Complete Guide for Choosing the Right Air Actuator
Pneumatic actuation is a motion technology that sounds more complicated than it really is – pneumatic components take the energy made through compressed air and convert it into motion. This motion can be either linear or rotary, and powers applications across nearly all industries, from manufacturing to medical.
This style of actuator is known informally by many different names, including air cylinder, pneumatic cylinder, and air actuator. Traditional pneumatic actuators are made up of a few core parts: a piston, body, end caps, rod, seals, and bearings. All these components work together to create a vessel that seals in compressed air, which moves the piston and causes the rod to extend and retract – just like that, you have motion!
Why Use Pneumatic Actuators
Need highly reliable, efficient and a safe source of motion control? You can count on pneumatic actuators. They use pressurized air or gas to convert energy into rotary or linear motion. From the basic construction, pneumatic actuators can change and adapt to many applications. They can be made wholly or partially from different materials like aluminum, steel, or stainless steel, and are often offered with a variety of seal and bearing material options to suit different application environments. They can be repairable or non-repairable. Their motion profiles, pressure ranges, and overall build can influence how and when you utilize a certain style to achieve specific results.
Types of Pneumatic Actuators
There are a variety of types of actuators. Many companies choose pneumatic actuators over electric actuators due to cost-effectiveness. In many instances, pneumatic actuators will be a cheaper alternative to electric ones. Below you will find the different types of pneumatic actuators and what they are commonly used for.
Pneumatic Round Body Actuators
Round body pneumatic actuators are the most common, and flexible, style of pneumatic actuators. They can be repairable or non-repairable, with modifications to the basic cylindrical style to adapt to multi-position, rod lock, non-rotating, and dozens of other application needs. If you have a unique usage, a round body pneumatic actuator can likely be customized to fit your needs.
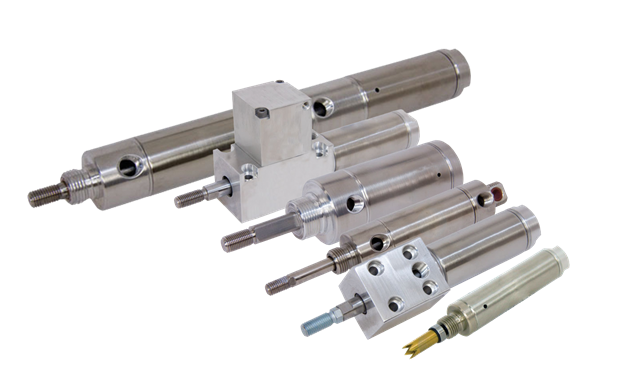
Pneumatic Rotary Actuators
These actuators are generally used for applications that require a range of motion. Compared to standard actuators, which generally provide linear motion, rotary actuators can provide up to 1080° of rotation. That makes these actuators ideal for applications such as pick and place, opening/closing, bending, indexing and so on.
Pneumatic Rodless Actuators
Pneumatic rodless actuators are generally used for point-to-point movements and in applications where space is a concern. Rodless actuators can achieve the same results as traditional round body actuators in up to 50% of the space, making them perfect for smaller machine footprints where you still need the output of a full pneumatic actuator. There are different styles, including models with built in guides to help in applications where the actuator may need to support a heavy load.
Tie Rod Cylinders
Tie rod cylinders are commonly used within the United States. They utilize four or more tie bolts that run the length of the cylinder body to secure the base and head plates together, preventing costly leakage. Many are also NFPA certified interchangeable, providing application flexibility. These cylinders are best used in applications that require larger bore sizes, longer strokes, and quick mounting, such as industrial machining.
Combination Rotary/Linear Actuators
This type of actuator is designed to be a direct rival to the electric actuator and combines the best features of both rotary and linear actuators. Combination actuators can be used for many applications including dispensing and packaging.
Applications of Air Actuators
It’s important to note that while air actuators are most often used in food and beverage, manufacturing, and production applications, they can be adapted to nearly any working environment.
The key to finding the right actuator for your application is identifying the correct size, style, and materials that you need to properly execute your applications.
Contact Us
To find the right air actuator for your needs, it is best to speak to a specialist that can identify the correct size and type of actuator for your project. Contact our specialists for careful consideration of application and precise sizing.