6 Reasons to Avoid Galvanized Pipe for Compressed Air Lines
Piping is a critical component of the compressed air delivery system as its purpose is to efficiently and safely transport air to the points of use, such as pneumatic tools, machinery and automation. For this reason, compressed air pipe must be tough enough to withstand high pressures, resist corrosion and be easy to install and maintain.
While galvanized pipe is a common choice, it has some major disadvantages, so it is not the best pipe for compressed air systems. This blog will explore the hazards of using galvanized pipes in the compressed air delivery system and suggest other alternatives.
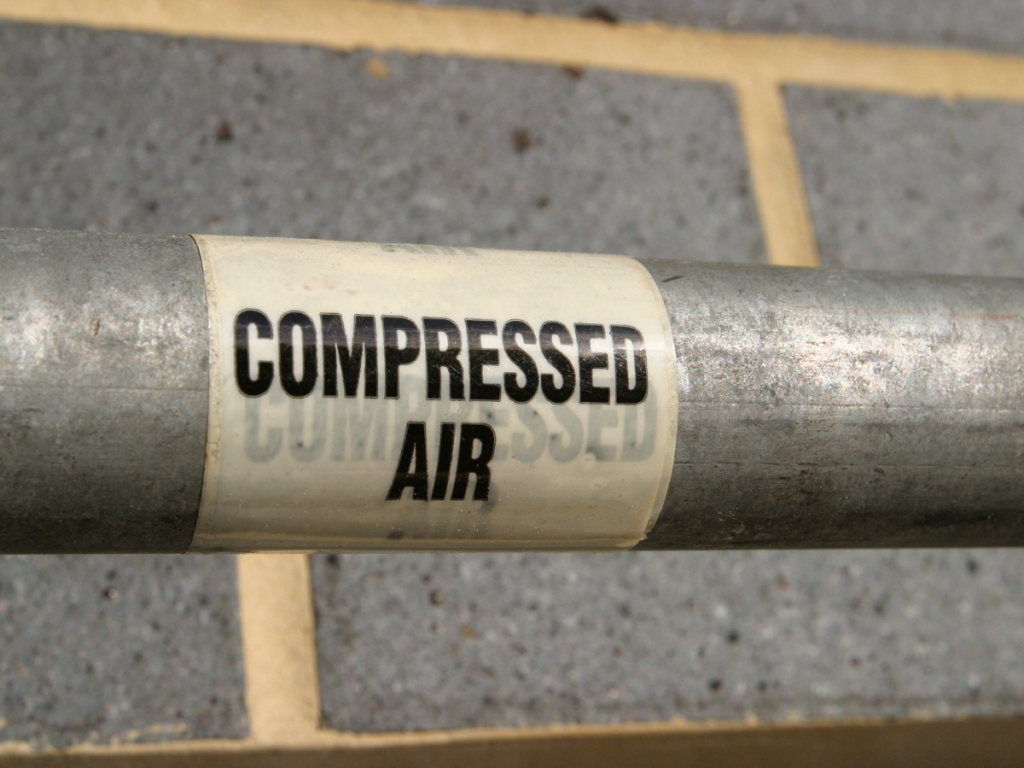
What is Galvanized Pipe?
Let’s start with the basics and answer the question: “What is galvanized pipe?”. Originally invented as an alternative to lead pipe for water supply lines, galvanized pipes are steel pipes that have been coated in a protective layer of zinc using a process called hot-dip galvanization to prevent corrosion and rust.
Because zinc corrodes more easily than steel, it serves as a “sacrificial” coating and provides an additional layer of protection against corrosion, making galvanized pipe durable enough to withstand challenging industrial environments and the high pressures of compressed air systems. In addition, galvanized pipe for compressed air is inexpensive and readily available, making it a popular choice for compressed air pipe in the past.
The Trouble with Galvanized Pipe for Compressed Air
While its durability and cost are advantageous, there are some significant issues with its use as a pipe for compressed air. The most concerning shortcoming is that the zinc coating will degrade over time and flake off inside the piping.
Another major hindrance with galvanized pipe for compressed air systems is that it is time-consuming to install. Additionally, galvanized pipe has a higher coefficient of friction than other materials, so it may cause issues with pressure drops, while the threaded connections can slip and leak over time.
6 Reasons to Avoid Galvanized Pipe for Compressed Air
The above-mentioned drawbacks of galvanized pipe can lead to a bevy of problems for the air delivery system, including:
- Inefficiencies: Because the zinc coating breaks down over time, it is prone to rust and corrosion. Galvanized pipe corrosion creates flakes that can lead to blockages in the air delivery system, causing the system to work harder – and consume more energy – in an effort to maintain the air supply. In addition, because of the threaded connections, galvanized pipes are prone to air leaks that waste energy. Additionally, the low coefficient of friction may create system-wide pressure drops, again forcing the air compression system to work hard to supply the air, consuming excess energy.
- Excessive maintenance: Flakes of rust caused by galvanized pipe corrosion can collect in the air network and cause blockages throughout the system, forcing the air compressor to work harder to meet air demand. Ultimately, this will cause wear and tear, creating maintenance issues and reducing the lifespan of the air compressor and components.
- Point-of-use equipment damage: Those same flakes of rust can travel through the air delivery network and end up inside the pneumatic tools and machinery, resulting in damage that impacts the performance of the equipment, causes maintenance headaches and shortens equipment lifespan.
- Poor air quality: When contamination from galvanized pipe corrosion enters the air compression system, it can travel through the delivery network along with the treated air. Contamination from galvanized pipe corrosion will reduce the quality of the air and can negatively impact finished product quality.
- Safety risks: The biggest safety risk associated with using galvanized pipe for compressed air is that over time it will corrode and corroded pipes are likely to rupture due to the high pressures associated with compressed air systems. An additional risk is related to the rust and corrosion flakes that can be blown through the air lines at high speeds. Both can result in hazardous situations and injuries.
- Increased expenses: Galvanized pipe is often difficult and time consuming to install as it requires cutting and threading. Hiring a professional installer is always recommended, so this will increase the cost and complexity of installation. Further, because it is prone to leaks, maintenance technicians will spend time chasing down and repairing leaking pipes more often with galvanized pipe. The inefficiencies and maintenance issues caused by galvanized pipe corrosion will also increase operating expenses.
Alternative Compressed Air Pipe Choices
The significant issues associated with galvanized pipe corrosion have left many engineers searching for alternatives. Fortunately there are plenty of other suitable options, which are covered in a comprehensive guide to compressed air pipe options that can be found here.
But, in short, for the cleanest air and highest levels of efficiency, performance and safety, the following materials are recommended for compressed air pipe:
Stainless steel
Stainless steel prevents corrosion and offers a smooth interior, making it a great choice for efficiency and for sensitive applications such as food and pharmaceutical processing.
Aluminum pipe
Aluminum compressed air pipe is anti-corrosive, light in weight and easy to install. Smooth interiors make it energy efficient and low maintenance.
Copper pipe
Copper pipe is also corrosion resistant and lightweight. It is a high-quality and durable compressed air pipe material.
Because compressed air pipe is a critical part of the air delivery system, it is best to choose a material that is durable and corrosion free. While galvanized pipe has been used for years in compressed air systems, it is no longer the superior choice because galvanized pipe corrosion can create issues with system efficiency, performance, maintenance and safety, and reduce the purity of the treated air. For assistance exploring alternative solutions, please contact the pros at JHFOSTER, a Tavoron company, today.