How to Find and Fix Leaks in Compressed Air Piping Systems
While they are essential to most manufacturing facilities, compressed air systems are notorious energy hogs and compressed air piping leaks are one of the biggest culprits when it comes to compressed air system inefficiencies. According to Compressed Air Best Practices, air compressor piping leaks can waste 20 to 30% of a compressor’s output and a plant that has not been well maintained will likely have a leak rate equal to 20% of total compressed air production. In addition, ignoring air compressor piping system leaks can result in underperforming end-use tools and equipment.
The good news, according to Compressed Air Best Practices, is that a facility with a solid leak detection and leak repair program can significantly reduce leaks to less than 10% of the compressor’s output, while optimizing compressor operation. To help boost air compressor efficiency and performance, this blog will provide best practices for air pipe leak detection, leak repair and leak prevention.
The High Cost of Compressed Air Piping Leaks
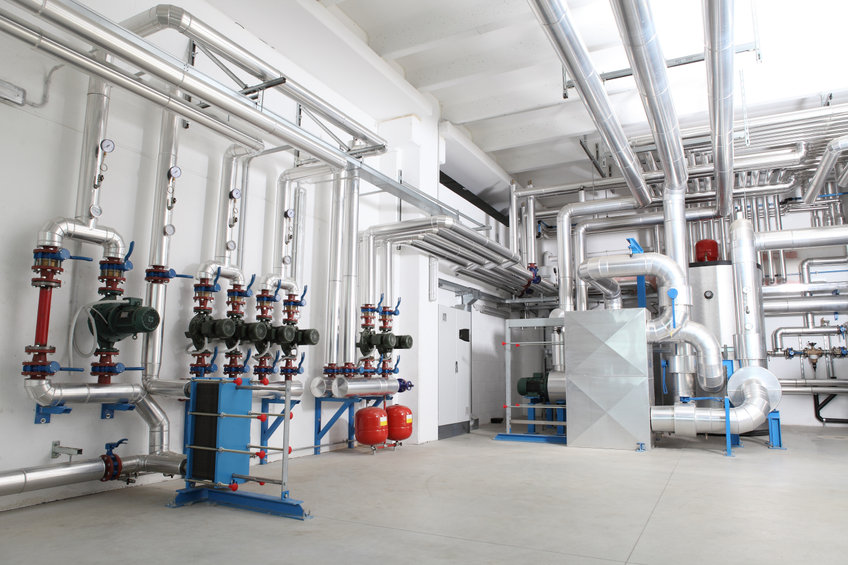
For the average facility, 20 to 30% of the electric bill is attributed to operating the compressed air system, and when you consider that the average facility loses 20 to 30% of that energy consumption to compressed air piping leaks, it’s easy to see how wasteful and costly leaks in air compressor lines can become.
Experts suggest that 1 CFM of air costs about $35 per shift annually, based on the average energy price of $0.08/kWA. And, a facility that runs two to three shifts per day can multiply that number by 2 or 3, while a 24/7 plant can multiply that figure by 4.
And, since most plants have multiple leaks in the air compressor piping system, the annual cost of wasted energy that can be attributed to air pipe leaks can be well into the thousands annually.
Aside from wasted electricity and money, leaks in air compressor lines can also result in pressure drop that negatively impacts the performance of point-of-use tools and equipment, slowing down production and productivity.
How to Detect Leaks in Air Compressor Piping
While leaks can turn up anywhere in an air compression delivery system, most leaks are found in the last 30 feet of hoses, connectors and fittings before the point of use, with the most common places being quick couplers, disconnects, pipe joins, rubber hoses and seals. Fortunately, once detected, leaks in these areas can be easily repaired by in-house technicians.
There are three methods that can be used to detect leaks in air compressor lines, as follows:
- Listen for leaks: It’s not uncommon to walk around the facility and hear hissing emanating from air compressor lines, which is a sure sign of a leak. However, leaks may not be audible if there is noise in the background or the air compressor piping is located near the ceiling.
- Soapy water: Applying soapy water to connections, joints or other areas of pipe where a leak is suspected is a good way to pinpoint the source. If there is a leak, soap bubbles will form and identify the precise location of the leak. However, this method is time consuming and requires access to the pipe.
- Ultrasonic leak detection: Ultrasonic leak detection devices can be used to pick up leaks in air compressor piping. Leak detection kits usually include microphones, amplifiers and audio filters and can detect sounds that are not audible to the human ear. This is the most reliable way to find air pipe leaks.
Once you’ve identified the source of the leak or leaks, be sure to tag them so they are easy to find when a technician returns to perform the leak repair.
How to Perform Air Compressor Line Leak Repairs
Simply detecting the source of the leak is not enough – repairs will be necessary. Before making any repairs, be sure to depressurize the entire system, or, if possible, isolate and depressurize the area being repaired.
Often, leaks can be repaired simply by tightening the connection. However, some leak repairs may be more involved. If leaks are found in couplings, fittings, pipe sections, hoses or other components that are damaged, these components will need to be repaired or replaced to stop the leak.
Following the repair, the system should be repressurized and tested to be sure the leak was addressed and that the air compression system is again in good working – and efficient – order.
Reducing the Need for Future Leak Repairs
Unfortunately, leaks are an ongoing issue in air compressor piping, especially as systems age. For this reason, leak detection and repair should be considered a continuous effort. Many service providers can conduct an air audit on a regular basis and perform leak repairs as needed. However, it is also possible to create an in-house leak prevention program that includes leak detection and repair on a regular basis using the methods discussed above.
To make it less likely that the compressed air piping system will experience leaks in the future, it’s a good idea to ensure that fittings, disconnects, hoses and tubing are all of the highest quality and that thread sealant is properly applied to connectors to help prevent future air leaks. Additionally, air pipes made of older or problematic materials, such as black iron piping, can be upgraded to modern piping materials with lower leak rates.
Because eliminating leaks in the compressed air piping system has the potential to save a facility thousands of dollars a year in wasted electricity charges while also ensuring optimal performance and efficiency, it is worth the effort and investment to detect and perform leak repair. For questions about leak repair or to schedule an air audit or compressed air service, please get in touch with JHFOSTER, a Tavoron company.