Machine Risk Assessments Boost Manufacturing Safety
Manufacturing facilities can be busy and dangerous places with fast-moving equipment, vehicles and people at every turn. Safeguarding employees, as well as the assets and equipment, should be the highest priority in industrial settings. Fortunately, a thorough machine risk assessment, conducted by an experienced safety management service professional, can boost manufacturing safety by exposing potential hazards and recommending safety improvements that help prevent accidents and injuries.
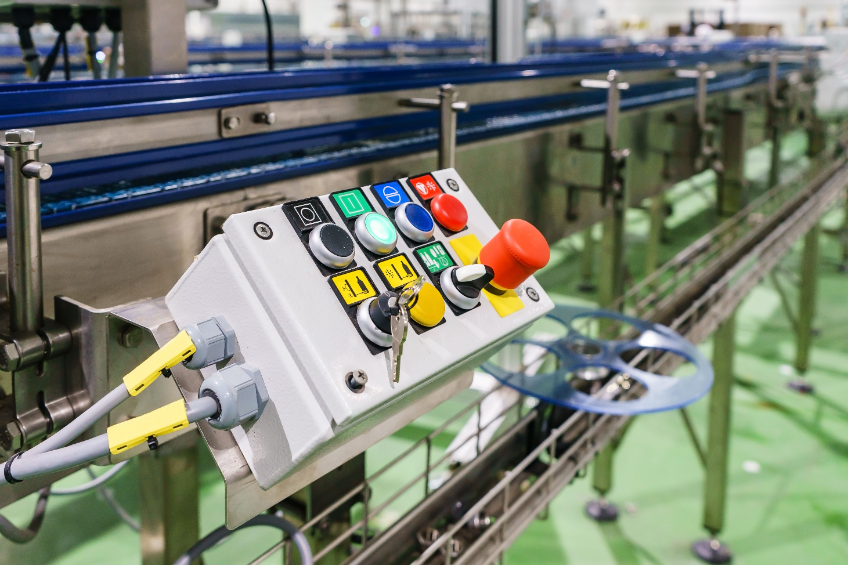
What is a Machine Risk Assessment?
A machine risk assessment is a valuable tool when it comes to ensuring manufacturing safety. Machine, or manufacturing risk assessments, take an in-depth look at the current state of a machine or process and develop mitigation recommendations to reduce risks to an acceptable level, according to the experts at ROSS Controls, a leader in fluid power safety and provider of safety management services.
Machine risk assessments are typically conducted by a machine safety expert who works in conjunction with facility engineers, operators and maintenance staff to analyze machinery, machine modes and tasks for those modes and evaluate them for potential hazards, such as moving parts, electrical risks, exposures and ergonomic stressors, that may compromise safety within the facility. Additionally, machine guarding and safety systems will be examined to identify current gaps, as well as safety function performance levels.
In greater detail, the steps of a manufacturing risk assessment include:
Risk Reduction Plan
After the evaluation, a risk reduction report will be generated. The provided report should detail the machine risk assessment findings and include a risk reduction plan that offers proactive risk mitigation strategies, such as machine guarding and other safety equipment, that should be implemented to minimize or prevent dangerous situations.
Risk Reduction Activities
Suggested corrective actions from the risk reduction plan should be instituted. These may include the installation of manufacturing safety equipment, engineering controls, administrative controls and the use of personal protective equipment. These activities should be implemented according to priority level. Following risk mitigation strategy implementation, effectiveness should be evaluated and documented.
Periodic Review
Reassessment of risk should be conducted on a regular basis to ensure that safety equipment and practices are still in place and functional or that changes in machinery or processes have not resulted in additional or new risks.
Preparation
The boundaries and objectives of the machine risk assessment, including specific machines, processes and tasks, should be identified. A team that consists of experts in safety, maintenance and operations, as well as the safety management service provider, should be assembled.
Hazard Identification
A systematic inspection of machinery should be conducted during a machine risk assessment to expose potential safety hazards, such as unguarded moving parts, unidentified electrical dangers or ergonomic risks. Each hazard and the potential for damage should be noted.
Risk Categorization
The likelihood and severity of each hazard should be assessed, rated and categorized based on potential impact. Regulatory requirements should also be considered to ensure compliance. Categorizing risks as low, medium or high priorities is suggested, so they can be addressed accordingly.
What are the Benefits of a Machine Risk Assessment?
Maximizing manufacturing safety and well-being of employees is the number one benefit of conducting a machine risk assessment, installing manufacturing safety equipment and implementing suggested practices.
However, there are additional benefits associated with machine risk assessments, including:
- Asset Protection: Employees aren’t the only ones who suffer when machinery-related accidents occur. Machinery is often damaged and/or taken out of commission in the wake of a safety incident. Repairing or replacing equipment following an accident can be expensive. By exposing and preventing potential hazards during a machine risk assessment, you are protecting employees, as well as equipment-related assets.
- Reduced costs: Practicing manufacturing safety not only keeps employees healthy, but also reduces the expenses associated with injuries, such as the cost of medical bills, paid sick leave, insurance premiums and regulatory fines. In addition, by preventing damage to machinery, maintenance and downtime costs will also be minimized.
- Enhanced compliance: Conducting regular machine risk assessments helps your company remain in compliance with relevant safety regulations. Not only does this help avoid costly penalties, but it shows a commitment to safety, corporate responsibility and the health and well-being of employees.
- Increased efficiency: Conducting a machine risk assessment helps keep workers and equipment available and operating effectively, which results in increased efficiency, uptime and throughput.
Practicing manufacturing safety is not only a way to protect employees, equipment and assets, but it is also an effective way to reduce costs, increase machine uptime and labor availability, while remaining in compliance with regulatory agencies. To learn more about machine risk assessments conducted by the experts at ROSS Controls or to mitigate safety hazards with the addition of safety equipment, such as machine guards, light curtains, safety switches and other safety controls, please contact JHFOSTER, a Tavoron company who partners with Ross Controls as a safety equipment supplier and experienced representative of multiple safety equipment manufacturers.