Choosing the Right Flow Control Valve Maximizes Performance
Although the importance of flow control valves is often overlooked, they are a critical component in industrial systems as they regulate and direct the flow, volume, rate and pressure of liquids or gases through piping systems and directly impact the safety and efficiency of the plant. While selecting an appropriate flow control device may seem simple, choosing a flow control valve is a challenging task because many factors must be considered to ensure the highest levels of safety and performance.
This blog will discuss four considerations for the selection process of these essential motion and flow control products.
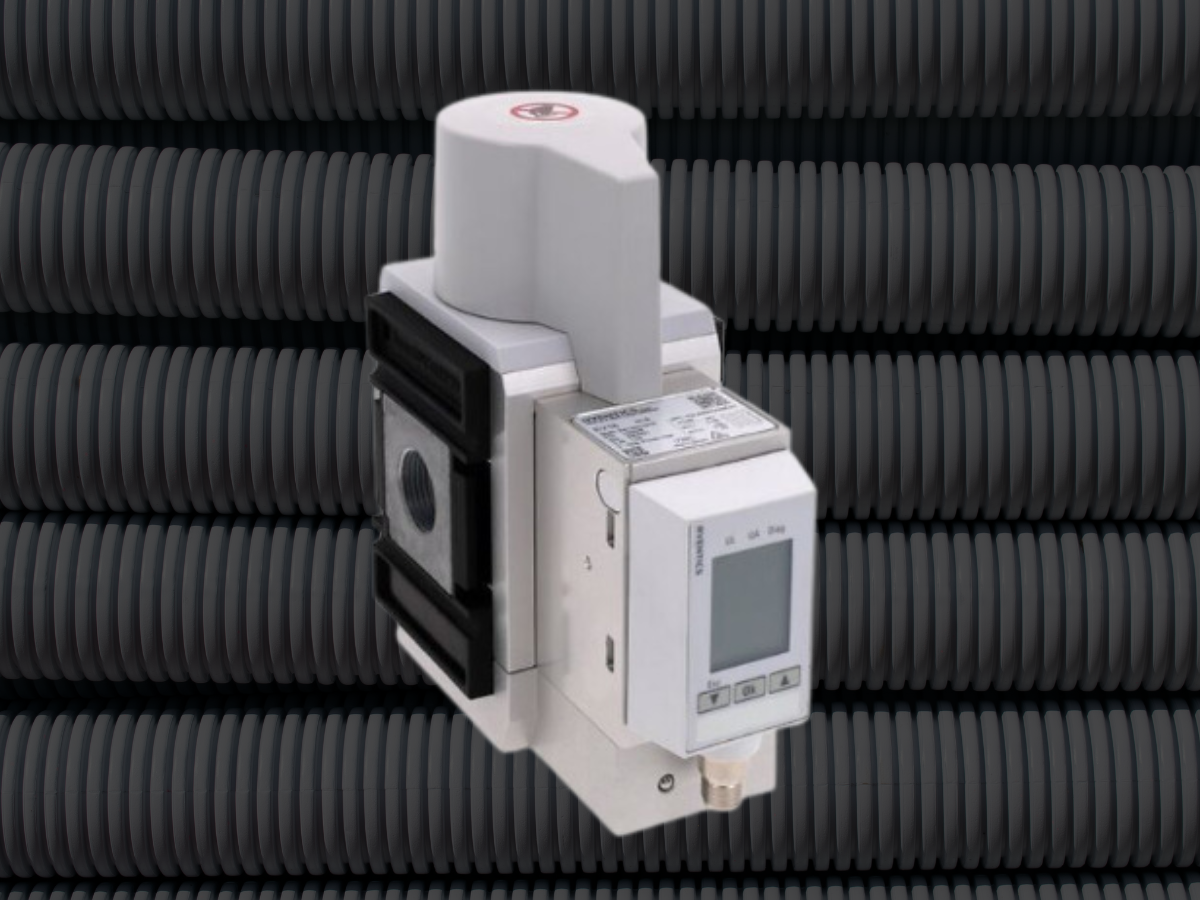
What are Flow Control Valves and Why are They Important?
Flow control valves are devices that regulate the flow of liquids and gases through various industrial systems or processes.
Valve flow control may be used to:
- Stop and start the flow of fluids or gases
- Vary or throttle the amount of flow
- Control the direction of flow
- Regulate system or process pressures
Because flow control valves serve different functions, there are a variety of flow control valve types to accommodate a range of industrial applications, including:
I/P Proportional control valves | These flow control valves are used for controlling or adjusting air flow through the system. As amperage is applied or varied to the solenoid of the valve, the output flow of the valve varies accordingly. |
Ball valves | These flow control devices contain an inner ball attached to a handle that, when turned, permits or prevents flow. |
Butterfly valves | These employ a metal plate attached to the handle to open (allow) or close (block) the flow. |
Needle valves | Needle valves provide flow control via a needle that opens or closes to allow or block the flow of air through the system. |
High-pressure flow control valves | A high-pressure flow control valve is a specialized valve used to precisely regulate the flow of liquids or gases at very high pressure levels, and can function as both a flow controller and a pressure regulator. |
No matter the type, a flow control valve is a combination of the following components:
- The valve: This is the modulating element of the device within which the ball, butterfly or needle that regulates and controls the flow is contained.
- The actuator: The function of the actuator is to initiate movement of the functional valve component to control the flow of air or liquid.
- Valve positioner: This flow control component ensures that the position of the valve stem corresponds to the set point from the controller. Based on positional feedback, it controls the pressure to the actuator to open or close the valve.
4 Considerations for Flow Control Valve Selection
Just as specifying the wrong flow control valve for the job will result in sub-par performance (and be a potential safety risk), selecting an appropriate flow control device can maximize efficiency and insure safety. So, here are four considerations for choosing a control valve that will provide the best performance.
- Flow: Understanding the flow requirements (and pressure) parameters of the system is integral to selecting a properly sized valve. An incorrectly sized flow control valve will present problems. If the valve is too small, there will be insufficient flow, which can cause pressure drop, unreliable flow and wear and tear on system components. If it’s oversized, it can create inefficiencies within the system and be difficult to control. The size of the control flow valve should be determined based on the system’s normal, minimum and maximum flow rate.
- Pressure: The maximum and minimum allowable pressure will influence the valve size and type and ensure that the valve can handle the pressure conditions of the system. Once pressure and flow requirements are determined, an appropriately sized and style of flow control valve can be selected and will provide the highest levels of efficiency and performance.
- Temperature: The maximum and minimum temperature of the process and ambient conditions should match the acceptable temperature range of the valve. Selecting a valve that cannot handle the temperatures of the environment will damage the valve and its components and create maintenance and performance issues.
- Media type and environment: If the valve is moving caustic media or is exposed to a process or environment that presents corrosive or harsh conditions, be certain that the valve’s materials of construction can withstand the environment in which it will operate. This will help prevent damage and ensure that the valve continues to provide safe and effective performance.
Careful selection of a flow control valve assures that it can handle the application’s flow, pressure and temperature parameters, as well as the media type. When all system requirements are met, the flow control device will provide the highest levels of efficiency and performance. Experts at JHFOSTER are available to discuss motion and flow control products and help select a flow control valve that meets all the parameters of the application.