A Look at Leading PLC Brands for Industrial Automation
Programmable logic control (PLC) industrial automation systems are one of the fastest growing segments as they support the growing trend toward digitalization of the factory, or Industry 4.0.
However, with several leading PLC companies, it can be difficult to select the right PLC brand for the requirements of an application. This blog will compare offerings from top PLC manufacturers and offer key considerations for the selection process.
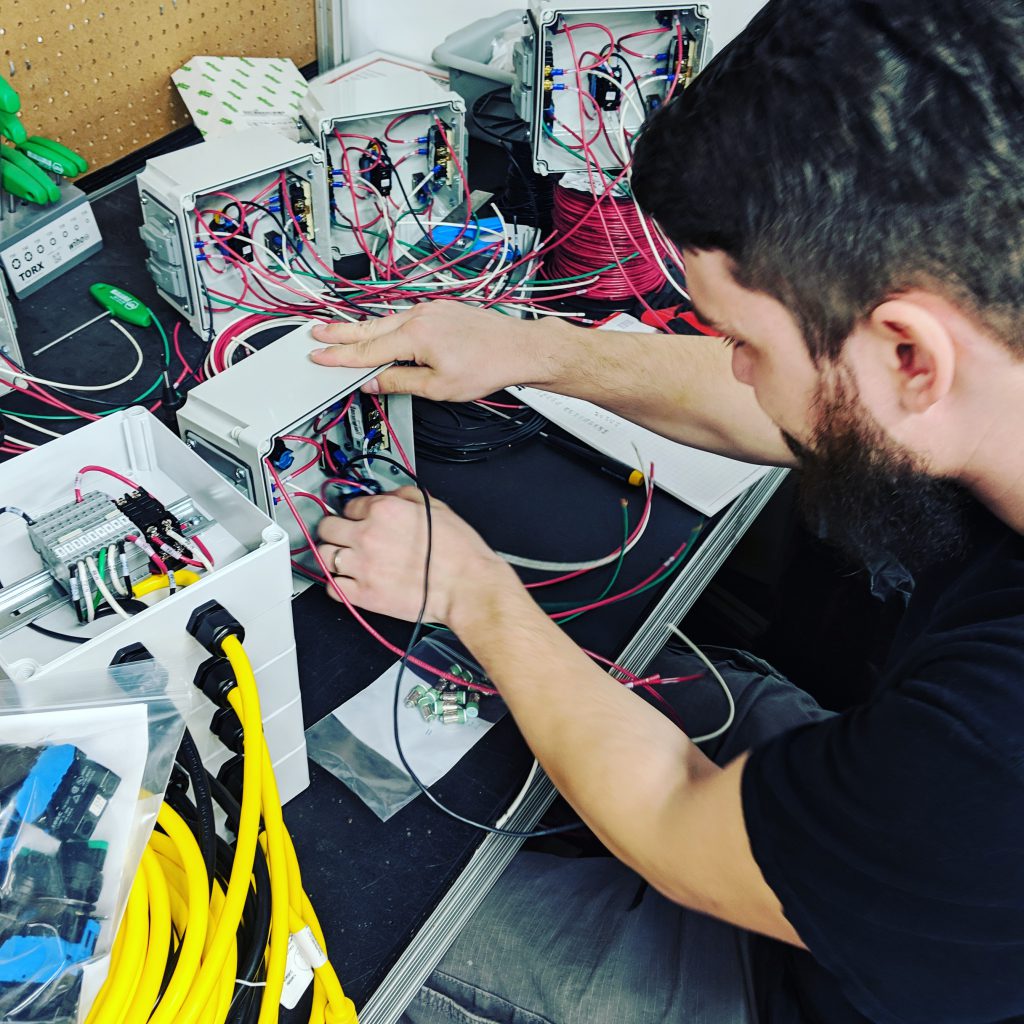
What is a PLC and Why is PLC Integration Important?
In simple terms, a PLC is a small, ruggedized, digital computer-based device used to control industrial automation. A PLC is made up of a central processor unit, memory, input/output (I/O) modules and communication interfaces.
PLCs are capable of monitoring and recording equipment or process parameters such as temperature or pressure, performing control tasks such as switching relays and controlling motors and generating alarms if equipment goes out of spec, as well as other essential automation duties.
PLCs are widely used in industry because they offer flexibility, reliability and scalability.
PLC integration involves linking PLCs with other devices, systems and applications to create a connected, integrated solution that streamlines manufacturing processes and permits remote monitoring and control.
In order to achieve PLC integration, the PLC is connected to devices such as sensors, IoT devices, actuators, human machine interfaces (HMIs) or other control systems so that operators can more easily and effectively control equipment or processes. The greatest advantage of PLC integration is the ability to collect information from sensors and IoT devices and then analyze the data in real time, allowing operators to identify maintenance issues, inefficiencies and opportunities for improvement.
By connecting PLCs to the internet or facility network, PLC integration also allows operators to remotely monitor and control operations based on the supplied real-time data. The incorporation of PLCs, along with real-time monitoring and control, helps manufacturers reduce downtime, increase efficiency and optimize productivity.
PLC Selection Criteria for Industrial Automation
Choosing the right PLC for an industrial automation application is crucial to how well it functions in the operation. While consulting with a professional integrator is likely to yield the best results, some preliminary research can be beneficial. Below are the key considerations when searching for a PLC:
- Application requirements: It is essential to understand the complexity and scale of the automation tasks expected of the PLC.
- I/O capacity: Since PLCs rely on the input and output of data to operate, check the I/O capacity of the PLC to ensure that it can handle the required number of inputs and outputs for the application.
- Communication protocols: Because the PLC must be able to communicate with other components in the automation system, communication protocols are an essential consideration. PLCs should support the necessary standards, such as Ethernet/IP or Modbus to ensure seamless PLC integration.
- Processing speed: Complex systems that must be tightly or quickly controlled will require a PLC with very fast processing speeds and enough memory to support the anticipated operations.
- Scalability: Because operations change and expand, a PLC that can easily accommodate more automation in the future is essential.
A Comparison of Leading PLC Manufacturers
It can also be helpful to identify the top-selling PLC brands and compare the advantages of each. While all of the widely used PLC manufacturers have offerings that are designed to be easy to program and set up, many offer additional features and capabilities that support the demands of modern PLC industrial automation systems, and all will provide reliable and efficient control solutions. However, each PLC brand has its advantages in certain situations.
Below is a list of 3 PLC companies and the features that set them apart from the rest of pack.
Rockwell Automation’s Allen Bradley ControlLogix PLC | Known for user-friendly interfaces and seamless automation, these PLCs offer scalability for growing operations and enhanced communication options for flexibility. The motion control capabilities are top-notch, making it ideal for applications such as robotics where precise control and coordinated movements are essential. |
Schneider Electric’s Modicon PLC | Schneider Electric’s PLC stands out when it comes to seamless integration and IoT applications. It offers numerous I/O options and cybersecurity features, permitting secure connectivity. These PLCs are also reliable, precise and offer a ton of innovative features not found in other PLCs. |
Siemens Simatic PLC | Siemens Simatic series is the most popular industrial PLC due to its reliability and features. This PLC brand offers high processing speeds, integrated safety functions and comprehensive self diagnostics. Siemens’ PLCs offer precise operation, which is crucial for complex industrial operations |
Selecting the PLC brand that best meets the needs and specifications of the application will ensure that industrial automation equipment and systems operate at the optimal levels of efficiency and performance. While the decision can be a hard one to make, using the right selection criterion and being informed about the best-selling PLC brands for industrial automation can make the process go more smoothly. Be sure to consult with the experts at Celco, a Tavoron company, when selecting a PLC and working on PLC integration.