A Comprehensive Guide to Compressed Air Piping Materials
In a compressed air system, the air compressor is often thought of as the heart so, in keeping with that analogy, compressed air piping can be considered the circulatory system as it delivers treated compressed air around the facility to end-use applications. For this reason, it’s important that the material used for air compressor piping is not only suitable, but also sturdy, safe and capable of efficiently delivering clean air to all the endpoints. This blog aims to explore the pros and cons of the various materials used for compressed air lines.
What Are My Choices for Air Compressor Piping
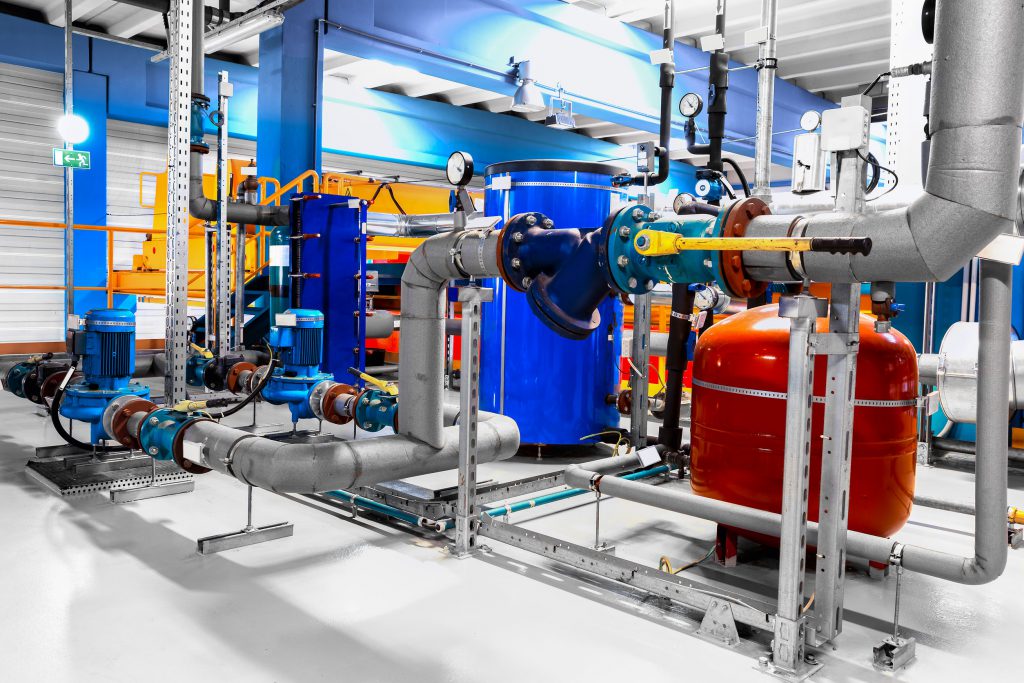
Many options are available for compressed air line materials; however, choosing the most suitable compressed air piping material is essential to the overall performance and efficiency of the compressed air system. So, while the choice typically comes down to tradeoffs between safety, cost, performance and longevity, a thorough evaluation is necessary.
The following commonly used air compressor piping materials will be discussed in detail in this blog:
- Aluminum
- Black pipe
- Stainless steel
- Copper
- Galvanized pipe
- Plastic pipe
Because all of these compressed air piping materials are not created equal, the pros and cons of each are discussed below.
Aluminum Compressed Air Piping
Aluminum air pipe is quickly becoming one of the most popular choices for air compressor line – and for good reason. Aluminum compressed air piping is lightweight, provides years of leak-free operation and is easy to install, especially when using push-to-connect aluminum compressed air piping systems.
Another benefit of aluminum air pipe is that it offers smooth interiors, which reduces friction and helps maintain the efficiency of the compressed air system. It is corrosion resistant so there is minimal chance of introducing contamination from the piping itself into the compressed air system, making aluminum compressed air piping an excellent choice for systems that require very clean, pure air.
Black Iron Compressed Air Piping
Black iron is one of the most commonly used materials for compressed air piping. Although black iron pipe is strong, durable, readily available and cost effective, it is susceptible to corrosion, so can lead to contaminated compressed air lines that can damage pneumatic end-use applications or finished product.
Further, it is time-consuming to install and features threaded connections that may slip and leak over time, resulting in lost energy and reducing the efficiency of the compressed air system.
Stainless Steel Air Compressor Piping
Like black pipe, stainless steel air compressor lines are strong and durable, but unlike black iron, compressed air piping constructed from stainless steel is not prone to corrosion, so it provides a clean source of air. However, installation can be time consuming as stainless steel can be difficult to cut and work with. Stainless steel piping is also susceptible to air leaks around the joints, so it can reduce the efficiency of the compressed air system. Although stainless steel is aesthetically pleasing in a facility, it comes with a high price tag.
Copper Compressed Air Piping
This corrosion-resistant compressed air piping choice is lighter than stainless steel and black pipe and makes an attractive option around the facility. In addition, copper piping has a very smooth interior, so it promotes efficiency and is suitable for applications that demand very clean air; however, it is very expensive, making copper cost prohibitive for most industrial installations.
Galvanized Air Compressor Piping
While the plating used in galvanized piping helps it resist the moisture contained in compressed air systems, the coating is inclined to flake and peel, which can lead to system contamination. The contamination may be so severe that it can damage the pneumatic tools and equipment supplied by the compressed air system or contaminate products made using the air stream.
Further, it is also time-consuming to install and features threaded connections that may slip and leak over time, resulting in lost energy and reducing the efficiency of the compressed air system.
Plastic Air Compressor Piping
First and foremost, it is important to note PVC and CPVC piping are NOT Occupational Safety & Health Administration (OSHA)-approved for use in air compression systems. OSHA mandates that these materials should never be used for air compressor piping as they are not strong enough to withstand the high pressures of compressed air systems. In addition, they may degrade over time due to exposure to air compressor oils and lubricants, further weakening the material. Once these materials become brittle, it is possible that PVC or CPVC piping will crack, break or shatter and create lethal flying projectiles when exposed to system pressure.
That said, plastic air compressor piping made of ABS, PE and HDPE are more durable and will not degrade when exposed to air compressor oils or lubricants. They are lightweight, easy to install and offer a smooth interior surface to increase efficiency. Further these approved plastic materials do not corrode, so the risk of contamination is minimized. However, plastic materials do not offer the strength, durability and longevity of recommended metal compressed air piping materials and are prone to air leaks around joints and connectors.
Because there are many options when it comes to compressed air piping and you want the material that will provide the cleanest air possible at the highest levels of system efficiency while meeting the needs of the application and the budget, please reach out to the experts at JHFOSTER, a Tavoron company, for assistance with air compressor piping selection.