Injection Molding Techniques Call for Flexible Parts Feeding Systems
Traditional injection molding typically involves the use of volumetric and gravimetric feeders that precisely measure raw plastic granules, powders or pellets into the process. However, newer injection molding techniques – over molding and insert molding – call for an additional feeding system, an automated and flexible feeding system that can efficiently and accurately pick and orient parts and then place them on a feeding tray in preparation for the over molding or insert molding process.
Over Molding and Insert Molding Explained
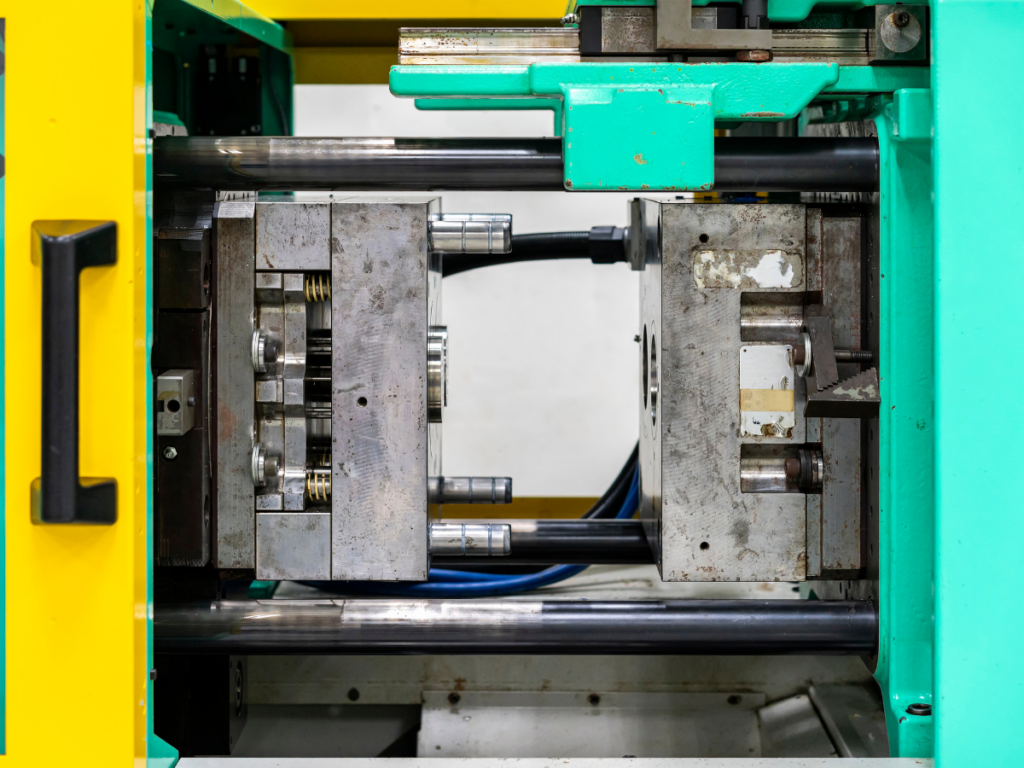
Over molding and insert molding are processes where injection molding occurs over another part or component. In this injection molding technique, the component, called the substrate, is placed into a mold and then molten plastic is injected into the mold so that it surrounds or attaches to the substrate. The result is a single, but complex injection molded part that is actually composed of two components – the substrate and the plastic on top of it.
The main difference between over molding and insert molding is the material from which the substrate is composed. While over molding is usually used to inject rubber over a rigid plastic substrate or rigid plastic over a rigid plastic substrate, insert molding is performed over a metal substrate, such as rubber over a metal substrate or rigid plastic over a metal substrate. For example, over molding might be used to create products such as plastic toothbrushes with rubber grips on the handle, while insert molding might be used to apply rubberized grips to metal tools.
Injection molders employ over molding and insert molding techniques when they need to create a molded part that consists of more than one component or material. It is an inexpensive method of creating a sturdy multi-component part. The techniques provide a more cost effective and efficient method of assembling two separate pieces made from different materials and, in many cases, the methods allow injection molders to mass produce designs that would be too time consuming or difficult to assemble manually.
Flexible Feeders Bring Efficiency to New Techniques
While over molding and insert molding can more efficiently mass produce parts made of two different materials or components, to eek even more productivity out of the process it does necessitate the use of a parts feeding system that is capable of accurately picking and orienting the substrate on a staging fixture in preparation for the injection molding technique. And, for the greatest performance, the feeding system should be integrated with another robot that can then pick the substrate from the staging area and place it into the mold for the over molding or insert molding process.
An automated flexible feeding system that consists of a feeder, a vision system and a robot is the ideal solution. When the automated flexible feeding system is in operation, the substrates can be dropped onto the feeder surface where a robot equipped with a vision system identifies the components, or substrates, that are properly oriented and then uses pick-and-place functionality to grab and supply them to the staging fixture with accuracy, consistency and efficiency.
The Automated Flexible Feeding System (AFFS) from DevLinks excels at performing these functions. The AFFS includes a flexible feeder bowl, an integrated vision system and a robot, which work together to easily align and feed components, regardless of their shape, making it suitable for use with over molding and insert molding processes. Using this automated system, metal or plastic substrates can be dropped onto a rotating disc where they are oriented and aligned for robotic pick and place. The system is compatible with most parts, even silicone, and multiple programs can be loaded to the system to permit simplified switching between parts.
Pairing seamlessly with FANUC robots, the AFFS can feed multiple types of parts – both metal and plastic in a variety of shapes and sizes on the same feeder – saving injection molders from having to purchase multiple feeding systems to handle different substrate materials, sizes or shapes, while providing high speeds and efficiency to the task of sorting through and properly orienting the substrates for the next step in the process. Taking it further, the experts at DevLinks have the experience to integrate the AFFS with an additional robot that will perform the task of picking up the properly oriented substrates from the rotating disk or staging area and placing them into the molds where the over molding or insert molding process will take place.
Over molding and insert molding provide injection molders with a more efficient method of mass producing stronger, sturdier multi-component parts composed of two different materials. However, to gain the greatest performance from the over molding and insert molding processes, an automated flexible feeder system is key. To learn more about how the DevLinks AFFS can provide higher levels of speed, flexibility and productivity to your injection molding process, please contact DevLinks, a JHFOSTER company.