8 Tips for Efficient and Safe Compressed Air Piping
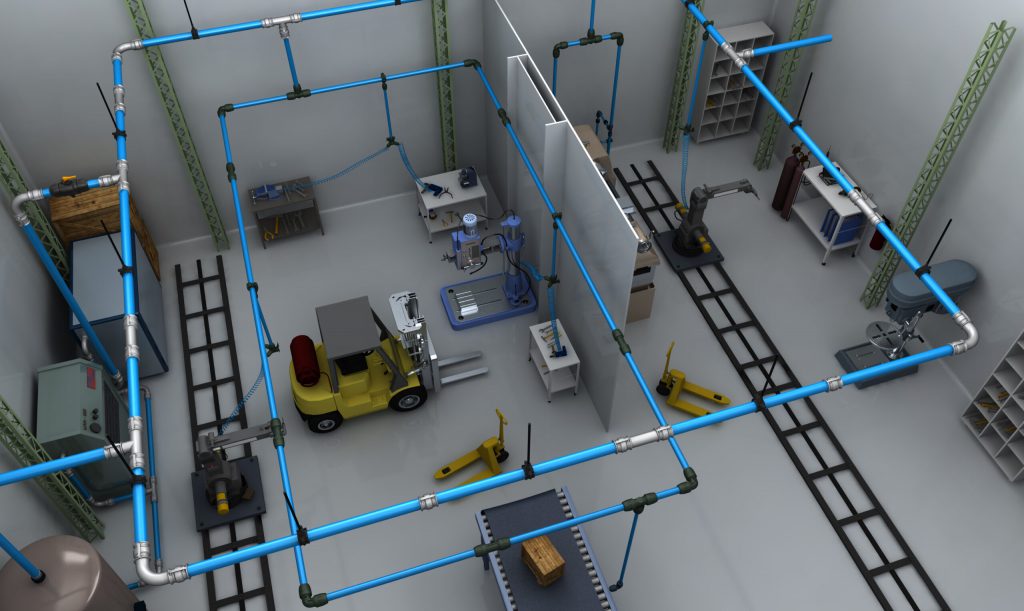
Compressed air systems play a significant role in most industrial facilities as they provide power to the tools, equipment and automation used in production. While air compressors, the heart of the compressed air system, get most of the attention, compressed air piping, which distributes the air to the end points, plays an equally important role in the system.
So, when designing compressed air piping systems, it’s important to do it right in order to ensure the highest levels of efficiency and safety. To that end, we present eight tips for compressed air piping design.
Designing Compressed Air Piping Systems for Efficiency
Compressed air piping design has a huge impact on the efficiency of the overall system. To maximize efficiency be sure to do the following:
1. Optimize the compressed air piping system to prevent pressure drop
While pressure drop can be related to leaks in the system, it can also result from undersized piping, sharp turns and junctions in the piping layout. As compressed air travels through the system, the velocity of air will diminish as it changes direction, resulting in turbulent flow that causes pressure to drop. The compressed air system will have to work harder to compensate, creating significant inefficiencies. Minimize the amount of turbulence by using gentler and fewer pipe bends. Experts suggest a 30- to 45-degree angle for turns, create a continuous loop for the main plant distribution piping whenever possible, and use properly sized piping to achieve maximum efficiency.
2. Choose materials for compressed air piping wisely
A variety of industrial piping solutions exist and each material has pros and cons regarding performance, durability and safety. Black iron, galvanized steel, stainless steel, aluminum and copper are the most common choices; however, some metal piping is subject to corrosion, which may result in contamination in the system and obstructions in the compressed air piping that can create inefficiencies.
Aluminum, which is lightweight, smooth and corrosion resistant is a popular choice. Stainless steel is a common choice in industries such as food and beverage, pharmaceutical and medical device production as it resists corrosion and meets stringent requirements for cleanliness.
3. Use shorter runs of compressed air piping
Long lengths of piping can negatively impact the efficiency of a compressed air system, as longer lengths may result in pressure drop because the system must work harder to force air through long runs.
One way this can be avoided is by using a compressed air piping design based on a looped piping layout, especially if the facility is smaller in footprint. A looped piping layout with gentle bends will reduce instances of long lengths of pipe and sharp turns, allowing air to flow through the system with fewer obstructions, minimizing pressure drop and boosting efficiency.
4. Plan future needs into compressed air piping design
Be sure to plan for future needs when selecting an air compressor and designing the compressed air piping layout. It is much easier and more efficient to plan for future demands and expansions during the design stage than it is to modify compressed air piping at a later date.
5. Take precautions to control moisture
Moisture is a byproduct of the air compression process, but it can be detrimental to a compressed air system as it will lead to corrosion within the system that can damage components, create rust and other obstructions, contaminate generated air and degrade efficiency of the overall system.
When selecting compressed air piping, opt for materials that can handle anticipated moisture levels without corroding. And, when planning a compressed air piping design, be sure to include drain valves that release moisture from the system. Additionally, aftercoolers, dryers and filters should be included in the system design to help combat moisture and condensation.
Compressed Air Piping Safety Considerations
While efficiency is important, the safety of employees and assets is also a significant concern when designing a compressed air piping layout. Although compressed air is generally safe for use, the following should be acknowledged:
6. Pay attention to pressure ratings of compressed air piping
When planning a compressed air system, be sure all components, including the compressed air piping material, hoses and fittings, meet building codes and have the proper pressure rating. In addition, be sure to include gauges for monitoring and pressure relief valves as required on storage tanks and within the distribution system that will automatically release air if pressures reach dangerous levels.
7. Do not use PVC for compressed air piping
PVC is not an OSHA-approved compressed air piping material for a reason. Over time it can become brittle and burst under the high pressures and flows associated with compressed air systems, creating safety hazards and health risks. Instead, opt for OSHA-approved plastics or corrosion-resistant metals when choosing industrial piping solutions for a compressed air system.
8. Take proper safety precautions with compressed air piping
There are a number of general safety precautions when working with compressed air piping. Air lines should be inspected frequently for brittleness, wear and defects that could result in burst pipes and flying debris. Additionally, compressed air piping should be clearly marked and labeled with maximum working pressures to ensure safety and prevent hazardous conditions. Provisions for vibration isolation, thermal expansion and contraction need to be taken into consideration also.
By considering these tips when selecting piping for compressed air and designing a piping layout, it will help ensure that your compressed air system is efficient and safe. A well-designed compressed air piping layout will enhance the performance of the compressed air system and the facility. JHFOSTER experts are here to assist you with compressed air piping design and layout concerns.