A Look at the Essential Components of a Motion Control System
Motion control, a sub-field of automation, is widely used for production lines and in robotics and other equipment where it is necessary to precisely control the speed, acceleration, position and torque of individual axes of a machine. It’s important to note that motion control is actually a system made up of several essential components that work together in order to provide powerful, efficient movement of equipment in both factories and non-industrial applications. Each part – the motion controller, the drive, the motor and feedback device – plays an important role in achieving precise control and improving the system’s efficiency and performance. Below we will explore the components that make up a motion control system.
Four Essential Components of Motion Control Systems
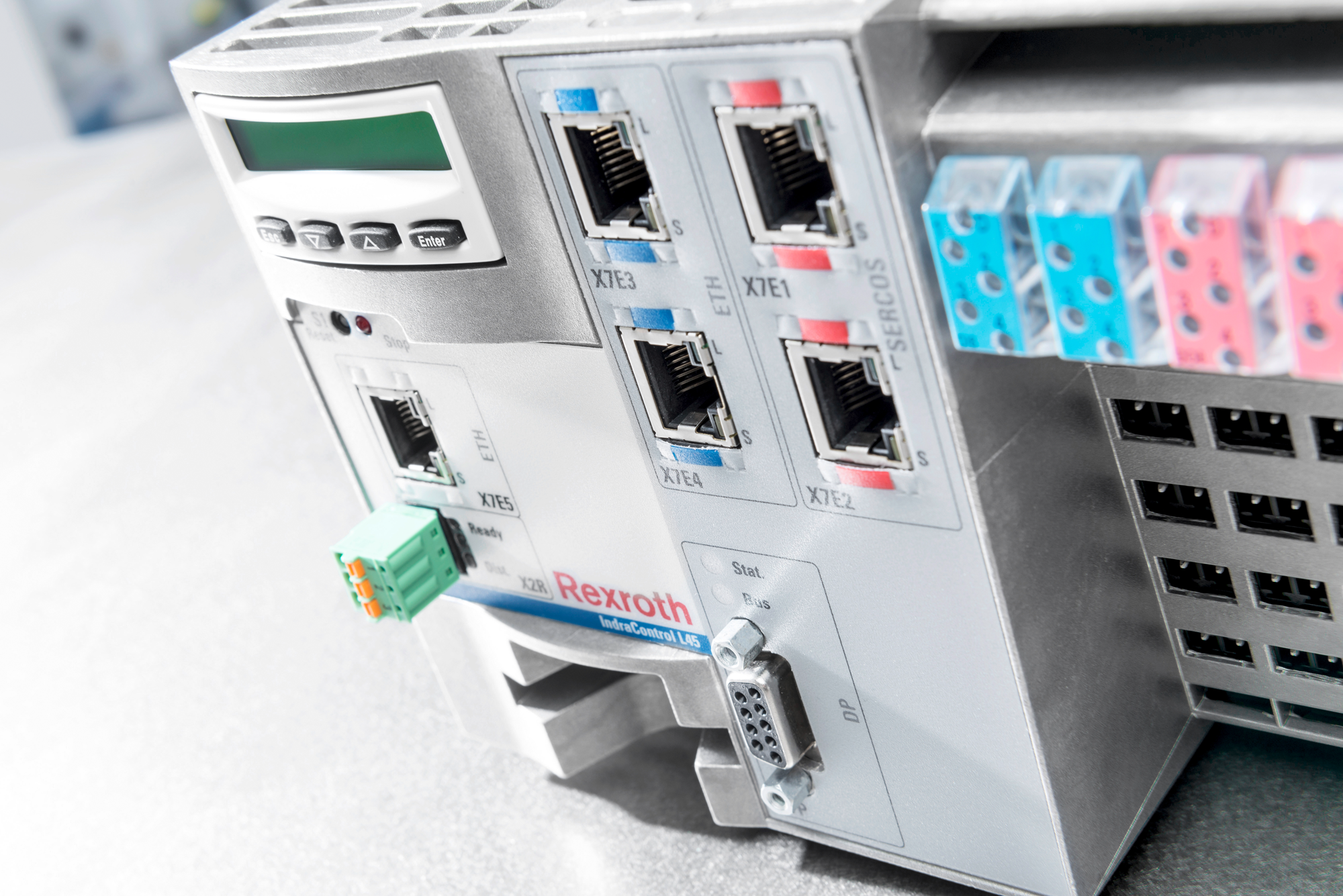
Motion Controller
Often referred to as the brain of the motion control system, the motion controller coordinates the motor drives; sometimes there are several drives being controlled at once. Based on the programmed target position and motion profiles, the motion controller creates the appropriate trajectories for the motors to follow. Like the human brain, it sends the command to accelerate to a precise speed and slow down to a stop at the desired location. The number of controllers used in an application will vary based upon the number of individual processes that require control. Each controller in a system will receive instructions from and send feedback to the computer or PLC that controls the machine or line.
The drive serves as the interpreter between the motion controller and the motor. Its function is to receive the command signal from the controller, interpret the command and then supply the proper level of power to the motor in order to provide accurate movement of the machine. Drives are available as digital, analog, linear, switching, stepper and servo drives. Each type of drive has different characteristics. Digital drives contain discrete input and output capabilities, while analog drives contain variable input and output capabilities. Linear drives are used for straight motion. Switching drives use a technique called pulse width modulation to turn voltage on and off rapidly to create a particular motion or speed. Stepper drives offer low- to mid-level torque and produce smooth rotation over a wide speed range. Servo drives interpret command signals and internal feedback loops to precisely control motion in high-power, high-speed applications.
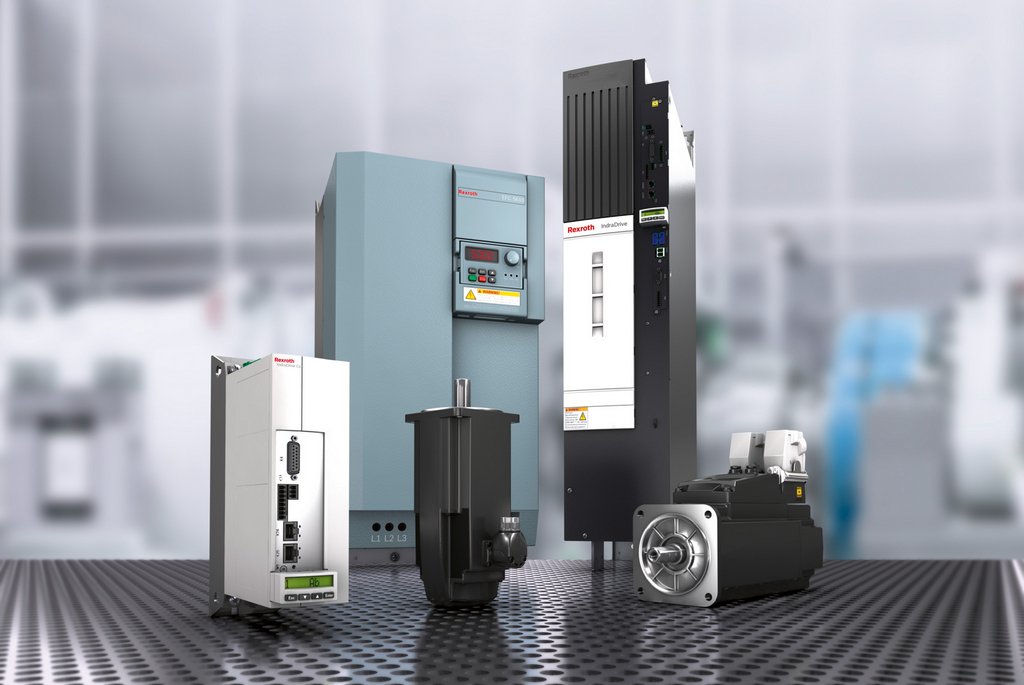
Motor Drive
Motor
The motor functions as the muscle. Its role is to receive the electrical input from the motor drive and convert it into motion. The two types of electric motors are AC and DC and they both transform electricity into motion by means of magnetic fields. DC motors run on Direct Current, while AC motors run on Alternating Current. The speed of DC motors is typically controlled by varying the amount of applied voltage. The speed of AC motors is typically controlled by varying the frequency of applied voltage. AC motors are more commonly used.
Used only in closed-loop motion control systems, feedback devices provide motor position information to the motion controller so it can make adjustments to its commands at the appropriate times. Encoders, which measure and report position, velocity and direction, are the most popular feedback device. Closed-loop motion control systems can precisely perform complex motions that open-loop motion control systems can’t.
Feedback Devices
Where is Motion Control Used?
As manufacturers aim to improve their efficiency and lower their operational costs, machine automation is becoming more prevalent on the factory floor and motion control systems are playing a huge role in rapidly evolving the industrial world.
Some common applications for motion control systems include pick-and-place motions for packaging and palletizing; complex motions such as welding, assembly or cutting; CNC machining; 3D printing; material handling; textile manufacturing; automotive assembly and many others where intricate motions must be made precisely and repeatably while being easy to change if needed.
In these and other applications, motion control systems can meet the needs of the task. As plant floors continue to become more and more automated, motion control systems will continue to play a growing role in helping manufacturers increase their quality and efficiency.
For more information on motion control systems or components, please contact a representative at JHFOSTER.