How to Size Compressed Air Piping
The compressed air piping system has a direct impact on the overall performance and efficiency of an industrial air compression system, making proper sizing of air compressor lines especially critical in system design and operation. Inaccurate compressed air pipe sizing will result in inefficient – and expensive – delivery of the air from the compressor to the point of use. This article will provide information on how to size compressed air piping to ensure adequate airflow for industrial applications.
Why Compressed Air Pipe Size Matters
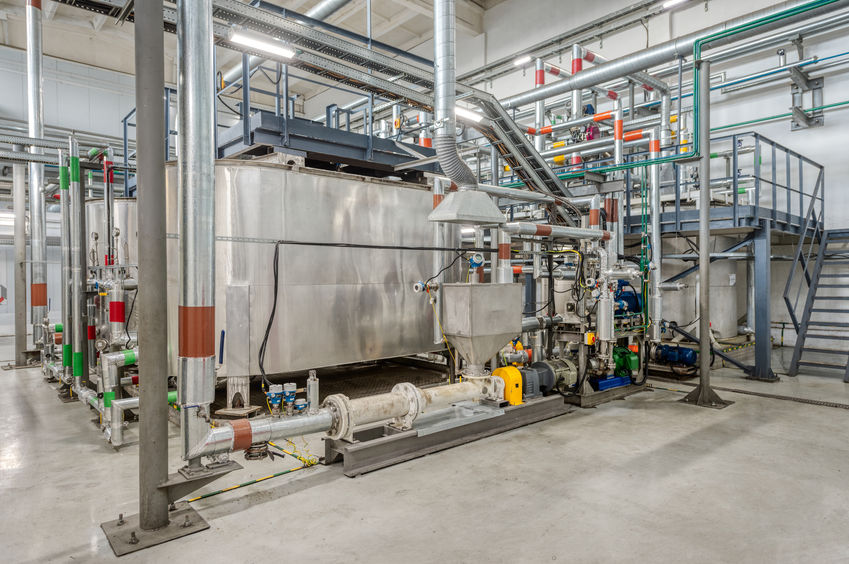
Designing a system with the correct compressed air pipe size is essential for achieving adequate and efficient airflow and air pressure, as air pipes that are too small or too large can cause a variety of issues.
If air compressor lines are too small, equipment at the point of use may experience pressure drops due to friction within the pipeline.
This is because air pipes that are too small in diameter will be unable to let the air flow at the speed and pressure that is required for the application, which will not only negatively impact the operation of the air-powered equipment it supplies but will also force the air compressor to operate at a higher pressure to compensate for the lower pressure downstream, resulting in an inefficient system that consumes excess amounts of electricity, making the compressor more expensive to operate.
While using compressed air pipe that is too large may not affect overall performance, it will be unnecessarily expensive as large air pipes require more material, labor and resources to construct, which will increase the cost of the compressed air system.
To determine if your compressed air pipe is too small to meet your system needs, you can check the pressure at the point that is furthest from the air compressor. Examine the tool or equipment at this end point to find the required operating pressure in pounds per square inch, or PSI. This will determine the pressure that must be maintained at the point of use. If a drop of more than 3 PSI is found and there is not a significant leak in the system, it could mean that the current air compressor piping is not adequate for the system needs and your system is not operating at its optimum level of performance or efficiency.
Factors that Influence Compressed Air Pipe Sizing
Several factors within the compressed air system play a role in achieving proper sizing of the compressed air pipe system, including:
Maximum CFM | Distance to Application |
Cubic feet per minute, or CFM, is the rate of airflow through the system. Maximum CFM values are needed for proper sizing, as this is the greatest demand at any given time, so the selected compressed air piping must be able to support peak CFM demands in order to avoid pressure drops. The compressor data plate should list the total flow rate supplied. While it is typically shown as CFM, it may also be shown in liters per second (l/s) or cubic meters per minute or per hour (m3/min or m3/hr). Generally, the higher the CFM, the larger the compressed air piping will need to be to avoid pressure drops. | The point-of-use application that is furthest from the air compressor will also play a role in proper pipe sizing. |
How to Calculate Compressed Air Pipe Sizing
To determine the correct pipe size for the compressed air system, you must make careful calculations based on the above factors and then consult a compressed air pipe size chart, using the following steps:
- Determine the maximum CFM for your system: Typically the manufacturer of the air compressor will provide the maximum CFM, which is the amount of air the compressor can pump out at a given pressure at any given time.
- Draw a piping schematic that includes all of the lengths of pipe and fittings, valves and bends in your compressed air piping system.
- Measure and add together all of the straight runs in the piping system in feet.
- Add additional length to account for each bend, fitting or valve. The general practice is to add 5 feet in length for each of these.
- Add your total length and equivalent lengths of fittings together to get the total length of air compressor piping for your system.
- Use the maximum CFM and calculated length of pipe and then consult a table or chart, which will be supplied by most manufacturers and distributors to help guide you toward the proper pipe size for your compressed air system.
It is also important to note future needs when sizing piping. If your calculation puts you at the upper end of the CFM ratings for a particular pipe size and further expansion is expected, consider sizing up to avoid future inefficiencies.
Compressed air pipe sizing calculations are important to the overall performance and efficiency of your compressed air system, but they can be confusing. For assistance with selecting the proper size for your compressed air piping system, please reach out to an expert at JHFOSTER, a Tavoron Company, today.