What Are Pneumatic Actuators Used For? Types, Applications & Uses
By Vitor Rangel, Product Marketing Specialist, Actuators, from Emerson
Pneumatic actuators, in some cases referred to as pneumatic cylinders, can be found in automated systems and machinery in every industry and come in a wide range of sizes, styles and designs. Easy to maintain, these components can operate at high speeds, offering tremendous flexibility and value for a seemingly endless number of applications.
In addition to being fast, economical and reliable, pneumatic actuators are also cleaner and safer than other solutions, which make them ideal for manufacturing, packaging, palletizing, material handling, food and beverage and many more applications. (We’ll cover a few of these applications in a future blog post.)
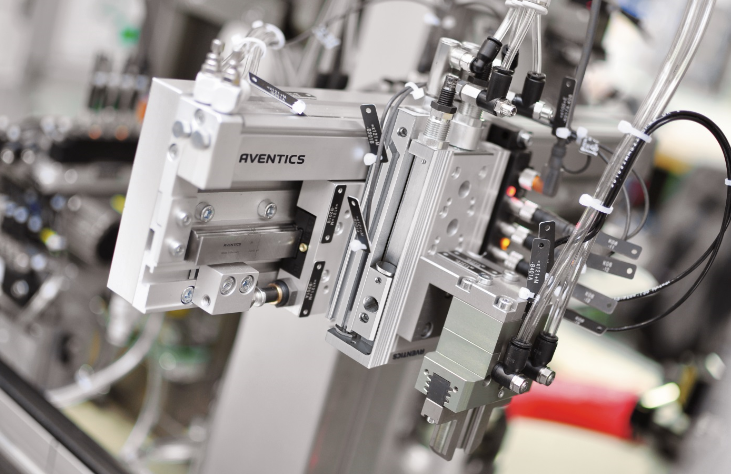
This multi-axis system is built with Emerson’s AVENTICSTM pneumatic actuators. Emerson’s proven portfolio features cylinders and actuators for every application.
To better understand exactly what pneumatic actuators are used for, let’s start with what they do. In the most basic terms, pneumatic actuators are devices that use compressed air to power motion. That motion can be along a rotational or linear path, ultimately assisting or performing a task such as pushing, pulling, gripping, turning, feeding, ejecting, opening, closing, holding, stopping, clamping, stamping and, as you can guess, the list goes on. The forces that these actuators can produce depend primarily on the cylinder bore size (piston diameter) and the operating pressure, but rod size is also a very important consideration on rod-style cylinders.
Types of Pneumatic Actuators
To meet such a wide range of applications and industries, the variety of pneumatic actuators available is comprehensive and versatile. They range from extremely compact actuators used for small handling applications to large actuators for the most powerful jobs as well as rodless designs that provide stroke lengths like conventional cylinders in a much smaller footprint. Each actuator type and its variations offer a unique set of characteristics and advantages based on the applications it serves. Let’s take a closer look at some of the most common types:
Profile and tie-rod cylinders are proven, universal solutionsthat provide precision and regulated force even in applications with high force requirements and long stroke lengths. Sturdy, reliable and highly configurable, they are frequently used in general automation applications, and, they come in numerous designs to meet a wide range of applications, needs and budgets. Available in aluminum, steel and stainless-steel constructions, these cylinders are typically manufactured to NFPA and ISO dimensional standards to simplify installation and worldwide interchangeability.
From left to right: AVENTICSTM Series PRA (profile) and TRB (tie rod) ISO 15552 Pneumatic Cylinders, AVENTICSTM SeriesTM5 TaskMasterTM, A and PPT NFPA Pneumatic Cylinders, all from Emerson.
Mini and round body cylinders come in a wide range of sizes, strengths and properties, which make them excellent solutions for many different applications. They are lightweight, highly customizable, affordable and provide infinitely adjustable force control, making them ideal for small handling and food industry applications. Primarily not repairable, these cylinders will typically have aluminum or polymer end caps crimped to a stainless-steel tube, which makes them an attractive, popular and cost-effective solution for basic pushing and positioning applications. Some models feature an all-stainless-steel construction to withstand caustic or corrosive environments. Hygienic designs with clean and smooth surfaces are also available to prevent accumulation of dirt or bacteria in applications with strict cleanliness requirements.
The compact, robust design of the AVENTICSTM Series MNI mini cylinder from Emerson offers lasting durability in a small footprint.
Short stroke and compact cylinders are shorter than standard pneumatic cylinders by up to 50% or 60% but provide the same concentrated power, precision and reliability. Their size allows them to fit perfectly in practically any machine environment where installation space is limited, making them great for manufacturing, packaging, palletizing, semiconductor and robotics applications. They are easy to mount and available in single- and double-acting models as well as nonrotating versions.
Rodless cylinders don’t have a piston rod, which eliminates the risk of rod-bending or buckling when compared to conventional cylinders. They offer high functionality and drive force in a small amount of space and come in a wide range of sizes and designs, making them fundamental for automated handling technology. Many rodless cylinders incorporate load guidance features such as slide bearings inside the cylinder or external rails with runner blocks to bear heavy loads with high repetitive precision. Emerson’s AVENTICSTM RTC Series features an oval-shaped piston that provides great resistance to side loads and a low overall height design. Common applications range from material flow to door openers and from cutting and drive processes to material handling applications involving light to heavy loads.
In addition to the pneumatic actuators mentioned above, there are also specialized pneumatic actuators like bellows (air springs), grippers, knife gate cylinders, rack-and-pinion rotary actuators, screw-in cylinders, flexible diaphragm cylinders and numerous others.
Bellows are a type of rodless actuator that provide high forces in small installation spaces and are incredibly low maintenance when compared to conventional cylinders as they do not require mechanically moving parts. Convoluted versions are the most popular variant and feature a corrugated natural rubber body making the product ideal for vibration, shock and noise isolation applications although they can also be used for tensioning, lifting and pressing.
Grippers offer parallel or angular motion and are commonly used for workholding, pick-and-place and robotic arm applications.
Knife gate cylinders are specifically designed to automate knife gate valves commonly found in mining and mineral processing, power, pulp and paper, wastewater and chemical industries.
Rack-and-pinion rotary actuators consist of a piston and rack that move linearly and cause a pinion gear and output shaft to rotate. They are commonly used to open and close valves or dampers and provide high torque and adjustable rotation angles.
Screw-in cylinders are primarily used for tensioning and positioning of small components and, because of their threaded design, can be installed directly into working environments without taking up space.
Flexible diaphragm cylinders are virtually frictionless and can be actuated at low pressure to provide precise balancing of forces, especially in finely tuned systems.
With so many types of pneumatic actuators and options to choose from, it can seem daunting to find the right product for your application. While there are many factors to take into consideration, online tools like Emerson’s AVENTICS CylinderFinder aim to simplify the selection of an actuator based on application parameters and desired product features.
For more information about what pneumatic actuators are used for and to find the right one for your application, visit www.emerson.com/aventics.