10 Common Machine Guarding Mistakes—and How to Avoid Them
In today’s fast-paced manufacturing and industrial environments, safety must be built into every system, not added as an afterthought. Machine guarding is one of the most effective ways to protect workers from injury and ensure compliance with safety regulations. However, even well-intentioned efforts can fall short when guarding solutions are poorly designed, incorrectly installed, or improperly maintained.
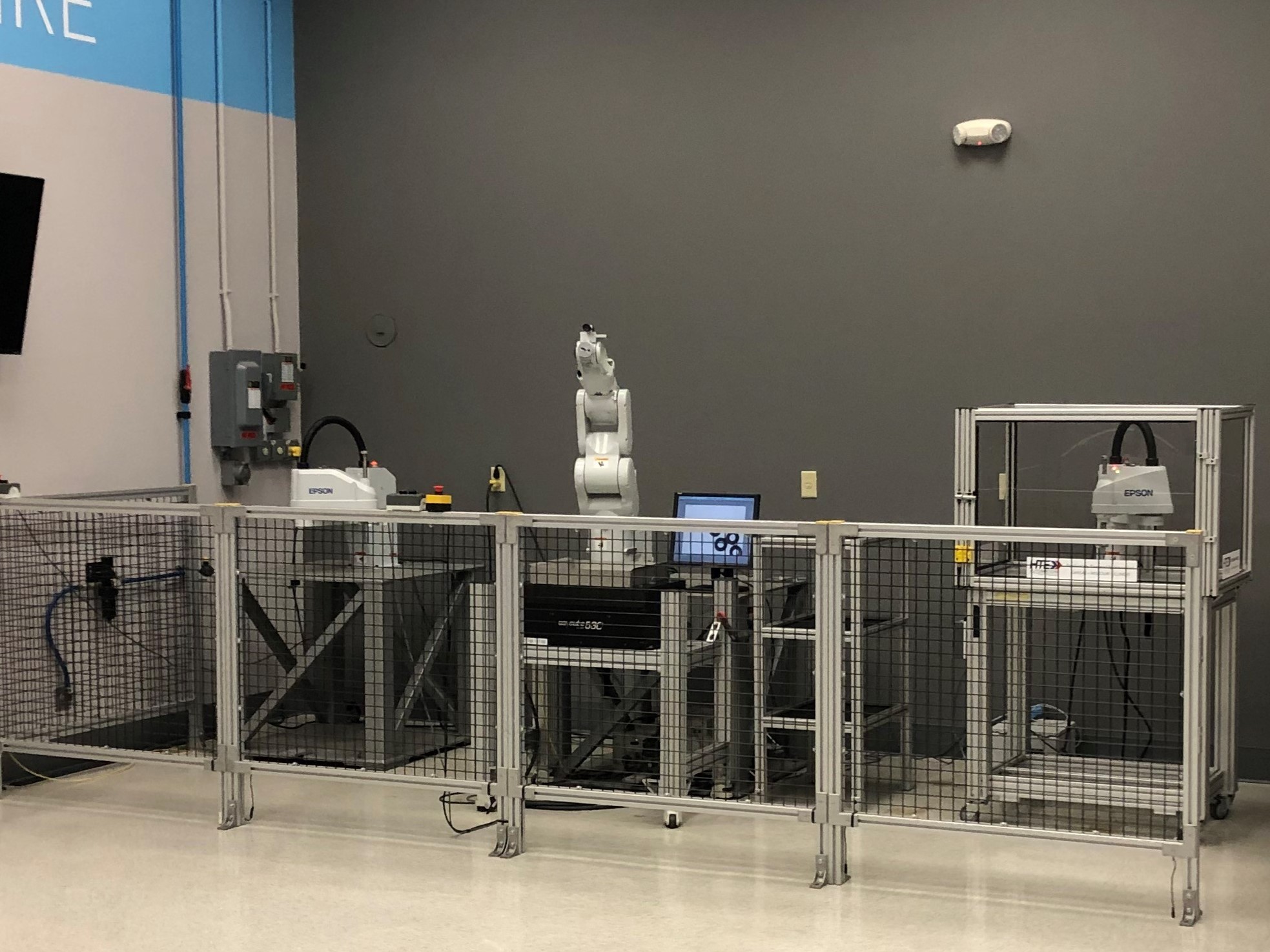
In this article, we’ll walk through ten frequent mistakes companies make with machine guarding and explain how to avoid them. Whether you’re setting up new equipment or retrofitting an existing system, these tips can help reduce risk, improve productivity, and ensure your facility meets OSHA and ISO standards.
1. Overlooking a Formal Risk Assessment
Jumping straight into guard installation without first identifying potential hazards is a misstep that can lead to dangerous blind spots. A thorough risk assessment should always be the first step, highlighting exposure points like shear zones, moving parts, and pinch points. Once hazards are clearly defined, appropriate guarding—such as light curtains, safety mats, or fencing—can be selected and positioned accordingly.
2. Placing Guards Too Close to the Hazard
Safety devices and guarding must be installed in the correct location. If protective equipment like light curtains or presence-sensing mats are positioned too close to a machine’s hazard area, the system might not stop the equipment in time to prevent injury. Calculating the proper safety distance is critical to maintaining both protection and productivity.
3. Skipping Functional Testing and Regular Checks
Even high-quality safety devices can become ineffective without proper maintenance. After installation, all safety systems should be tested to ensure correct operation—and those tests shouldn’t stop there. Integrating regular checks into your maintenance routine helps identify failures early and keeps your facility safe and compliant. Learn more about JHFOSTER’s maintenance services.
4. Failing to Integrate with Safety Controllers
When safety devices function independently, response times can be slower and diagnostics less reliable. Connecting your guarding systems to a centralized safety controller or PLC ensures synchronized responses and real-time alerts, streamlining both operations and compliance tracking.
5. Using Incompatible or Legacy Equipment
Pairing new safety devices with outdated controls or components often leads to miscommunication or system failure. Ensure that your equipment is not only compatible but also up to current regulatory standards. JHFOSTER, offers automation integration services to modernize your setup without sacrificing reliability.
6. Ignoring the Operating Environment
Guarding solutions must be tailored to their surroundings. For example, certain materials may break down in high-heat or washdown areas. Always select components that are engineered for the specific demands of your facility, whether it involves chemicals, moisture, heat, or heavy debris.
7. Neglecting Maintenance and Calibration
Sensors, switches, and mats degrade over time. If they aren’t inspected and calibrated regularly, their effectiveness will diminish. Scheduling preventative maintenance and incorporating functional testing into your standard operating procedures helps ensure continued protection.
8. Not Providing Employee Training
Safety devices are only as effective as the people who interact with them. Without clear training, workers may override, bypass, or misuse guarding systems creating unintended risks.
9. Designing a System That Can’t Scale
As your operations grow, your safety systems should evolve, too. When you choose non-scalable equipment or limit system capacity, you’re setting yourself up for expensive and time-consuming retrofits later. Modular, expandable safety systems are a smart investment in future flexibility.
10. Misunderstanding Regulatory Requirements
Many safety violations stem from a lack of clarity around compliance. OSHA, ISO 13849, and ANSI B11 standards can be complex and assuming your system meets them without verification can be costly. Partnering with automation experts ensures your system is properly documented, installed, and inspected.
Partner with JHFOSTER for Safer Systems
Avoiding common machine guarding mistakes isn’t just about compliance. It’s about building a safer, smarter facility. JHFOSTER offers end-to-end solutions to help you:
- Conduct complete hazard and risk assessments
- Install light curtains, interlock switches, and safety mats
- Integrate safety devices into your control architecture
- Choose durable components for your specific environment
- Train your workforce and perform ongoing system audits
Request Machine Safety Assessment information or call us at 855.688.0065 to speak with a safety expert.
Looking to upgrade or expand your system? Browse our full selection of machine guarding and safety automation products today.