cuts, punctures, amputation and potentially death. Dangerous mechanical motions and actions commonly found in industrial workplaces include:
- Hazardous motions, such as rotating machine parts, reciprocating motions (up and down and sliding motions) and transverse motions (where materials move in a continuous line such as material handling or assembly lines).
- Points of operation, including areas where machines cut, shape, bore or bend materials being manufactured.
- Pinch points and shear points, such as areas where body parts or clothing may be snagged between a moving part and a stationary object, including flywheels, pulleys, belts, conveyor belts, chains, spindles, cams, gears, transmission apparatuses or other machine components.
Other safety concerns include flying debris or splinters, as well as splashes, sprays and sparks that may injure employees working in the vicinity of industrial machinery.
Methods of Safeguarding
While it may seem like almost every area of the facility is fraught with danger, many workplace injuries can be avoided with properly selected and installed safety equipment and machine guards. According to OSHA standards, there are three main categories of physical machine safeguards, including guards, devices and automated feeding and ejection mechanisms.
Guards | Devices | Automated Feeding |
These are barriers that prevent access to dangerous areas or machine points. Common types include fixed guards, which are permanent parts of the machine; interlocked guards, which automatically cut off power through a tripping mechanism when a machine is opened; and adjustable guards, which are designed to accommodate various sizes of stock. | Safety devices may stop a machine if a body part or object is placed in a danger zone. They may restrain the body part from the area, may require the use of both hands on a control in an effort to keep hands out of the danger zone or provide a barrier that is synchronized with the operating cycle to prevent entry when the machine is running. Presence-sensing devices, electro-mechanical sensing devices, pullback devices, safety-trip controls, two-hand controls and two-hand trips fall into this category. | Automated Feeding and ejection mechanisms are used to eliminate operator exposure at the point of operation while feeding materials into equipment. |
Also recognized within OSHA’s machine guarding standard are machine location and distance, which remove hazards from the work area, and miscellaneous aids such as shields that contain flying debris or awareness barriers that warn about dangers.
Selecting Effective Machine Guards
When selecting machine guards, it is important that they are well designed for the purpose and installed properly. They must be made of material that is substantial enough to withstand impact, prolonged use and the environment in which they are installed. Devices should be purchased from a reliable supplier and may be incorporated into a control enclosure by a licensed professional familiar with the control system and enclosure type. They should also be certified for the area in which they are being used since they may be electrical.
In addition, to ensure that the selected guard provides adequate protection, OSHA requires equipment that:
- Prevents contact: Effective guards provide a physical barrier that keeps body parts and clothing away from the hazards.
- Is secure: Machine guards must not be bypassed, removed or tampered with, so they should be attached to the machine and should not be easily removed. Devices may be installed in a control enclosure, if appropriate.
- Protects from falling objects: Falling objects can compromise safe operation of machinery and injure workers.
- Creates no new hazards: Edges of safeguards should be rolled or bolted to eliminate sharp or jagged edges and unfinished surfaces that could create their own injuries.
- Does not interfere with operation: If a guard prevents workers from operating equipment efficiently or comfortably, there is a strong likelihood it will be bypassed. Properly selected and installed safeguarding allows workers to perform tasks without interference.
- Allows safe lubrication: Techs should be able to lubricate machinery without removing machine guards.
Determining Where to Apply Safety Equipment
The best safeguards are ones that not only adequately protect employees from injury, but also allow the highest level of productivity from the machine.
While OSHA suggests the first line of defense is to eliminate the hazard from the employee work zone, this approach is not always feasible. The next option is to determine the necessary level of protection and safeguard the hazard in a way that prevents any part of the body from entering the hazardous area or point of operation. OSHA-recognized methods of protection include proven concepts and designs such as distance, barriers, interlocked guards, presence-sensing devices, enclosures or various combinations of these methods.
The third step includes a risk assessment and evaluation of each potential hazard to verify the level of safeguard needed. For each hazard, a risk assessment must consider the severity of the foreseeable injuries and the probability of their occurrence during all phases of operation for both operators and maintenance staff. Consider the probability of injury, the severity of injury and the frequency of exposure. Safeguards that will prevent these injuries should be selected.
Once the risk assessment for each potential hazard has been completed and the guards or devices have been installed, it’s important to provide necessary training and ensure that all mechanisms are correctly installed and in working order.
The Benefits of Safety Equipment
Not only do safeguards prevent injury, but they can help improve productivity because workers know they are not at risk for injury so can freely complete their tasks. Proper safeguards also reduce expenses associated with OSHA fines, labor losses, injuries, lawsuits, insurance claims and medical expenses.
For more details on selecting appropriate machine guards, devices and other safety equipment, please contact a JHFOSTER expert.