5 Ways to Use SCADA Automation for Compressed Air Monitoring
Compressor monitoring is a great way to optimize compressor efficiency and coordinate maintenance plans. And, when operating a multi-compressor installation, users may find they need a more centralized compressed air monitoring control platform. Fortunately, Supervisory Control and Data Acquisition (SCADA) systems, which combine hardware and software technologies for the monitoring and control of industrial equipment and processes, can be applied to compressed air management systems in a variety of ways with great results.
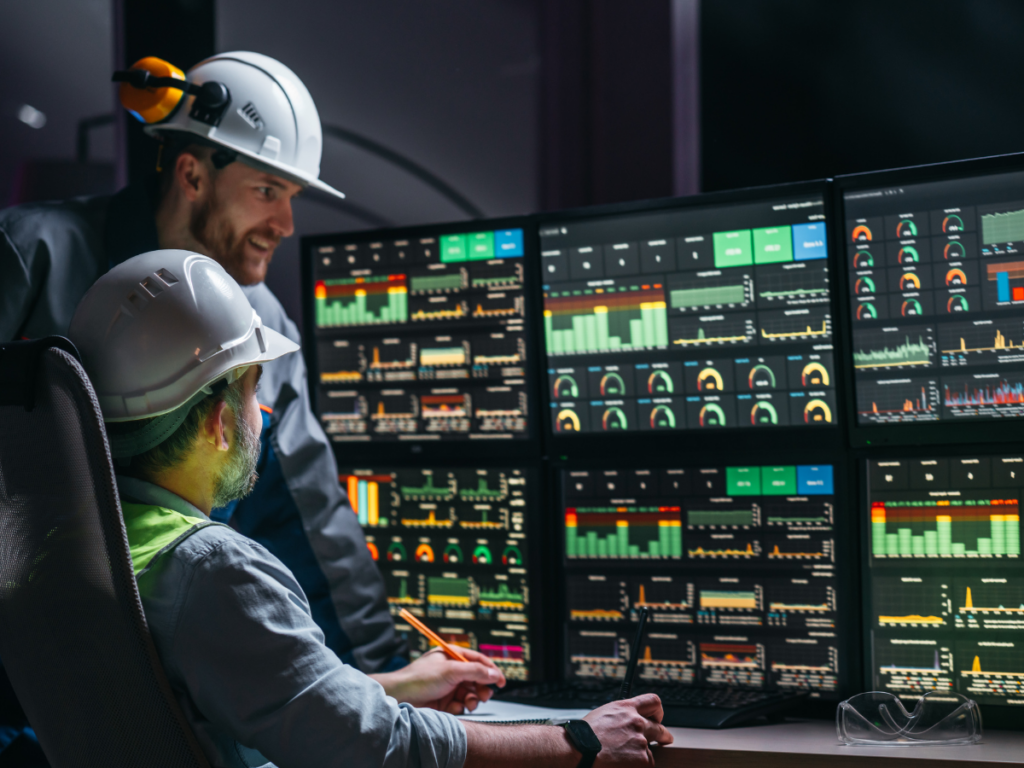
What is SCADA Automation?
SCADA systems provide centralized monitoring and control of industrial processes, including compressed air management systems. SCADA automation uses computers, data networks and graphical interfaces for management of industrial equipment and processes. In operation, SCADA solutions collect data from sensors, send it to the PLC SCADA (Programmable Logic Controller) component, which uses the information to provide precise control of the system with the goal of optimizing operations. HMI SCADA (Human Machine Interface) components or other graphical interfaces allow operators to view graphical information about the system so they can make adjustments based on real-time data.
5 Ways to Use SCADA Automation for Compressed Air Monitoring
SCADA Automation can be applied to the control of air compressor monitoring systems and is especially helpful in the management of multi-compressor installations. When utilized as a compressed air management system, SCADA automation systems collect data from sensors that are located on the air compressor and/or other air compression system components so that operators can monitor and control all the air compressors in the facility from a single, centralized location.
The goal of using SCADA solutions as an air compressor monitoring system is to minimize the amount of compressed air that is being used while still delivering the precise amount of air in order to maintain production. This encourages optimal compressor performance and energy efficiency, while also cutting associated costs.
SCADA Automation can be applied to compressed air monitoring in the following ways:
- Optimize Energy Efficiency: By using a centralized control system to gather real-time operational data, SCADA automation systems can optimize energy efficiency of the air compression system. From one centralized location and in real time, systems can assure the correct combination of equipment is being used to meet current demand and ensure that the system is maintaining stable pressure and flow during operation. Using SCADA control strategies to curtail unnecessary energy usage helps reduce electricity costs and ensures that energy is being used in the most effective way.
- Enhance Compressor Performance: Because SCADA automation allows remote monitoring and control, it can be used to make real-time adjustments to operational parameters that are going out of spec, improving performance based on the current conditions. Data analysis and reporting options also encourage users to trend compressor demand and air usage so that patterns can be identified, allowing continuous improvement efforts in performance and energy efficiency. Additionally, tightly controlled compressors can be adapted to varying process conditions and demands for air, providing consistent performance even under fluctuating workloads.
- Improve Reliability: Using SCADA control strategies in multi-compressor installations permits load sharing and load distribution based on the current demand. This permits distribution of the workload evenly between compressors, preventing overloading, as well as wear and tear on the equipment. Tight control of load sharing and distribution helps minimize breakdowns and maximize reliability of the air compression system. Further, the lifetime of each compressor will be extended, reducing equipment repair and replacement costs.
- Plan Preventive Maintenance: When SCADA automation systems are used for compressor monitoring, they can identify performance anomalies that may signal upcoming maintenance issues and alert operators. The information can be applied to preventive maintenance planning so small issues may be addressed before they become larger problems. Using SCADA systems in this way will minimize downtime, increase reliability of the system and reduce costs associated with more significant repairs, ultimately preventing premature replacement of air compressors and components.
- Detect Leaks: A SCADA system used for compressed air system monitoring can provide insight on system wide compressed air leak losses. This helps bring attention to leak losses faster, minimizing energy waste and costs.
An effective compressed air management system provides optimal efficiency, performance and reliability and reduces operational costs by minimizing energy consumption, downtime and maintenance costs. SCADA automation systems provide an effective strategy for remote and centralized compressed air monitoring and control, especially in multi-compressor installations. To learn more about how SCADA automation for compressor monitoring can optimize energy efficiency, enhance performance, assist with preventive maintenance planning and augment flexibility, please reach out to the experts at JHFOSTER today.