Pneumatic Valves Provide Cost-Effective Benefits
Pneumatic systems are used in industrial applications to power tools and processes and as a power transmission method to move parts and tooling within industrial machinery. Many different components are used to control the rate, pressure and amount of air that moves through these pneumatic systems and pneumatic valves are one of the most vital parts. Not only are they ideal for controlling the air source and regulating the flow in pneumatic systems, but pneumatic valves provide many benefits, including cost efficiency.
What is a Pneumatic Valve?
Pneumatic systems rely on air pressure to function with compressed air serving as the medium used to transfer energy to the different endpoints in a pneumatic system. Pneumatic valves play a crucial role in these systems because they control how much air and in what direction it passes through the system, allowing them to serve as both a control valve and a safety valve that will relieve pressure and/or discontinue the airflow in dangerous situations.
Within a pneumatic system, pneumatic valves may serve as a switch that holds off the compressed air and/or regulates the flow of compressed air to avoid air backlash and leakage. They may also control the amount of compressed air and allow the required volume of air to pass. And, when serving as a directional control valve, pneumatic control valves control the air that is conveyed into the actuator, enabling the cylinder to move.
Because there are a myriad of ways pneumatic valves may be used within a pneumatic system, there are different types available, including:
- Spring-offset pneumatic valves: Some pneumatic valves feature a spring mechanism that opens or closes the ports. The springs often function to return the valve to its previous position.
- Two-, three- and four-way directional control valves: These pneumatic valves are classified based on the number of ports they offer. Each port serves a purpose such as an intake, exhaust, or as a connection to an actuator.
- Open- or closed-resting state valves: Pneumatic valves with open and closed functions are used to regulate the airflow by restricting it. When closed, they will not allow any airflow to pass through.
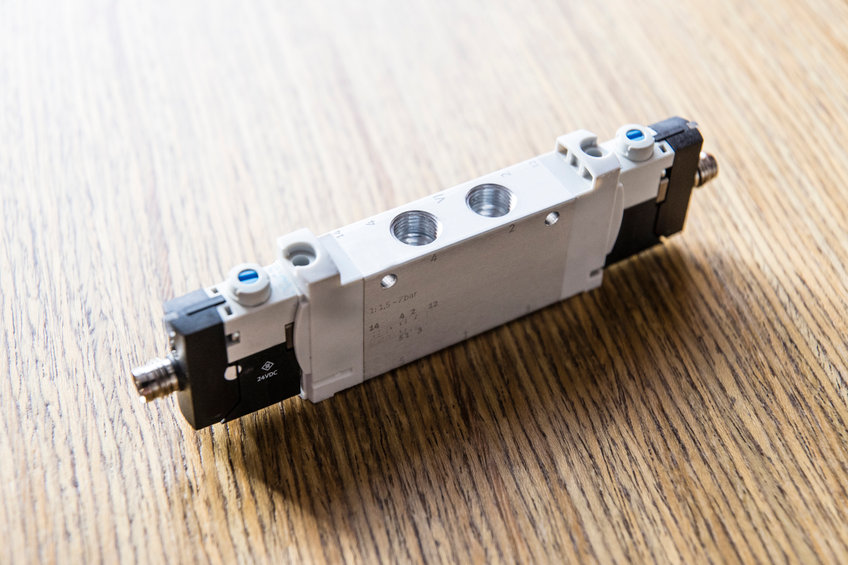
Why Use Pneumatic Valves?
Pneumatic valves are widely used throughout manufacturing, packaging, automotive assembly, food and beverage, pharmaceutical and other industries because they offer cost-effective, reliable and safe operation.
Pneumatic valves are relatively inexpensive when compared to other valve types, making them a very cost-effective option upfront; however, many of their features lend themselves to reliability and safety, which often results in additional benefits to the bottom line.
For example, pneumatic valves offer simple, but robust construction from high-quality materials such as aluminum, stainless steel and carbon steel and have few moving parts. These features allow pneumatic valves to reliably operate in dirty and harsh industrial environments. In addition, pneumatic valves open and close without major impact or wear and tear as tends to occur with mechanically actuated valves. This robustness allows pneumatic valves to function in applications where other valve types would be subject to failure and frequent repair and replacement. The reliability of pneumatic valves can lead to significant savings of time and money in repair, replacement and labor costs. In addition, the reliable operation of pneumatic valves means there is less frequent downtime, resulting in increased productivity.
Why Use Pneumatic Operated Valves?
Increased safety is an advantage associated with pneumatic operated valves. Since they operate via air pressure, not electricity, there is a reduced risk of sparks or fires when using pneumatic operated valves in locations or applications that are flammable, hazardous or high-risk. Further, because they are not electrically operated and there is very little risk of spark or ignition when using pneumatic valves, there is often no need to purchase equipment that protects against explosions, reducing costs while promoting safety.
Pneumatic operated valves can also be used in applications where other valve types may not be suitable. For example, because they are air-operated, pneumatic operated valves can be used in applications and environments with elevated temperatures without overheating, as is an issue with electrically operated valves. And many industrial and manufacturing processes require precision movement and flow direction of hazardous fluids and chemicals. Strong and powerful systems with the ability to safely handle heavy payloads are required for these applications. Pneumatic valves allow these systems to maintain precise movement even in intricate pipe networks and hazardous conditions in a cost-efficient way. Additionally, the lack of a motor means that pneumatic operated valves tend to be more compact than competing valve types, making them ideal in applications and systems where space is at a premium, ultimately reducing expenses and allowing a smaller system footprint.
There are many advantages to using pneumatic valves and pneumatic operated valves, including increased safety and reliability. The low maintenance requirements and ability to function for prolonged periods without failure, often result in benefits to the bottom line and increased productivity. The compact size, strength, and precision of pneumatic valves combined with the increased uptime and safety allow them to be used in many industrial applications at a lower cost than other valve types.
For more information on how pneumatic valves can enhance your application in a cost-effective way, please contact a representative at JHFOSTER.